The Difference Between Stainless Steel Pumps and Aluminum Alloy Pumps
In industrial fluid handling systems, pump material directly affects the equipment’s reliability, service life, and operational cost. Stainless steel pumps and aluminum alloy pumps are two widely used types, each offering distinct advantages based on their material properties, environmental adaptability, and cost efficiency. This article provides a comparative analysis to support informed pump selection decisions.
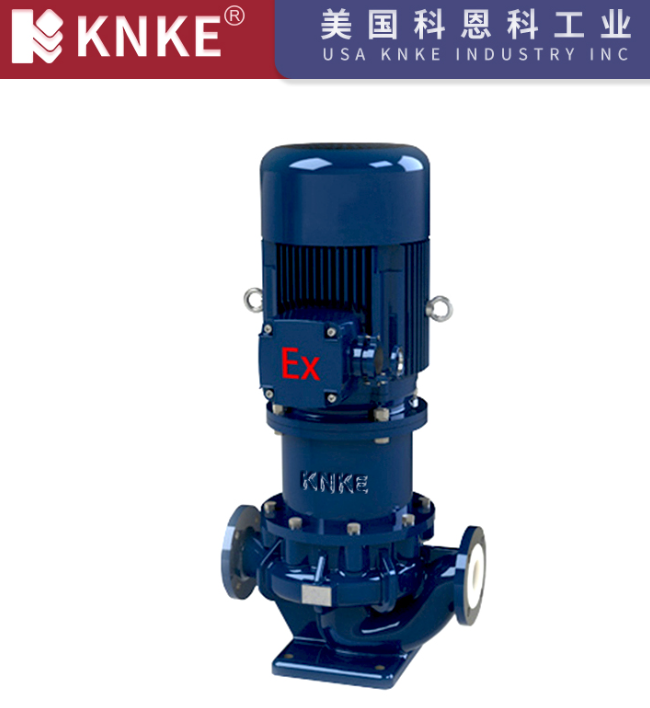
1. Material Performance Comparison
Stainless Steel Pumps
Typically made from 304 or 316L austenitic stainless steel, these pumps feature high tensile strength (≥520 MPa) and exceptional corrosion resistance. They perform reliably in acidic and alkaline media with a pH range of 2–11 and can withstand temperatures from -20°C to 200°C. A passive film on the surface protects against chloride-induced corrosion, making them highly durable in salt spray environments.
Aluminum Alloy Pumps
Manufactured from casting alloys such as ADC12 and A356, aluminum pumps are lightweight—approximately 40% to 50% lighter than stainless steel—with a density around 2.7 g/cm³. However, they offer lower yield strength (200–250 MPa) and limited corrosion resistance. Surface anodizing can improve durability, but exposure to acidic or alkaline substances (ideal pH range: 5–9) may lead to pitting corrosion. Their maximum operating temperature is around 120°C.
2. Application Field Analysis
Chemical and Pharmaceutical Industry
Stainless steel pumps dominate due to their resistance to corrosive media and high temperatures. For example, in systems handling hydrochloric acid with chloride ions or ammonium sulfate solutions, 316L pumps can operate reliably for 8–10 years. One chemical plant reduced pump failure rates by 75% after switching to stainless steel.
Automotive and Mobile Equipment
Aluminum alloy pumps are favored for their lightweight design, widely used in electric vehicle cooling systems. For instance, using A356 aluminum alloy reduced a single water pump’s weight by 1.2 kg, cutting total energy consumption by 3%. However, these pumps must be used with glycol-based coolants to prevent galvanic corrosion from water exposure.
Food Processing Industry
Stainless steel pumps meet FDA hygiene standards and are often mirror-polished (Ra ≤ 0.8 μm) to eliminate microbial residue, making them ideal for dairy and aseptic filling lines. In contrast, aluminum alloys may release metal ions and are typically limited to non-contact auxiliary applications in food systems.
3. Cost and Lifecycle Performance
In terms of upfront cost, stainless steel pumps are generally 2–3 times more expensive than their aluminum counterparts. However, stainless steel significantly reduces maintenance needs and replacement frequency in corrosive environments. A coastal power plant reported that over 10 years, the total cost of using 304 stainless steel pumps was 42% lower than using aluminum alloy pumps, including spare parts and labor.
4. Selection Recommendations and Conclusion
Choosing the right pump material involves balancing performance with cost:
- For corrosive, high-temperature, or hygienic environments, stainless steel pumps are the optimal choice due to their longevity and stability.
- For light-duty or mobile applications in neutral environments, aluminum alloy pumps offer cost and weight advantages.
For example, when transporting food-grade sodium chloride solutions, even with a 40% increase in cost, 316L stainless steel pumps remain the better long-term solution due to safety and durability.
Selecting the proper pump material is a strategic decision that affects both initial investment and long-term operational performance. Understanding the differences between stainless steel and aluminum alloy pumps helps engineers and procurement teams make informed, cost-effective choices tailored to their specific industrial needs.