The Relationship Between Stainless Steel Centrifugal Pump Pipe Diameter and Head
Stainless steel centrifugal pumps are widely used in industrial applications such as chemical, petroleum, and pharmaceutical industries due to their compact design, low operating costs, and ease of use. These pumps are versatile, offering the flexibility to handle various flow rates, heads, and different types of media. However, there are still many misconceptions about the relationship between pipe diameter and head in centrifugal pumps. This article will clarify the relationship between pipe diameter and head, providing a better understanding of how to optimize pump performance.
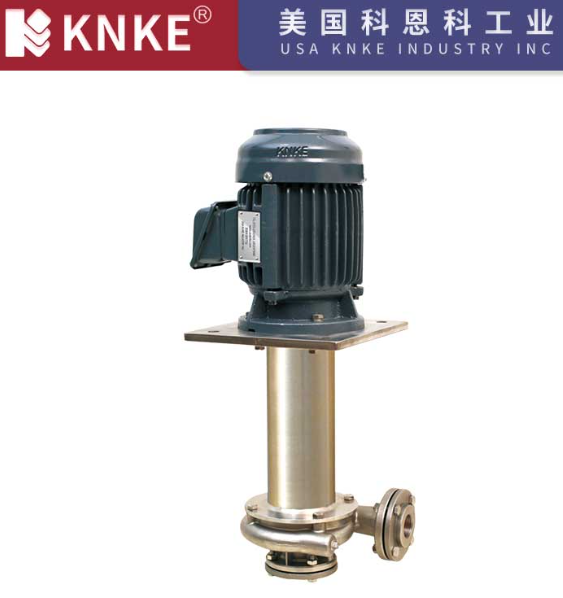
1. Total Head and Loss Head: What You Need to Know
In centrifugal pumps, the total head is the maximum pressure increase the pump can provide. The loss head, on the other hand, is the pressure drop due to friction in the pipes, valves, and other components of the system. The total head is determined by the pump’s design, while the loss head is influenced by the system’s piping layout, pipe diameter, and other factors.
The actual head of the pump is the difference between the total head and the loss head. Understanding how pipe diameter impacts the loss head is key to optimizing pump performance and efficiency.
2. How Pipe Diameter Affects Head and Pump Efficiency
Many people believe that using larger diameter pipes with smaller pumps increases the head. However, this is a common misconception. In reality, the relationship between pipe diameter and head is more complex. The head of a pump is determined by two factors: the pump’s total head and the head loss due to pipe resistance. As per the following formula:
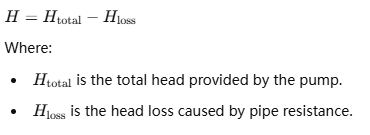
For a given pump, the total head remains constant, but the head loss increases with smaller pipe diameters. Let’s explore this in more detail.
1. Effects of Reducing Pipe Diameter:
When a centrifugal pump uses smaller diameter pipes, the resistance in the system increases, which raises the loss head. This means the actual head the pump can provide decreases. Although it might seem that reducing the pipe diameter increases the pump’s pressure, in fact, the pump efficiency drops because more energy is wasted in overcoming the higher resistance.
2. Effects of Increasing Pipe Diameter:
On the other hand, when you increase the pipe diameter, the resistance decreases, reducing the loss head and allowing the pump to operate more efficiently. This increase in pipe diameter helps to increase the pump’s actual head, enhancing its overall performance. While a larger pipe diameter may require more power to push higher flow rates, the reduced energy loss typically results in improved efficiency for the entire system.
3. Addressing the Misconception About Motor Load with Larger Pipe Diameters
Another common misconception is that increasing the pipe diameter will significantly increase the motor load on the pump. The belief is that larger pipes exert more pressure on the pump impeller, which in turn increases the motor load. However, the pressure exerted on the pump impeller is determined by the head, not the pipe diameter. As long as the head remains constant, the pressure on the impeller remains the same, regardless of the pipe diameter.
Increasing the pipe diameter actually reduces the energy losses caused by friction, which results in lower operating costs and better overall pump efficiency. This means that, contrary to popular belief, increasing pipe diameter does not increase motor load but can reduce the overall system’s energy consumption.
4. How to Select the Optimal Pipe Diameter for Your Pump
Selecting the right pipe diameter is crucial for maximizing pump performance and minimizing energy consumption. An appropriately sized pipe reduces the friction losses and ensures that the system operates within the desired flow rate and head parameters. Here are a few key considerations:
- Flow Rate: Ensure the pipe diameter supports the required flow rate without causing excessive pressure loss.
- Head Requirements: A correctly sized pipe will help maintain the desired head while minimizing losses.
- System Design: The layout of your piping system, including length and material, should influence your pipe diameter choice.
Choosing a pipe diameter that is too small results in excessive resistance, which lowers pump efficiency. On the other hand, an oversized pipe may reduce flow velocity, causing the pump to work less effectively. Therefore, it is essential to balance the pipe size with the pump’s capabilities and the overall system’s requirements.
5. Conclusion: The Importance of Pipe Diameter in Pump Efficiency
Understanding the relationship between pipe diameter and head is essential for optimizing the performance of stainless steel centrifugal pumps. Pipe diameter influences the head loss, and by selecting the right diameter, you can improve pump efficiency, reduce energy consumption, and achieve better system performance. Contrary to popular belief, increasing the pipe diameter does not increase the motor load but instead reduces friction losses, leading to a more efficient pump system.
For industrial applications, the correct pipe diameter ensures that your centrifugal pump operates at peak efficiency, saving on operational costs and improving the overall performance of your fluid handling system.