Mass Flowmeter Accuracy: A Deep Dive into Industrial Measurement
Mass flowmeters are crucial in industrial fluid measurement. They directly measure mass flow in fields like chemical engineering, energy, pharmaceuticals, and aerospace. Their accuracy class is a key performance indicator. It ensures reliable measurements and impacts production stability and economy. This article systematically analyzes mass flowmeter accuracy. We’ll cover classification, influencing factors, enhancement measures, and practical applications.
I. Scientific Classification of Accuracy Classes
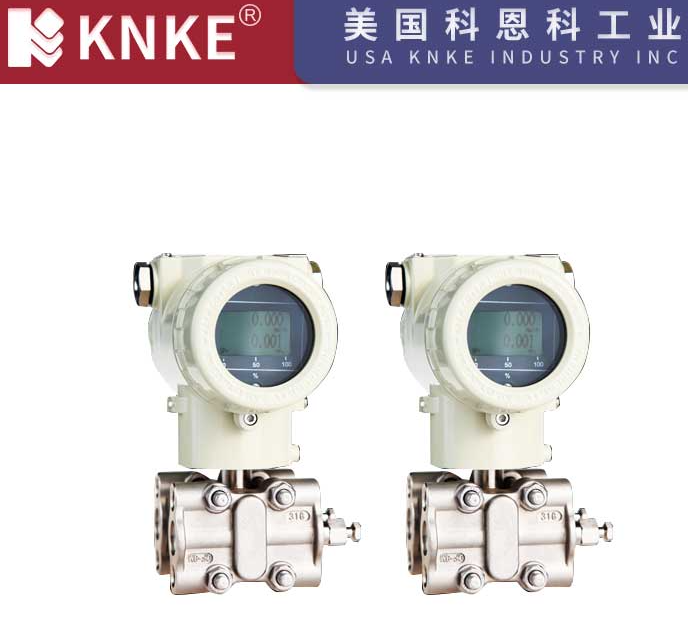
Mass flowmeters typically have three core accuracy levels. These levels, based on measurement error ranges, suit different industrial applications.
1. Basic Accuracy Class (±1%~±2%)
- Error Range: Measurement results deviate from true values by ±1% to ±2%.
- Technical Features: Basic sensor design meets conventional measurement needs. It offers high cost-effectiveness.
- Application Scenarios: This class suits industrial scenarios with moderate accuracy. Examples include water supply and drainage, sewage treatment, cooling water monitoring in steel manufacturing, and general chemical process material metering.
- Typical Advantages: It is low cost, easy to maintain, and suitable for large-scale deployment.
2. Advanced Accuracy Class (±0.5%~±1%)
- Error Range: Measurement error stays within ±0.5% to ±1%. This improves accuracy by over 50% compared to the basic class.
- Technical Features: Improved sensors are used, such as high-precision electromagnetic induction elements or optimized Coriolis vibration structures. They also include basic temperature/pressure compensation functions.
- Application Scenarios: This class applies to scientific research, precision metrology, food and pharmaceutical production (e.g., liquid medicine ratio), and intermediate process control in energy and chemical industries (e.g., feedstock monitoring in reactors).
- Typical Advantages: It maintains stable measurement under complex conditions. It also meets the needs of medium-precision industrial automation control.
3. Precision Accuracy Class (±0.2%~±0.5%)
- Error Range: Measurement error is as low as ±0.2% to ±0.5%. This represents the industry’s top precision level.
- Technical Features: Patented sensor technologies are employed, like Anton Paar’s Coriolis sensor or Alicat’s high-precision thermal probe. Intelligent algorithms integrate for real-time compensation of fluid property changes. High-stability power modules and anti-interference designs are also included.
- Application Scenarios: This class is for extremely high-precision fields. These include aerospace fueling (e.g., precise rocket propellant metering), semiconductor wafer manufacturing (ultrapure water/special gas flow control), high-end pharmaceuticals (sterile preparation raw material ratio), and precision scientific research (fluid dynamics experiments).
- Typical Advantages: It supports micro-flow measurement (e.g., SLM-level gas flow) and offers strong anti-interference capabilities. Long-term accuracy decay rate is less than 0.1% per year.
II. Core Influencing Factors of Accuracy Performance
Actual mass flowmeter accuracy depends on the design class and multiple working conditions. Key control is necessary during selection, installation, and maintenance.
1. Manufacturing Process and Component Precision
- Sensor Machining Accuracy: The wall thickness uniformity of Coriolis flowmeter vibration tubes and the consistency of thermal flowmeter temperature probes directly affect signal acquisition accuracy.
- Integrated Assembly Process: Stability of signal transmission between the sensor and transmitter is vital. Fluid disturbance control of sealing components also matters; pipeline inner wall roughness should be ≤Ra0.8μm.
