How Diaphragm Pumps Safeguard Food Safety in Food Testing Equipment
Food safety has become a top priority in modern food production. Manufacturers must inspect every step of the process—from raw materials to finished products—to meet hygiene and quality standards. Food testing equipment plays a vital role in achieving this goal. Among its key components, diaphragm pumps directly support accurate testing, helping the industry protect consumer health.
Delivering Accurate and Reliable Food Analysis
Food testing equipment analyzes components in food and determines their proportions. It detects contaminants, verifies nutritional values, and confirms overall quality. Diaphragm pumps enable these processes by delivering fluids with precision and maintaining stable pressure. Their consistent performance ensures accurate, repeatable results. As a result, food manufacturers rely on these pumps to uphold safety and quality standards.
Protecting Safety in Dairy Production
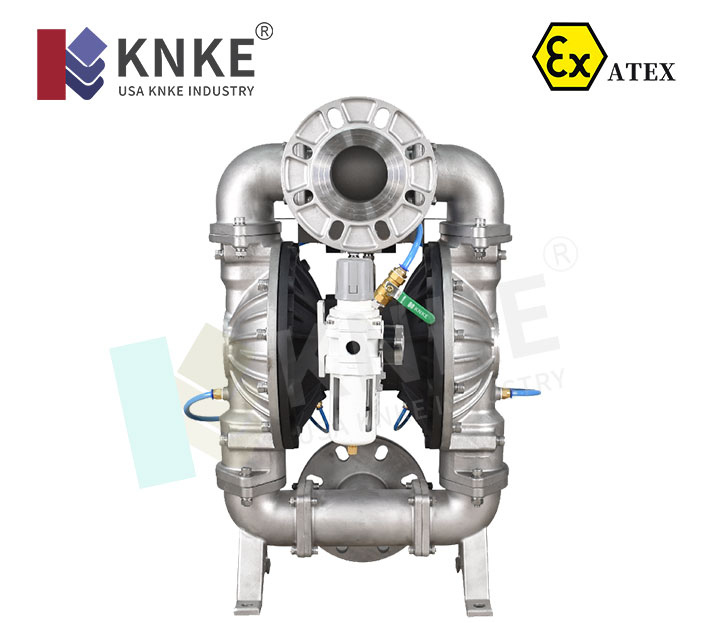
In the dairy industry, precise testing determines the fat, protein, moisture, and bacterial content of milk and related products. Diaphragm pumps operate inside milk analyzers to create the necessary vacuum for waste removal and sample handling. In compact analyzers, the pumps transfer milk and reagents through sensors to measure composition with accuracy. Although swing piston pumps can handle certain pressure needs, diaphragm pumps offer cleaner and more stable operation, making them a preferred choice.
Maintaining Consistency in Wine Quality
Wine producers need accurate control over chemical components—especially sulfur—to preserve flavor and prevent spoilage. Diaphragm pumps help wine analyzers measure sulfur levels and manage reagent flow with precision. For example, low sulfur may cause wine to spoil quickly, while excessive levels can affect taste and cause headaches. Therefore, wine testing systems rely on diaphragm pumps to handle both gas and liquid reagents efficiently, ensuring consistent quality.
Key Advantages of Diaphragm Pump Technology
Diaphragm pumps offer many advantages that make them ideal for food testing equipment:
- Oil-free operation avoids sample contamination.
- High chemical resistance ensures compatibility with a wide range of testing agents.
- Self-priming capability allows the pump to start dry without external liquid.
- Dual-media capability enables the handling of both gases and liquids.
- Simple design allows easy maintenance and fast cleaning.
- Stable performance under both vacuum and pressure conditions.
In addition, their compact structure and low maintenance needs make them easy to integrate into different instruments.
Customized Designs for Specific Testing Needs
To meet diverse requirements in food testing, KNKE diaphragm pumps offer extensive customization options. Customers can choose from various motor types, including brushless DC motors and IP54-rated motors, for enhanced protection and control. Engineers can rotate pump heads to save space or customize fluid and electrical connections to simplify integration. Moreover, users can request specific materials to ensure chemical compatibility. Before delivery, KNKE tests every pump rigorously to guarantee consistent performance. Upon request, they also provide custom testing based on customer specifications.
Food safety demands reliable and accurate testing. Diaphragm pumps support this mission by providing clean, precise, and consistent fluid handling in food testing equipment. From dairy analysis to wine composition monitoring, these pumps ensure manufacturers meet strict safety standards. As testing technology continues to evolve, diaphragm pumps remain essential in helping producers deliver high-quality, safe food to consumers around the world.
Great insight on how diaphragm pumps contribute to food safety. ItDiaphragm Pumps in Food Testing would be interesting to learn more about how they handle highly viscous or particulate-laden samples in testing scenarios.