Screw Pump Maintenance Guide
The screw pump, as a critical fluid transfer device, is widely used in various industrial environments. Its efficient and reliable operation directly affects the stability and safety of the entire system. Therefore, systematic maintenance is crucial to ensure the long-term stable operation of the screw pump and extend its service life. Below are several key recommendations and considerations for the maintenance of screw pumps, aimed at improving the scientific management of the equipment and standardizing operations.
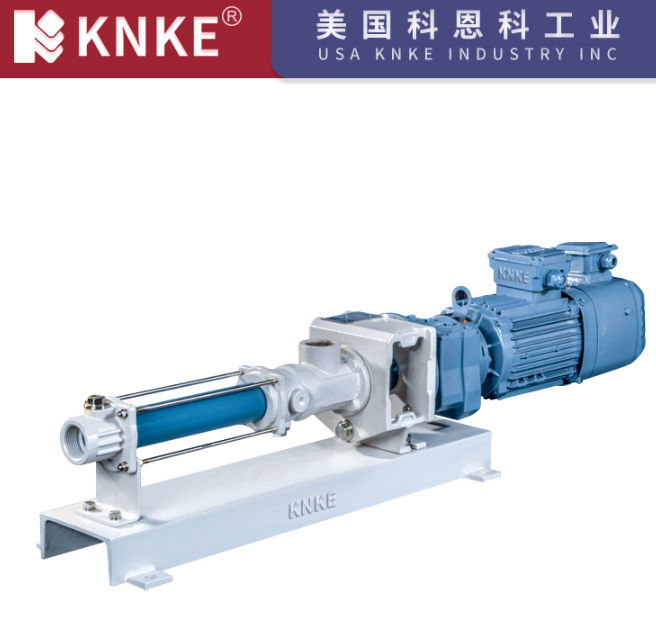
1. Emergency Shutdown Measures for Abnormal Noise and Current
During the operation of the screw pump, if abnormal noise is observed from the pump or motor, or if the ammeter pointer rises sharply, the pump should be stopped immediately to identify and rectify the cause of the issue. Such abnormalities may be caused by foreign objects inside the pump, bearing failures, or pipeline blockages. Promptly addressing these issues is essential to prevent further equipment damage and reduce downtime.
2. Monitoring and Controlling Outlet Pressure
The outlet pressure of the screw pump must not exceed the maximum allowable value indicated on the nameplate. Exceeding this pressure limit can not only reduce the efficiency of the pump but also cause severe damage to the equipment. Therefore, operators should continuously monitor the pump’s outlet pressure during operation to ensure that it remains within a safe range, thereby avoiding equipment failure and system malfunction due to overpressure.
3. Proper Setting and Management of Safety Valves
The safety valve is a key device that protects the screw pump system from overpressure damage. Safety valves are usually precisely calibrated before leaving the factory and should not be adjusted without authorization. If adjustments are required due to special needs, they must be performed by qualified professionals to ensure that the safety valve can effectively open in case of abnormal system pressure, thus preventing equipment damage or personal injury due to uncontrolled pressure.
4. Pipeline System Faults and Safety Reflux Management
When a pipeline system fault occurs that triggers safety reflux, the pump should be stopped immediately to troubleshoot the fault. Generally, the safety valve reflux time should not exceed three minutes; otherwise, the continuous backflow of liquid in the pump may cause pulsation, leading to pump body vibrations and, in severe cases, the pump seizing or being seriously damaged. Therefore, fault clearance should be completed as quickly as possible to maintain system stability.
5. Monitoring and Maintenance of Shaft Seals
During normal operation, a small amount of liquid leakage from the shaft seal of the screw pump is normal. However, if the leakage exceeds 10 ml/hour, the pump should be stopped to check the condition of the shaft seal to determine if there is any damage or aging, and replace the sealing elements if necessary. Regular maintenance of the shaft seal can effectively prevent liquid leakage from affecting equipment operation, ensuring the proper functioning of the pump.
