What is a Cryogenic Valve
A cryogenic valve is a critical device specifically designed to operate under extremely low-temperature conditions, typically below -40℃. It is used in applications such as gas liquefaction, separation, transportation, and storage, with operating temperatures reaching as low as -270℃. Common types of cryogenic valves include gate valves, globe valves, check valves, ball valves, butterfly valves, and throttling valves.
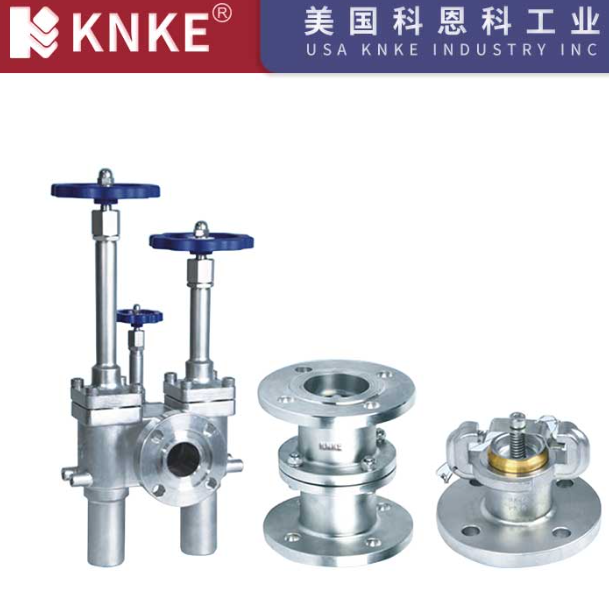
In recent years, cryogenic valves have found increasing application in industries such as petrochemicals, air separation, and natural gas, becoming indispensable in these sectors. The media in cryogenic conditions often have extremely low temperatures and may possess toxic, flammable, explosive, and high permeability characteristics, which impose stringent requirements on material selection, structural design, and manufacturing processes. Cryogenic valves must not only maintain stable performance under extremely low temperatures but also ensure reliable operation under ambient conditions.
Differences Between Cryogenic Valves and Conventional Valves
Cryogenic valves differ significantly from conventional valves in their design. Firstly, cryogenic valves typically employ extended stems and elevated packing boxes to minimize heat transfer from the external environment into the system, ensuring that the temperature of the packing box remains above 0℃. This design ensures proper functioning of the packing and effectively prevents the stem and upper parts of the bonnet from frosting or freezing in low-temperature environments.
Additionally, the long-neck bonnet design of cryogenic valves is crucial to their reliable performance, especially the precise calculation of the neck length L. L represents the distance from the bottom of the packing box to the top surface of the upper seal, and its length is influenced by factors such as the thermal conductivity of the material, heat conduction area, and surface heat dissipation coefficient. The calculation process is complex and often determined through experimental methods.
Material Selection for Cryogenic Valves
Material selection is fundamental to ensuring the reliable operation of cryogenic valves under extreme conditions. Typically, when the operating temperature is above -100℃, ferritic stainless steel is considered suitable. For temperatures below -100℃, austenitic stainless steel is preferred due to its excellent toughness and strength at extremely low temperatures. In addition, copper alloys or aluminum alloys are reasonable choices for low-pressure and small-diameter valves.
The design of the cryogenic valve body must also take into account the impact of thermal expansion and contraction due to temperature fluctuations, ensuring that the valve does not undergo permanent deformation. In particular, the valve seat structure must possess sufficient strength and toughness to withstand mechanical stress caused by temperature changes.
Applications of Cryogenic Valves
Cryogenic valves are widely used in liquefied natural gas (LNG) plants, liquid nitrogen storage systems, air separation units, and petrochemical enterprises. These industries impose stringent requirements on the sealing performance, anti-brittleness of materials, and structural stability of cryogenic valves to ensure the safe and efficient control of fluid media under cryogenic conditions.
Cryogenic valves have a wide range of applications in extreme low-temperature environments and are essential components in industries such as petrochemicals and natural gas. Due to the unique requirements of their operating conditions, cryogenic valves have high standards for material selection and structural design during the design and manufacturing process. By optimizing materials, structure, and heat dissipation design, cryogenic valves can maintain stable performance at extremely low temperatures while also exhibiting excellent functionality under ambient conditions, thus playing a key role in low-temperature industries.
To ensure optimal performance, it is crucial to consider the properties of the working medium, operating temperature, and relevant process parameters when selecting cryogenic valves, thereby guaranteeing long-term stable operation and safety of the equipment.