Main Functions of Steam Traps
In a steam system, a steam trap plays a crucial role, acting as the system’s “cleaner.” Its primary responsibility is to discharge condensate, air, and non-condensable gases while preventing steam leakage. Understanding these core functions of a steam trap is vital for ensuring the efficient and safe operation of any steam system.
Discharging Condensate: Ensuring Efficient Heat Transfer
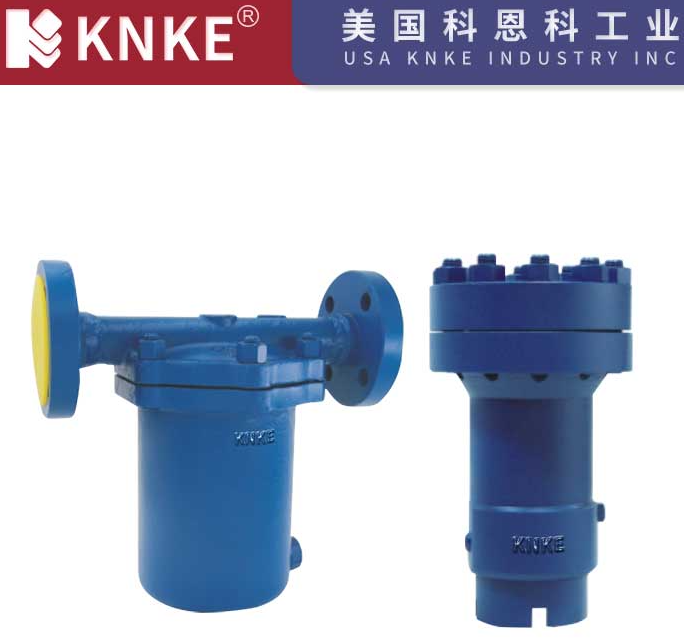
As steam travels through pipes or transfers heat to equipment, it gradually cools down and condenses back into water. If this condensate isn’t removed promptly, it accumulates inside pipes and equipment, forming a “film” of water. This water film can severely hinder heat transfer from the steam to the medium being heated, significantly reducing heat transfer efficiency. Imagine trying to heat a room with a radiator full of cold water instead of hot steam – it wouldn’t be very effective, would it? Similarly, the presence of condensate prolongs heating times and can even prevent you from achieving the desired heating results, leading to enormous energy waste. The core function of a steam trap is to identify and promptly discharge this condensate, ensuring that the steam can fully contact the heating surfaces and maintain efficient heat transfer performance.
Discharging Air and Non-Condensable Gases: Eliminating System Obstructions
Besides condensate, steam systems also contain air and other non-condensable gases (like carbon dioxide and nitrogen). These gases are lighter than steam and tend to accumulate in the upper parts of pipes and equipment, forming “pockets.” Air and non-condensable gases pose several significant dangers:
- Reduced Heat Transfer Efficiency: Air and non-condensable gases are poor conductors of heat. The “pockets” they form act like insulation layers, preventing the steam’s heat from transferring and further diminishing the system’s heat transfer efficiency.
- Corrosion: Oxygen and carbon dioxide dissolved in condensate are primary causes of internal corrosion in steam systems, accelerating the deterioration of pipes and equipment.
- False System Pressure: Air and non-condensable gases occupy space that steam should fill, which can lead to false pressure readings on gauges, affecting system control.
Through its design, a steam trap effectively identifies and expels these air and non-condensable gases, creating an unobstructed flow path for pure steam. This ultimately improves system efficiency and extends equipment lifespan.
Preventing Steam Leakage: Saving Energy and Ensuring Safety
Another critical function of a steam trap is to prevent steam leakage. After discharging condensate and gases, the steam trap must close immediately to prevent valuable steam from escaping. If a steam trap malfunctions or is incorrectly sized, leading to steam discharging along with the condensate, it results in immense energy waste. Continuous steam leakage not only significantly increases operating costs but also has an environmental impact. More importantly, steam leaks can pose safety hazards, such as high-temperature burns and noise pollution. A properly functioning steam trap accurately differentiates between steam and condensate, ensuring that only condensate and gases are discharged, keeping valuable steam within the system to continue its work.
Summary
In summary, a steam trap is not just a simple “drain valve”; it is an indispensable and precise component within a steam system. Its main functions—efficiently discharging condensate, thoroughly removing air and non-condensable gases, and strictly preventing steam leakage—collectively ensure that the steam system operates at its best: with high heat transfer efficiency, low energy consumption, extended equipment life, and safe operation. Neglecting the role of steam traps, or improper maintenance, can lead to significant efficiency losses and safety risks.