Principles for Selecting Pressure Reducing Valves
Pressure reducing valves play a crucial role in many industrial and commercial applications by automatically controlling and stabilizing the outlet pressure. To ensure that these valves perform reliably and efficiently, it is essential to follow certain selection principles that match the operating conditions and the properties of the working medium. The following discussion outlines the key principles for choosing the right pressure reducing valve.
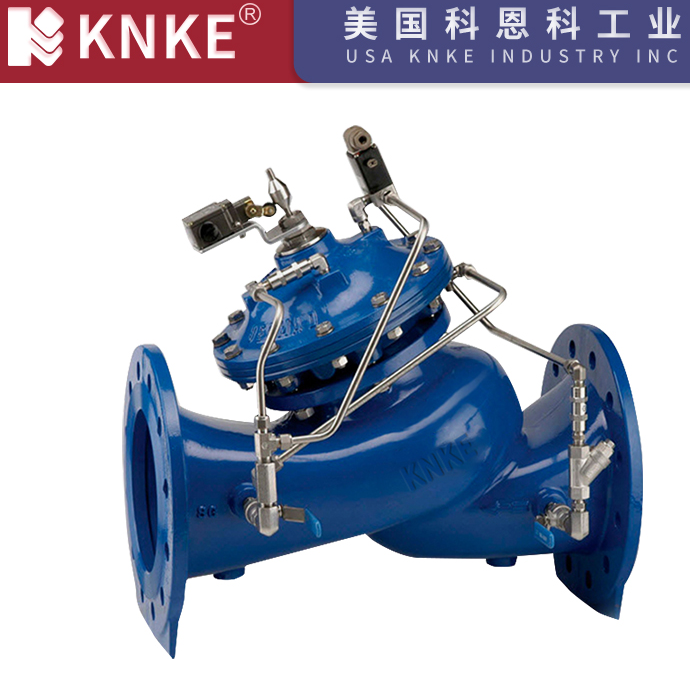
1. Control of Inlet Pressure Fluctuations
A primary consideration in valve selection is the stability of the inlet pressure. The fluctuation of the inlet pressure should be maintained within 80% to 105% of the specified inlet pressure value. Operating outside this range may impair the valve’s performance and affect the stability of the outlet pressure. This guideline ensures that the valve operates under optimal conditions and prevents potential damage or inefficiencies in the system.
2. Downstream Pressure Requirements and Spring Compatibility
Another important principle is ensuring that the downstream pressure (Pc) is appropriately lower than the upstream pressure (P1). Typically, the outlet pressure should be less than half of the inlet pressure (i.e., Pc < 0.5P1). In addition, each stage of the valve’s spring mechanism is designed for a specific range of outlet pressures. When the actual operating pressure falls outside the designated range, it is necessary to replace the spring to maintain proper performance. This approach guarantees that the pressure reduction is both precise and consistent.
3. Valve Selection for High-Temperature Applications
In processes where the working temperature of the medium is relatively high, standard valve designs may not be sufficient. Under these conditions, it is advisable to use pilot-operated valves. Specifically, pilot-operated piston-type or pilot-operated bellows-type pressure reducing valves are preferred. Their design and construction are better suited to handle elevated temperatures, ensuring reliable control of the outlet pressure even under demanding thermal conditions.
4. Selection for Air and Water (Liquid) Applications
When the medium is either air or water, the selection criteria shift to accommodate the characteristics of these fluids. For such applications, direct-acting diaphragm valves or pilot-operated diaphragm pressure reducing valves are generally recommended. These valves are designed to offer stable performance and precise control with lower viscosity fluids, thereby ensuring that the system remains both efficient and responsive.
5. Special Considerations for Steam Applications
Steam presents unique challenges due to its high energy content and thermal properties. In steam applications, the recommended choices are pilot-operated piston-type valves or pilot-operated bellows-type valves. These designs are better capable of managing the dynamic behavior of steam, ensuring that the pressure is reduced effectively while maintaining safety and system integrity.
6. Installation Orientation for Ease of Maintenance
For operational convenience, including ease of adjustment, maintenance, and repair, it is generally recommended that pressure reducing valves be installed on horizontal pipelines. This orientation not only facilitates better access during routine service but also helps maintain the valve’s alignment and performance over time.
Adhering to these selection principles is essential for ensuring that pressure reducing valves operate efficiently and reliably in any system. By controlling inlet pressure fluctuations, maintaining proper downstream pressure ratios, selecting valves tailored to the temperature and medium type, and installing them in a convenient orientation, operators can achieve consistent performance and long-term durability. These guidelines serve as a comprehensive framework for engineers and technicians tasked with designing and maintaining pressure control systems.