How Check Valves Work
Check valves, also known as non-return valves, are critical components in fluid systems that ensure unidirectional flow by preventing backflow. The operation of a check valve is based on pressure differential and the valve’s internal design, ensuring that fluid only flows in one direction. Check valves are widely used in steam, condensate, and other fluid systems to maintain system safety and efficiency.
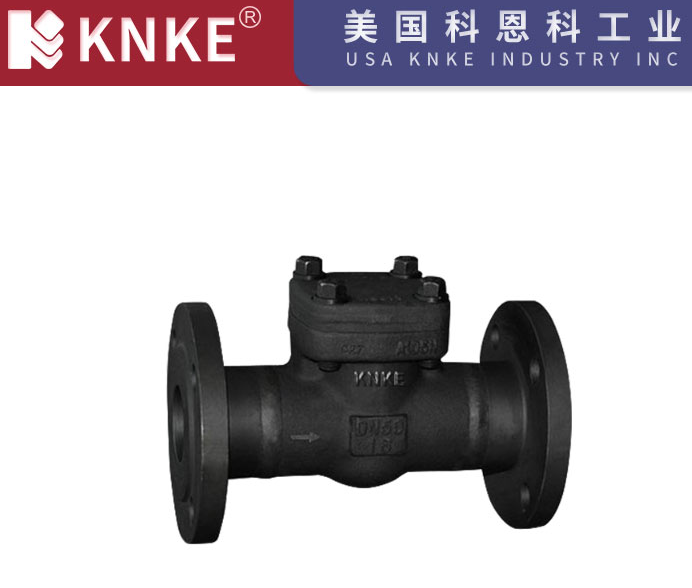
1. Basic Principle of Check Valves
The operation of a check valve relies on the pressure differential between the upstream and downstream sides of the valve. When the upstream pressure is higher than the downstream pressure, the valve opens. The opening of the valve is typically assisted by a spring or weight mechanism that generates an opening force (pressure differential × valve cross-sectional area). When the opening force exceeds the closing force, the valve disc or element opens, allowing fluid to flow through the valve. At this point, a volume flow begins.
The closing process occurs when the flow of fluid decreases. As the upstream pressure of the valve drops, the closing force once again exceeds the opening force, causing the valve to close and preventing backflow. This process repeats as the pressure in the system changes, until the volume flow is large enough that the additional dynamic pressure keeps the closing force from being sufficient to close the valve.
2. Opening and Closing of Check Valves
The opening and closing of check valves depend not only on the static pressure differential but also on the internal spring or weight mechanism. The purpose of the spring or weight is to provide the necessary opening and closing forces to balance the pressure differential in the system. Once the valve reaches a certain opening pressure, the valve disc begins to open, allowing fluid to flow.
However, when the flow decreases, the upstream pressure drops, causing the closing force to exceed the opening force, and the valve closes. During this process, if the valve design is unsuitable, noise issues may arise. For example, when the valve is partially open, and flow is reduced, a “clicking” sound may occur due to the impact between the valve disc and the valve seat. High-frequency buzzing sounds may also be heard in some cases.
3. Noise Issues with Check Valves
In certain cases, check valves may generate noise, especially when the flow rate is low. These noises are usually caused by the impact of the valve disc or element against the valve seat. If the valve is oversized, continuous noise may occur, indicating that the valve is not the best choice for the plant’s requirements. In such cases, using an appropriately sized valve is crucial to reduce noise and improve system performance.
If the pressure drop at full load is too large, it may not be advisable to use a valve with a smaller nominal size. Therefore, selecting a valve with the correct size for the system’s needs is essential to ensure optimal performance.
4. Applications of Check Valves
Check valves play a vital role in many industrial systems, particularly in steam and condensate systems, where they prevent backflow and ensure the stability of the fluid system. In vertical pipelines with upward flow, some check valves may even be used without springs to simplify the system and enhance efficiency.
In practice, the design of a check valve should be tailored to the specific needs of the system. The valve’s size, spring tension, and weight must be adjusted according to the pressure differential and flow conditions of the system to ensure reliable operation.
5. Conclusion
The operation of a check valve is based on balancing the opening and closing forces to automatically control the valve’s opening and closing, maintaining unidirectional fluid flow. The performance of the check valve directly impacts the stability and efficiency of the entire system. When selecting and using check valves, it is important to consider the pressure differential, flow rate, noise issues, and valve size to ensure that the valve meets the specific requirements of the plant and system.