2. Installation Specifications and Pipeline Conditions
- Straight Pipe Section Length: Upstream requires 10-20 times the pipe diameter. Downstream needs 5-10 times the pipe diameter of straight pipe sections. This avoids flow field distortion from elbows and valves (e.g., error increases by 0.3% when flow velocity non-uniformity exceeds 5%).
- Installation Attitude: Coriolis flowmeters require horizontal installation. An inclination angle over 5° introduces additional vibration interference. Thermal flowmeters must ensure the sensor is fully immersed in the flow channel center.
3. Fluid Characteristics and Medium State
- Changes in Physical Parameters: Fluctuations in density, viscosity, and thermal conductivity (e.g., when gas density changes by $>$10%, thermal flowmeter error increases by 0.5%) need correction. This can be done through real-time compensation algorithms or regular calibration.
- Medium Cleanliness: Solid particles ($>$50μm) or liquid bubbles will block thermal probes or wear Coriolis vibration tubes. A filter with a precision ≥40μm is required at the front end.
4. Maintenance, Calibration, and Environmental Adaptation
- Regular Calibration Cycle: Calibrate industrial-grade flowmeters annually. Precision-grade equipment needs calibration every six months. Use a standard flow source (uncertainty ≤0.1%) for multi-point linear calibration.
- Environmental Stability: Power fluctuations >±5%, temperature changes $>$10℃/h, or strong electromagnetic interference (e.g., near frequency converters) cause signal drift. A voltage-stabilized power supply and electromagnetic shielding devices are necessary.
III. Technical Paths and Engineering Practices for Accuracy Optimization
1. Innovation in Sensor Technology
- Coriolis Type: A double parallel vibration tube design (e.g., Emerson Micro Motion LF series) improves vibration frequency measurement resolution. Patented optical sensors enhance accuracy to ±0.2%.
- Thermal Gas Type: Multi-channel temperature measurement probes (e.g., ABB Sensyflow) integrate. Neural network algorithms dynamically compensate for gas component changes. This achieves direct mass flow measurement without temperature/pressure compensation.
- Electromagnetic Type: Superconducting coil technology reduces zero drift. Optimized lining materials (e.g., PTFE) improve liquid measurement accuracy to ±0.3%.
2. Full-Process Quality Control
- Manufacturing Link: Coordinate measuring machines (accuracy ±0.001mm) detect key components. Helium mass spectrometry leak detection (leakage rate $<$1×10⁻⁹mbar·L/s) ensures tightness.
- Testing Link: More than 10-point calibration is performed within the full range (covering 0.5%~100% of the range). Extreme working conditions (e.g., ±50℃ temperature shock, 10g vibration) are simulated to test accuracy stability.
3. Intelligent Operation and Predictive Maintenance
- Integrates IoT Modules: Real-time monitoring covers parameters such as sensor temperature, vibration amplitude, and signal noise. Machine learning algorithms predict accuracy decay trends (e.g., triggering a calibration warning when error growth rate exceeds 0.1%/month).
- Remote Calibration System: This system supports issuing calibration commands via cloud platforms. It automatically completes zero and span calibration using built-in standards, reducing manual intervention errors.
IV. Golden Rules for Selection and Application
- Match Classes as Needed: Basic accuracy (±1%) suffices for general industrial scenarios. Advanced accuracy (±0.5%) is recommended for material cost accounting or process optimization (e.g., pharmaceuticals, semiconductors). Precision accuracy (±0.2%) is mandatory for critical safety or R&D fields (e.g., aerospace, nuclear industry).
- Focus on Comprehensive Error: Understand the difference between “reading error” (%Rd) and “full-scale error” (%F.S.). For small flow measurements ($<$10% of the range), prioritize models with %F.S. error (e.g., North China CS330 has an error as low as ±0.35%F.S. at ≤35% of the range).
- Full Lifecycle Management: Establish equipment files. Record calibration data, failure history, and working condition parameters. Optimize maintenance strategies through big data analysis (e.g., shortening filter replacement cycles to 3 months in high-dust environments).
Conclusion
Mass flowmeter accuracy balances technical performance and application requirements. It ranges from industrial universality in the basic class to cutting-edge breakthroughs in the precision class. Its value lies in accurate measurement data and reliable flow control solutions for high-end manufacturing and green energy.
Sensor technology, intelligent algorithms, and industrial internet are deeply integrating. Mass flowmeter accuracy will move towards a higher dimension. It will evolve from static calibration accuracy to dynamic process accuracy. It will also upgrade from single-device accuracy to full-system accuracy optimization, powering precise measurement and control in the Industry 4.0 era.