6. Motor Overload Protection and Automatic Shutdown Devices
To prevent the risk of motor burnout due to pump seizure, it is recommended to install overload protection devices in the motor control circuit. When the pump seizes, the overload protection device should be able to automatically cut off the power supply, effectively protecting the motor and pump from further damage. The installation and maintenance of such protective devices are crucial for ensuring equipment safety, especially in conditions involving frequent start-stop cycles.
Frequently Asked Questions
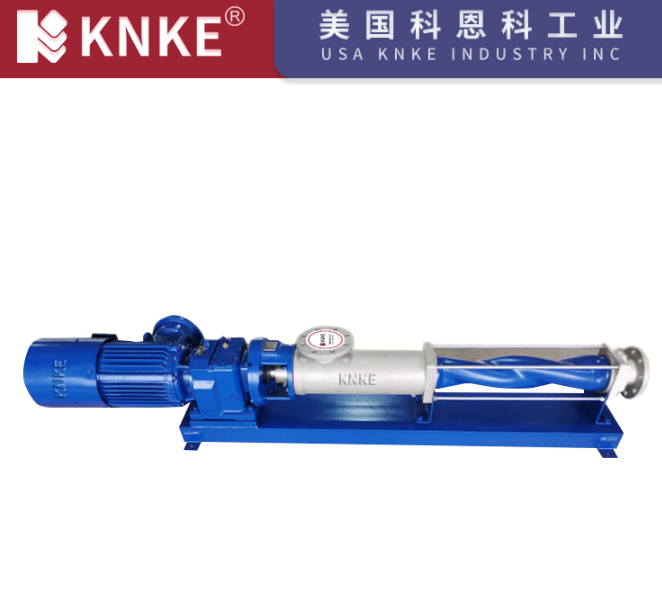
1. How to Determine If the Screw Pump Requires an Emergency Shutdown?
If abnormal noise is observed from the pump or motor during operation, or if the ammeter pointer rises sharply, these are signals that an emergency shutdown is required. The pump should be stopped immediately to determine the cause of the issue and prevent further equipment damage.
2. Why Must the Outlet Pressure of the Screw Pump Be Controlled Within a Safe Range?
If the outlet pressure of the screw pump exceeds the maximum allowable value on the nameplate, it will not only reduce the efficiency of the equipment but may also cause severe damage. Strictly controlling the outlet pressure within a safe range is crucial for ensuring operational safety and extending the service life of the equipment.
3. How Does the Safety Valve Ensure System Safety?
The safety valve is an important device for protecting the screw pump system from overpressure damage. Its set value is usually calibrated before leaving the factory and should not be adjusted without authorization. The safety valve can effectively open when there is an abnormal increase in system pressure, preventing equipment damage or personal injury due to uncontrolled pressure.
4. What Impact Do Pipeline System Faults Have on the Screw Pump?
Pipeline system faults may lead to the activation of safety reflux. If the reflux time exceeds three minutes, it may cause the pump body to vibrate or even seize, resulting in severe damage. Therefore, pipeline system faults should be eliminated as soon as possible to maintain the normal operation of the screw pump.
5. Is Leakage at the Shaft Seal Normal?
A small amount of leakage at the shaft seal is normal, but if the leakage exceeds 10 ml/hour, it is necessary to stop the pump and check for damage or aging of the sealing components. Timely replacement is needed to prevent the leakage from affecting the normal operation of the equipment.
6. Why Is It Necessary to Install a Motor Overload Protection Device?
The motor overload protection device can automatically cut off the power supply when the pump seizes, effectively protecting the motor and pump from further damage. Installing an overload protection device is particularly important for ensuring safe operation in conditions involving frequent start-stop cycles.
In conclusion, strictly adhering to these maintenance measures can significantly improve the reliability and service life of screw pumps. Regular inspection and maintenance of the equipment can effectively reduce the probability of faults and ensure the continuity of production processes and the safety of system operations. Scientific maintenance management is the foundation for ensuring the long-term efficient operation of industrial equipment and is key to enhancing overall system stability.