The Difference Between Cast and Forged Valves: Key Factors to Consider
When selecting a valve for industrial applications, the choice between cast and forged valves is crucial. These two manufacturing processes differ significantly in their production methods, performance, structure, and application suitability. Understanding the key differences can help engineers and decision-makers choose the right valve for their specific needs. This article will explain the distinctions between cast and forged valves, highlighting their advantages and disadvantages.
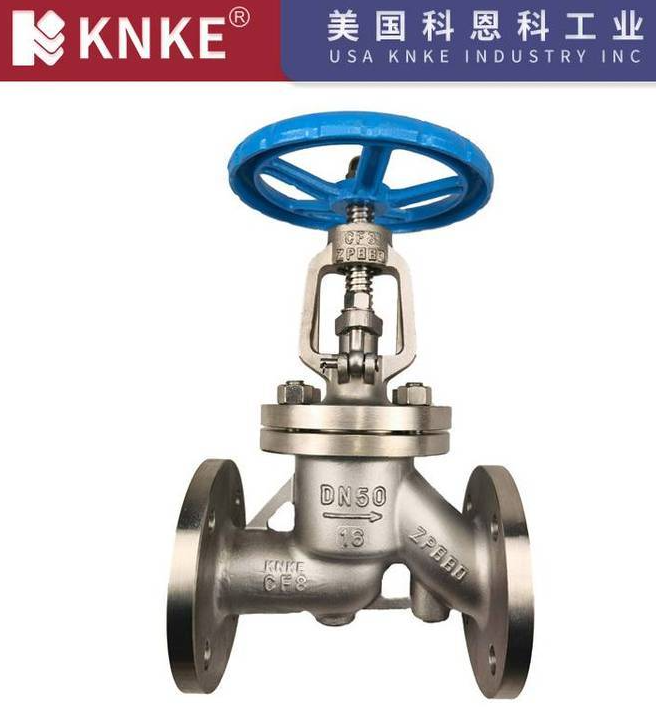
I. What Are Cast Valves?
Casting is a process in which molten metal is poured into a mold and allowed to cool, forming the desired shape. This method has a long history, dating back over 6,000 years, and remains essential for producing parts with complex geometries, especially those with internal cavities. Today’s casting technologies use a variety of alloys to create castings with high strength.
Cast valves are made using this casting method. The primary advantage of cast valves is their ability to produce intricate shapes at a lower cost compared to other methods. Additionally, cast valves provide uniform stress distribution, making them suitable for a broad range of applications.
Key Features of Cast Valves:
- Cost-Effective: Casting is ideal for producing valves in large volumes. It is especially efficient for making complex shapes.
- Material Flexibility: Cast valves can be made from various alloys, including cast iron and cast steel.
- Uniform Stress Distribution: Cast valves are designed to withstand pressure from multiple directions.
- Complex Geometries: Casting is effective for creating parts with complex internal structures.
However, the casting process can introduce defects such as gas porosity, cracks, or shrinkage, which may compromise the strength and sealing ability of the valve. Moreover, casting requires a wide range of materials and equipment, leading to environmental concerns such as dust and emissions.
II. What Are Forged Valves?
Forging involves applying pressure to a metal billet, causing it to deform plastically and achieve the desired shape. This process removes internal defects like porosity, resulting in parts with superior mechanical properties. Forged valves are typically used in high-pressure, high-temperature, or heavy-load applications due to their strength and structural integrity.
Forged valves are often made from high-grade steels or alloys, providing exceptional performance in demanding environments. The forging process improves the metal’s tensile strength and resistance to fatigue, making these valves ideal for critical applications.
Key Features of Forged Valves:
- High Strength: Forged valves offer superior tensile and compressive strength, ideal for high-pressure, high-temperature environments.
- Durability: The dense, uniform microstructure of forged valves gives them excellent resistance to fatigue and impact.
- Enhanced Mechanical Properties: The forging process aligns the metal’s grain structure, improving resistance to deformation.
- Ideal for Heavy-Duty Applications: Forged valves excel in industries that require high strength, such as oil and gas, chemicals, and power generation.
However, the forging process is more costly and requires specialized equipment. Forging can also be less cost-effective for producing valves with complex shapes.
III. How to Differentiate Between Cast and Forged Valves
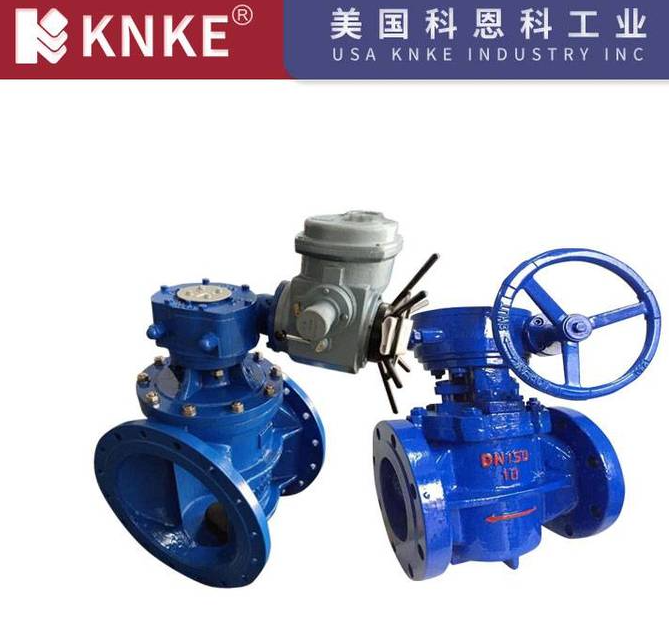
Though both types of valves have distinct production methods, you can easily distinguish between cast and forged valves by looking at certain characteristics:
- Surface Texture: Cast valves have a rougher surface, while forged valves appear smoother and shinier.
- Cross-Sectional Color: Cast valves usually have a dull grayish color, while forged valves have a bright, silvery appearance.
- Sound Test: When struck, forged valves emit a clear, sharp sound. In contrast, cast valves produce a duller, more muffled sound.
- Spark Test: Grinding a forged valve produces bright, long sparks, while cast valves create shorter, dimmer sparks.
These simple tests allow you to identify the type of valve quickly, ensuring you select the appropriate one for your needs.
IV. Applications of Cast and Forged Valves
Due to their differing mechanical properties, cast and forged valves are suited for different industrial applications:
- Cast Valves: Best used in low-pressure and moderate-temperature applications, such as water treatment plants, heating systems, and low-pressure gas pipelines.
- Forged Valves: Designed for high-pressure, high-temperature environments, making them ideal for industries like oil and gas, chemical processing, and power generation.
In summary, cast valves work well for simpler applications with moderate pressure, while forged valves are better suited for high-performance applications where strength and durability are paramount. Choosing the right valve ensures improved performance and longevity in your industrial systems.
The differences between cast and forged valves come down to their manufacturing processes, material properties, and intended applications. Cast valves are cost-effective and suitable for producing complex shapes, while forged valves are ideal for high-strength, high-performance applications. Understanding these differences will help ensure you select the right valve for your project, maximizing efficiency and safety.