Troubleshooting Turbine Flow Meters: An Engineer’s Guide
Turbine flow meters are widely used in various industrial sectors, especially in oil and gas, chemical, and water treatment industries, as precise instruments for flow measurement. However, like all mechanical devices, turbine flow meters may encounter a range of issues over time. These issues can affect measurement accuracy and lead to production downtime. Understanding common faults and troubleshooting methods is essential for maintaining optimal performance and preventing potential losses. This guide provides engineers with a detailed troubleshooting approach to quickly diagnose and resolve turbine flow meter issues.
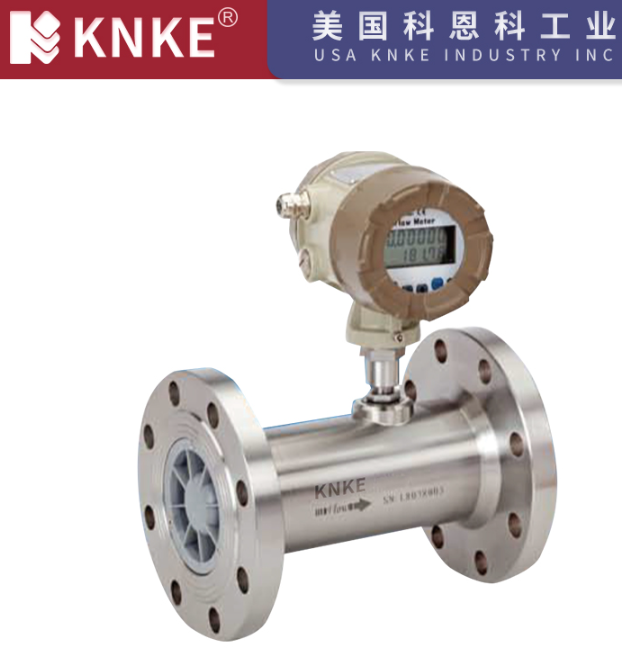
1. Common Turbine Flow Meter Faults and Solutions
Common Issues with Flow Meter Readings
One of the most common faults in turbine flow meters is abnormal readings, such as high, low, or no readings at all. These issues are usually caused by debris or particles inside the flow meter. To prevent this, it is recommended to install filters or filtration devices before using the flow meter to prevent foreign particles from entering the device. It’s important to note that all flow meters may contain small debris or particles that can affect measurement accuracy.
Troubleshooting No Reading
If the turbine flow meter displays no reading, the first step is to check if debris is blocking the turbine from rotating. Foreign particles can obstruct the turbine or magnetic pickup, causing the meter to fail. The solution is to clean the meter and ensure the turbine can rotate freely. If the issue persists, the turbine may be damaged or the bearings may be worn out, requiring further inspection and repair.
2. Low Readings with No Debris Inside
Low Readings with No Visible Debris
If the flow meter displays low readings but there is no visible debris, it could be caused by small debris in the turbine’s coupling. Disassemble the meter and thoroughly check the turbine and bearings for hidden particles like Teflon tape. Additionally, check for damage to the rotor and shaft, as well as external factors such as valve blockages or pipe scaling that may reduce flow.
Troubleshooting Debris-Induced Faults
Debris can lead to one of the following problems:
- No reading (turbine does not rotate)
- Low reading (debris restricts turbine movement)
- High reading (debris passes through the turbine with fluid)
To address these issues, it’s essential to remove all debris inside the meter and inspect the turbine and bearings thoroughly.
3. Increased Flow Rate with Unchanged Pressure
If you observe an increase in flow rate with no corresponding change in pressure, scaling or deposits in the meter or upstream pipeline could be the cause. The accumulation of substances like limescale or wax can increase flow resistance, affecting the accuracy of the flow meter. Inspect both the meter and the pipeline for any deposits and clean them to ensure proper functioning.
4. High Readings Higher than Actual Flow Rate
High readings in a turbine flow meter can be caused by the following factors:
- Partial blockage of the meter’s inlet by debris
- Closed valves or limiting devices upstream, restricting flow
- Flow dividers such as elbows or tees being too close to the meter, affecting fluid viscosity
- Misalignment of gaskets in the meter or piping
- Scaling or buildup inside the meter or pipeline
- Incorrect divisor settings or accumulator malfunctions
To resolve these issues, it’s necessary to check each component of the flow meter and pipeline for blockages, scaling, or damage and make necessary adjustments.
5. Sudden High Readings
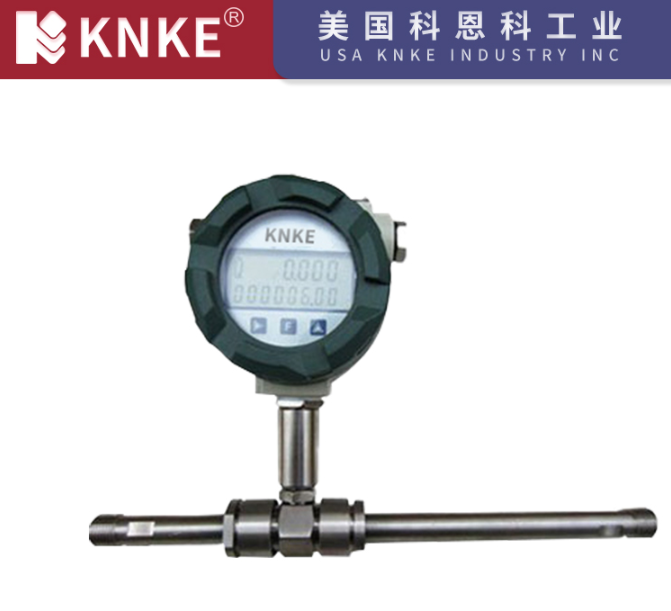
If the turbine flow meter suddenly shows high readings, it could be due to debris trapped at the upstream end of the turbine, or changes in the fluid’s condition, such as gas leakage. The presence of gas or air in the fluid can cause higher readings. Flow control valves should be installed downstream of the meter to prevent interference from gas or air. Also, check for check valve leakage, which may cause the accumulator to display abnormally high readings.
6. Inaccurate Liquid Level Readings
Inaccurate liquid level readings in flow meters are often caused by debris inside the meter, broken shafts, highly viscous fluids, air in the pipeline, or improper installation. To ensure accurate readings, periodically inspect the meter and pipeline for any blockages, and ensure the equipment is installed according to the specifications.
7. When to Replace the Rotor and Blade Kit Due to Bearing Wear
Bearing wear can prevent the turbine rotor from rotating smoothly, particularly when indentations or grooves appear at the ends of the shafts. If the groove covers more than 66% of the shaft’s surface area, the rotor and blade kit should be replaced. If grooves are noticeable on the side of the shaft, the kit should be replaced immediately.
8. How to Check the Pickup
The turbine flow meter typically includes a magnetic pickup to detect rotor movement and generate flow readings. If the pickup is suspected to be faulty, it can be tested using an ohmmeter or by connecting it to a normal working display device. If the pickup is working correctly, the meter should update the flow rate or total reading when a wire brush or screwdriver is passed over the pickup head.
Turbine flow meters are precision instruments that require regular maintenance and troubleshooting to ensure optimal performance. By understanding common faults and their solutions, engineers can more effectively diagnose and repair flow meter issues, ensuring long-term reliability and accuracy. Whether it’s cleaning the meter, replacing worn components, or removing debris buildup, taking proactive steps to address problems will significantly improve the performance and lifespan of turbine flow meters.