Solutions to External Leakage Problems in Electric Control Valves
In industrial production, electric control valves are crucial components in pipeline transport systems. They directly impact production efficiency and system safety. However, these valves are often prone to failure. Frequent switching operations, fluid flow erosion, corrosion, and the extrusion of impurities damage the valve sealing surface. This results in pitting, scratches, and other types of damage. Approximately 80% of valve leaks originate from sealing surface damage. Valve leakage leads to medium loss, environmental pollution, production faults, and even serious safety incidents.
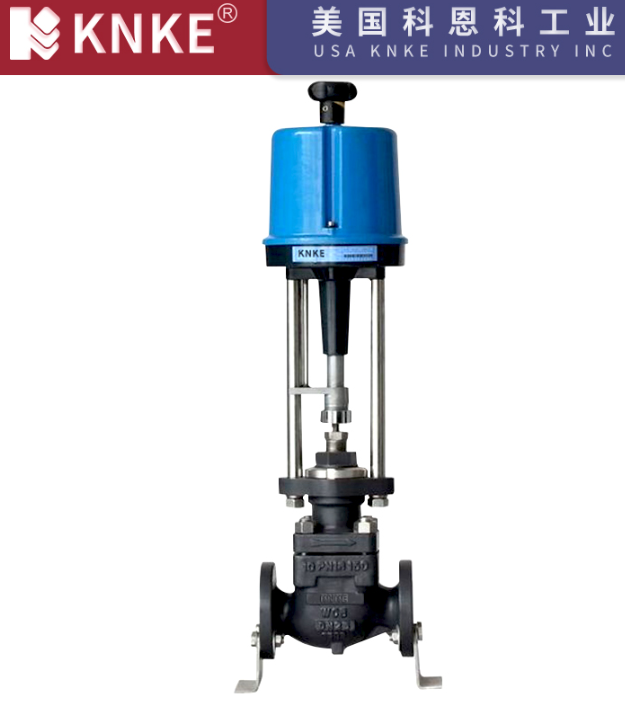
To effectively address external leakage in electric control valves, the following targeted solutions are proposed:
1. Increase Sealing Grease
For valves without sealing grease, adding it can enhance the sealing performance of the valve stem. This approach reduces the risk of leakage and improves sealing reliability and stability.
2. Add Packing
To improve the sealing effect of the packing on the valve stem, additional packing can be used. Typically, dual-layer or multi-layer mixed packing is preferred over simply increasing the quantity of packing. Careful selection and combination of packing materials significantly improve the sealing effect, avoiding the inefficiencies of merely adding more packing.
3. Replace with Graphite Packing
Polytetrafluoroethylene (PTFE) packing often fails in extreme temperature environments, with a fast aging rate and a short service life. Flexible graphite packing overcomes these shortcomings and has a longer service life. Therefore, many factories have replaced PTFE packing with graphite packing. Even new control valves undergo similar modifications. However, graphite packing may exhibit hysteresis or crawling behavior initially, and preventive measures should be taken.
4. Change Flow Direction to Place P2 at the Valve Stem End
When the pressure differential (ΔP) is large and the high-pressure side (P1) is at the valve stem end, ensuring effective sealing can be challenging. Changing the flow direction and placing the low-pressure side (P2) at the valve stem end enhances the valve’s sealing performance. This approach is particularly effective for high-pressure, high differential pressure control valves. For bellows valves, priority should be given to sealing the low-pressure side (P2) to reduce leakage risks.
5. Use Lens Gasket Sealing
Flat seals used for sealing the valve bonnet and between the valve seat and body often fail under high-temperature and high-pressure conditions, leading to leakage. Replacing flat seals with lens gasket sealing can significantly improve sealing performance and prevent external leakage.
6. Replace Sealing Gaskets
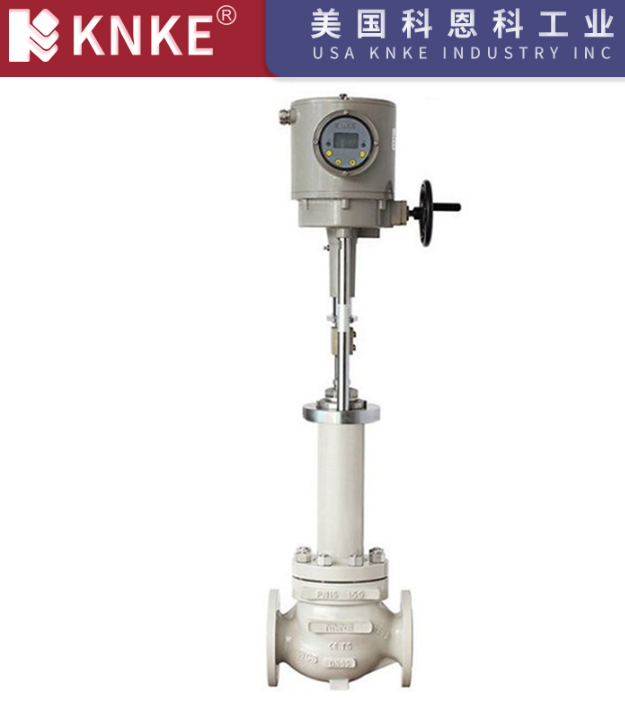
Many traditional sealing gaskets still use asbestos boards, which perform poorly under high-temperature conditions. These gaskets age quickly and lead to leakage. Spiral wound gaskets or “O” rings are more advanced sealing materials that demonstrate excellent sealing performance under high temperatures and have a longer service life. This has led to their widespread adoption in many factories.
Electric control valves may be small, but they play a vital role in industrial systems. Their sealing performance directly affects production efficiency, environmental safety, and equipment stability. By increasing sealing grease, optimizing packing structure, and selecting higher-quality sealing materials, leakage issues in control valves can be effectively addressed. For production enterprises, focusing on valve maintenance reduces leakage risks and ensures a safe and efficient production process.
Optimizing the sealing technology of electric control valves allows enterprises to improve overall production efficiency, reduce downtime, and enhance product quality, gaining a competitive advantage in an increasingly fierce market.