Reasons for Using Long Neck Bonnet in Cryogenic Valves
Cryogenic valves handle low-temperature media, typically ranging from -40°C to -196°C. Common types include cryogenic butterfly valves, cryogenic gate valves, cryogenic ball valves, cryogenic globe valves, cryogenic check valves, and cryogenic throttle valves. These valves are vital for processes involving liquefied natural gas (LNG), liquefied petroleum gas (LPG), ethylene, liquid oxygen, and other cryogenic fluids. To ensure the performance and safety of these valves, manufacturers often use long neck bonnets.
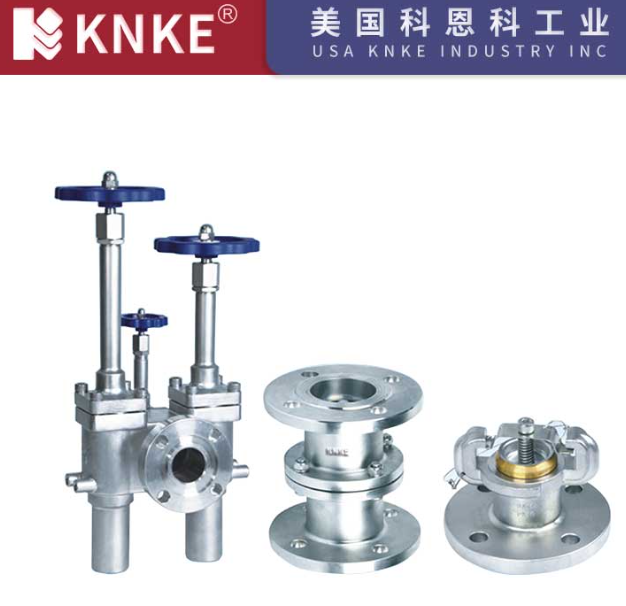
1. Functions and Advantages of Long Neck Bonnet Design
Cryogenic valves use long neck bonnets for several important reasons:
- Protecting the Packing Box and Ensuring Sealing Performance The packing box plays a critical role in the valve’s sealing performance. Proper sealing is essential to prevent cryogenic fluid leakage. When liquid ethylene, liquid nitrogen, and other cryogenic fluids vaporize, they expand rapidly, which can lead to hazardous leakage. As the temperature drops, the packing material loses its elasticity, weakening its ability to prevent leaks. If cryogenic fluid leaks into the packing and valve stem area, it can cause freezing, which interferes with valve operation and damages the packing. A long neck bonnet isolates the low temperature, maintaining a stable packing area temperature and preventing freezing.
- Preventing Cryogenic Energy Loss Maintaining low temperatures is essential for cryogenic valves. The long neck bonnet allows insulation materials to be easily wrapped around the valve, which helps prevent cryogenic energy from escaping. This minimizes the effect of external temperatures and ensures the valve continues to function properly.
- Facilitating Maintenance and Replacement Cryogenic valves are often located in cold boxes, where they are connected to pipelines. The long neck bonnet design makes it easier to disassemble and replace valve components quickly, without removing the entire valve body or re-welding the pipes. This design reduces the risk of leakage from the cold box and simplifies the maintenance process.
2. Manufacturing and Quality Control of Cryogenic Valves
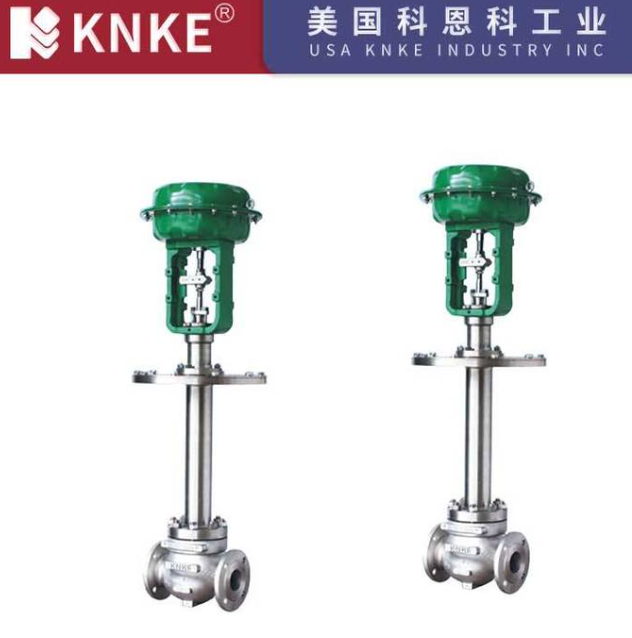
Cryogenic valves operate under extreme conditions, which requires strict standards for materials and manufacturing processes. For instance, German manufacturer WODE applies strict quality controls to ensure their valves’ reliability. They use special cryogenic treatments, immersing components in cooling media for several hours to release stress and improve material performance at low temperatures.
Additionally, the assembly process differs from regular valves. All parts undergo thorough cleaning to remove any oil or contaminants, ensuring the valve performs reliably in cryogenic environments.
Long neck bonnets play a vital role in cryogenic valves. They protect the packing’s sealing performance, minimize energy loss, and make maintenance easier. In applications involving LNG, LPG, and other cryogenic fluids, long neck bonnets help ensure the valve operates safely and efficiently. By adhering to strict manufacturing processes and quality controls, cryogenic valves maintain their performance even under harsh low-temperature conditions.