Three Common Issues with Metal Tube Rotameters and Their Solutions
Metal tube rotameters are commonly used in industrial applications to measure the flow of liquids and gases. However, several issues can affect their accuracy and stability. This article highlights the three most common problems and offers practical solutions for each.
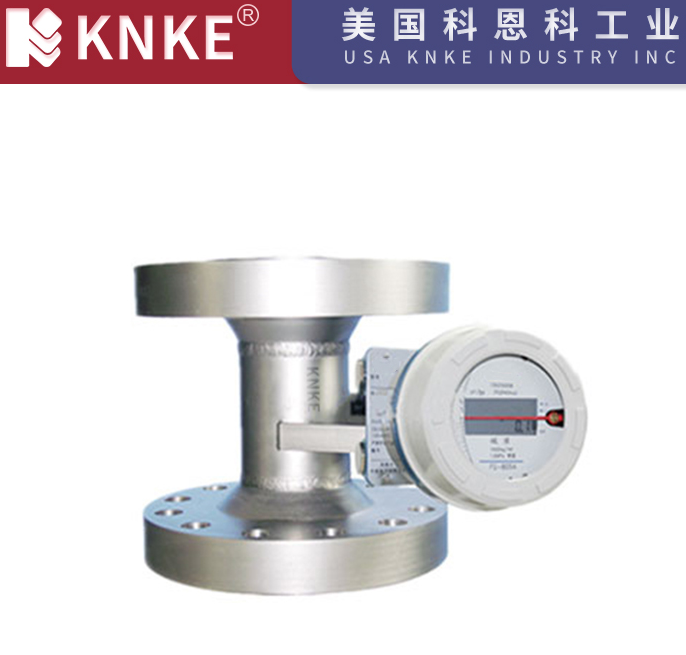
1. Large Measurement Errors in Rotameters
- Impact of Temperature and Pressure on Gaseous Media
Gas flow is highly influenced by changes in temperature and pressure. Without compensation for these variations, errors can arise. To address this, implement temperature and pressure compensation. This technique adjusts the readings in real-time to reflect the actual flow conditions, ensuring more accurate measurements. - Loose Moving Components
Prolonged use or vibrations in the pipeline may loosen components like the magnetic sensor, pointer, counterweight, and rotating magnets. Loose parts can lead to measurement errors. To check, manually push the pointer to the RP position and observe whether the output is 4mA and the flow display reads 0%. If discrepancies are found, adjust the component positions. Professionals should perform these adjustments to avoid misalignment, which could require factory recalibration. - Improper Installation
Installing the rotameter incorrectly often leads to measurement errors. For vertical installations, ensure that the tilt angle does not exceed 20 degrees. For horizontal installations, the meter should remain level with a tilt angle of no more than 20 degrees. Keep ferromagnetic materials at least 100mm away from the meter. Also, install the meter away from valve changes, pump outlets, and pipe bends. Finally, maintain a straight pipe section of 5D before and 250mm after the meter. - Density Variations in Liquid Media
Changes in liquid density can cause errors. Since rotameters are calibrated using the density provided by the user, variations in density during use will impact the readings. To correct this, calculate a correction factor based on the actual density and multiply the measured flow by this factor to obtain the true flow rate.
2. Pointer Flutter in Rotameters
- Severe Pointer Flutter
Severe fluttering is usually caused by fluctuations in the medium or unstable air pressure. In gas flow applications, discrepancies between the operating conditions (pressure, temperature, and flow rate) and the rotameter’s actual state can cause over-range errors. To resolve this, stabilize the pressure or adjust the operating conditions to eliminate fluctuations. - Mild Pointer Flutter
Mild flutter occurs due to medium fluctuations. To counteract this, install damping devices. These devices absorb fluctuations and reduce their impact on the measurement, improving stability. - Moderate Pointer Flutter
Moderate flutter typically occurs due to changes in the medium’s flow state. In gas measurements, unstable operating pressure often causes this issue. Using flow stabilization devices or gas damping mechanisms will help maintain steady readings.
3. Pointer Stopping at a Fixed Position
Pointer stoppage is typically caused by the float becoming stuck. Common reasons include:
- Valve Opening Too Quickly
Opening the valve too quickly causes the float to rush upwards, hitting the stopper and deforming it. This deformation may trap the float. To resolve this, inspect the stopper for deformation and reshape it if necessary. - Misalignment of the Float Guide Rod and Stop Ring
If the float guide rod and stop ring are not concentric, the float may become stuck. To fix this, disassemble the meter and check the alignment. Correct any misalignment and reassemble the meter. - Improper Installation
Installing the rotameter at an incorrect angle, especially a tilt, can cause the float to get stuck. Always install the meter either vertically or horizontally without tilting to prevent this issue.
Metal tube rotameters are reliable instruments for measuring flow, but issues like measurement errors, pointer flutter, and float jamming can arise. By employing temperature and pressure compensation, regularly checking moving components, ensuring proper installation, and using damping or stabilization devices, you can minimize these problems. Taking these steps will help maintain the meter’s accuracy and stability, ensuring efficient and precise industrial operations.