Handling Faults in Differential Pressure Flow Meters
Differential pressure flow meters are widely used in industrial automation systems for their high accuracy and reliability. However, they can experience faults during operation. Identifying and resolving these issues quickly is critical to maintaining performance. This article covers common faults in differential pressure flow meters and how to handle them.
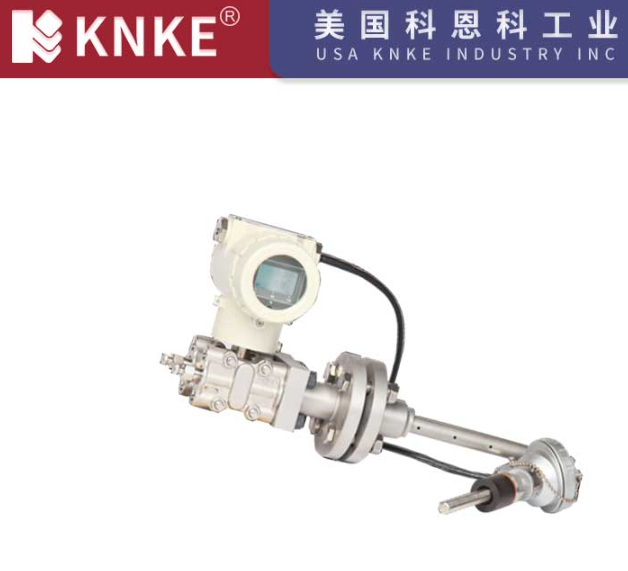
1. Blockage of the Pressure Tap Tube
Cause of the Fault: Blockage in the pressure tap tube is a common issue. It often happens when the tube is not purged regularly or when particles clog the line.
How to Handle It:
- First, close the primary valve. Use a wire or rod to clear the blockage.
- If this doesn’t work, open the primary valve and use steam pressure to flush the line.
- If flushing fails, use cutting and welding tools to replace the obstructed section of the tube.
Preventive Measures: Regularly clean and purge the pressure tap tube to prevent blockages. Conduct routine inspections to ensure the line remains clear.
2. Freezing of the Pressure Tap Line
Cause of the Fault: Freezing typically occurs in extremely cold weather or when the insulation is inadequate. It distorts the flow signal and affects measurement accuracy.
How to Handle It:
- Activate the heat trace system and ensure the heating cables are functioning.
- Check the insulation thickness and repair or add layers if needed.
Preventive Measures: Before cold weather sets in, check insulation systems. Repair any damaged insulation promptly to prevent freezing during operation.
3. Leakage at Valve Connections
Cause of the Fault: Leaks often occur at the joint between the primary valve and the piping. These leaks can cause pressure instability and impact measurement accuracy.
How to Handle It:
- If the leak occurs before the primary valve, contact a professional leak sealing company.
- If the leak occurs after the valve, close the valve and reseal the joint by welding or other methods.
- In special cases, replace the leaking section of the pipe after the valve.
Preventive Measures: During installation and maintenance, ensure proper sealing of valve connections. Regularly check for leaks at the joints to prevent issues.
4. Differential Pressure Transmitter Failure
Cause of the Fault: Differential pressure transmitters often fail due to zero drift, diaphragm deformation, or damaged electronic components.
How to Handle It:
- Zero Drift: Open the balance valve and close both the positive and negative pressure secondary valves. If the transmitter’s output is not 4mA, adjust the zero point.
- Diaphragm Damage: Diaphragm issues can be identified through laboratory calibration and testing.
- Electronic Component Failure: Check system displays and measurement readings for abnormal behavior. If issues are detected, inspect the electronics.
Preventive Measures: Perform regular calibration and maintenance to detect and prevent issues with transmitters. Ensure proper functioning of all electronic components.
Addressing faults in differential pressure flow meters promptly and effectively ensures the longevity and accuracy of the measurement system. Regular maintenance, timely troubleshooting, and proper preventive measures are key to minimizing downtime and maintaining optimal performance.