Types and Selection of Pressure Reducing Valves
A pressure reducing valve is a control valve that adjusts the inlet pressure to a desired outlet pressure and maintains stability of the outlet pressure through the medium’s own energy. In pneumatic control systems, the pressure reducing valve serves as a key auxiliary component, primarily used to reduce and stabilize the pressure of the air supply to ensure that the control valve receives a stable power source for precise regulation. There are various types of pressure reducing valves on the market, and this article will analyze three common types and discuss how to select a suitable pressure reducing valve for specific applications.
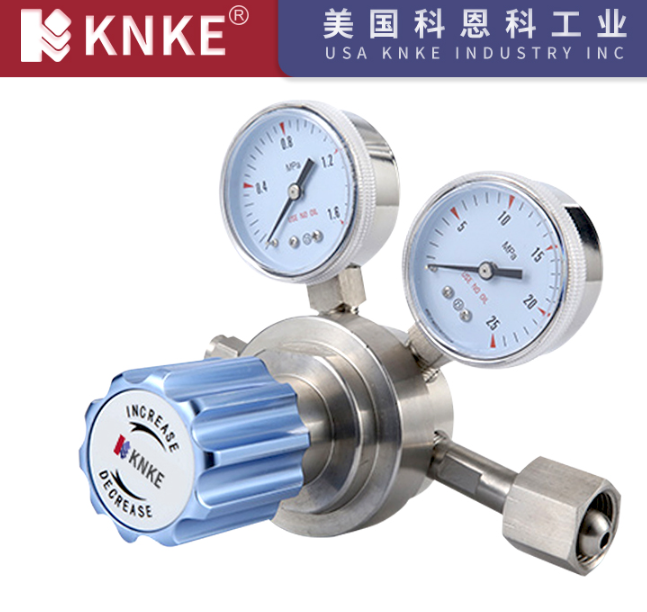
Common Types of Pressure Reducing Valves
The pressure reducing valves widely used in the current market mainly include direct-acting pressure reducing valves, piston-type pressure reducing valves, and diaphragm-type pressure reducing valves. These valves have different structures, working principles, and application scenarios, as detailed below.
1. Direct-Acting Pressure Reducing Valve
The direct-acting pressure reducing valve is the simplest type of pressure reducing valve, typically composed of a flat diaphragm or bellows that directly acts on the inlet pressure to regulate the outlet pressure. Due to its simple structure, it does not require the installation of an external sensing line downstream. This type of pressure reducing valve is compact, cost-effective, and suitable for low to medium flow applications. Its accuracy is generally within ± 10% of the downstream set point.
2. Piston-Type Pressure Reducing Valve
The piston-type pressure reducing valve combines the functions of a pilot valve and a main valve, with the pilot valve design similar to that of a direct-acting pressure reducing valve. The exhaust pressure generated by the pilot valve acts on the piston, driving the main valve to open. When the main valve is large and difficult to open directly, inlet pressure is used to assist in opening the main valve. Compared to direct-acting pressure reducing valves, the piston-type pressure reducing valve has a greater flow capacity and higher accuracy, typically achieving an accuracy of ± 5% under the same pipe size conditions. Similarly, it does not require the installation of an external sensing line, as it can sense pressure internally.
3. Diaphragm-Type Pressure Reducing Valve
The diaphragm-type pressure reducing valve uses a double diaphragm structure instead of a piston, with the increased effective diaphragm area driving the larger main valve to open. Under the same pipe size conditions, its capacity generally exceeds that of the piston-type pressure reducing valve. Moreover, the dual diaphragm is more sensitive to pressure changes, achieving an accuracy of up to ± 1%. Since the downstream sensing line of the diaphragm-type pressure reducing valve is installed externally, it can more accurately sense downstream pressure, making it particularly suitable for high-precision control applications. The diaphragm-type pressure reducing valve can also be flexibly configured with different types of pilot valves, such as pressure valves, temperature valves, and solenoid valves, to meet diverse application needs.
Guide to Selecting a Pressure Reducing Valve
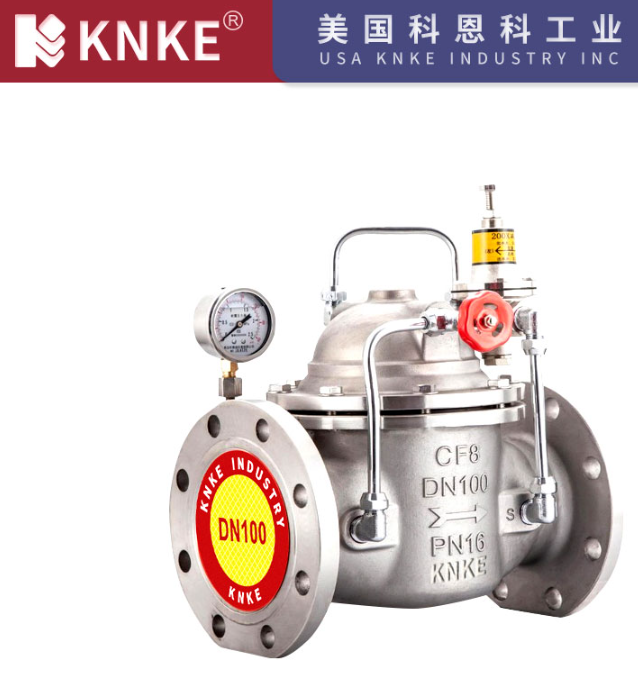
When selecting a pressure reducing valve, multiple factors must be comprehensively considered to ensure that it can adapt to the expected working environment and operate stably and efficiently. The main steps for selecting a pressure reducing valve are as follows:
- Clarify Purpose and Working Conditions: First, clarify the specific purpose of the pressure reducing valve in the equipment or system and determine the applicable medium type, working pressure range, and working temperature.
- Determine Connection Method and Pipe Size: Based on the nominal diameter of the pipe and the specific connection method (such as flange, thread, or welding), select a suitable pressure reducing valve.
- Determine Operation Method: According to actual needs, determine the operation method of the pressure reducing valve, including manual, electric, solenoid, pneumatic, or hydraulic operation.
- Select Valve Body Material: Select appropriate valve body and internal component materials according to the nature of the pipeline medium, pressure, and temperature conditions. Common materials include cast steel, stainless steel, alloy steel, and gray cast iron.
- Select Type of Pressure Reducing Valve: Choose the appropriate type of pressure reducing valve, such as direct-acting, piston-type, or diaphragm-type, based on application scenarios and working requirements.
- Determine Valve Form and Parameters: Confirm the form and relevant parameters of the pressure reducing valve. For automatic steam pressure reducing valves, it is necessary to consider allowable flow resistance, discharge capacity, and back pressure, to determine the nominal diameter of the pipe and the diameter of the valve seat.
- Determine Geometric Parameters: This includes the structural length, flange connection type and dimensions, valve height in open and closed states, and the dimensions and number of connecting bolt holes.
The process of selecting a pressure reducing valve requires comprehensive consideration of various factors such as purpose, working conditions, connection method, operation method, and material. Understanding the characteristics of direct-acting, piston-type, and diaphragm-type pressure reducing valves allows users to select the most suitable valve according to specific application requirements, thereby ensuring the safety and stability of the equipment. In the actual selection process, precision requirements, usage environment, and ease of installation should also be further considered to achieve optimal system performance.