Guidelines for Selecting Valve Electric Actuators
Electric valve actuators play a pivotal role in industrial automation systems by enabling precise control over valve operation and regulating process conditions. Proper actuator selection is essential for ensuring system reliability, dynamic responsiveness, and long-term performance.
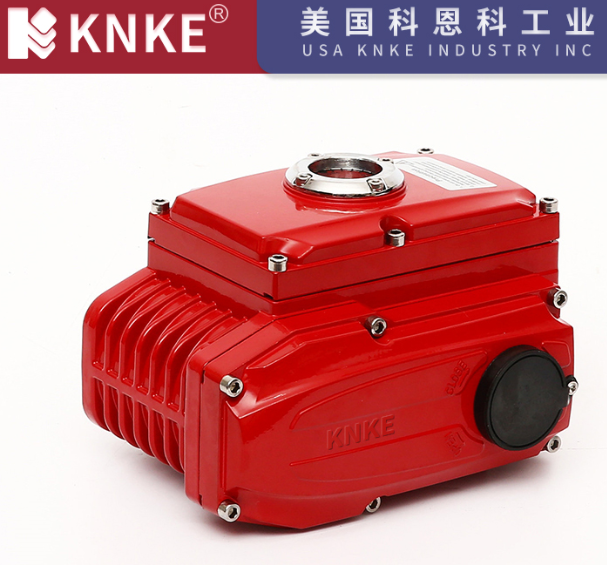
1. Operating Torque
Torque is the primary parameter when selecting an actuator. The actuator should provide at least 1.2 to 1.5 times the maximum required valve torque to account for factors like static friction, media viscosity variations, and seal adhesion.
2. Thrust Mechanism Structure
Actuators are typically divided into:
- Non-thrust disc design: Delivers torque directly, suitable for quarter-turn valves.
- With thrust disc: Converts torque into linear thrust, ideal for linear valves in high-pressure or large-diameter scenarios.
3. Number of Shaft Turns
The required shaft turns must match the valve’s stroke. This depends on valve height, thread pitch, and lead. Engineering evaluation should align with actual dimensions to ensure full stroke movement.
4. Stem Compatibility
For rising stem valves, the actuator’s shaft bore and keyway must accommodate the valve stem diameter precisely. For non-rising stems, check the dimensional compatibility to maintain efficient torque transfer.
5. Output Speed and Water Hammer
Opening or closing the valve too quickly can cause water hammer. It is vital to select actuators with soft start or speed reduction features to maintain hydraulic balance.
6. Overload Protection
To avoid damage from overload, actuators should include:
- Adjustable torque limiters;
- Thermal relays for locked-rotor protection;
- Thermostats for heat monitoring;
- Fuses or overcurrent relays for short-circuit protection.
Redundant protection strategies should include both current monitoring and thermal modeling to enable predictive control and safe shutdowns.
FAQ
Q1: Are electric actuators compatible with all valve types? A1: Not all. Selection depends on the valve type, such as gate, ball, or butterfly valves, and their movement requirements.
Q2: Is overload protection mandatory? A2: Yes. It is crucial for safeguarding both the actuator and the controlled system, particularly under high-frequency or variable load conditions.
Q3: How do actuators affect water hammer? A3: Rapid actuation may trigger water hammer. Choosing actuators with controlled speeds reduces this risk.
Q4: What are the most critical parameters when selecting an actuator? A4: Operating torque, shaft turns, stem compatibility, actuation speed, and protective features.
Q5: Can actuators operate in extreme temperatures? A5: Yes, provided they are designed with suitable thermal ratings and environmental protections.
Effective electric actuator selection requires a rigorous evaluation of load dynamics, mechanical compatibility, and operational scenarios. By considering torque reserves, motion speed control, interface matching, and multi-layered overload protection, system integrators can enhance reliability and support the precision demands of advanced automation environments.