Explosion‑Proof Turbine Flow Meter Performance Features and Application Advantages
First, the explosion‑proof turbine flow meter is engineered for hazardous and complex operating conditions. Consequently, it finds extensive use in petrochemical plants, urban gas networks, metallurgy, and power generation. Moreover, it consistently delivers the precise flow data these industries require.
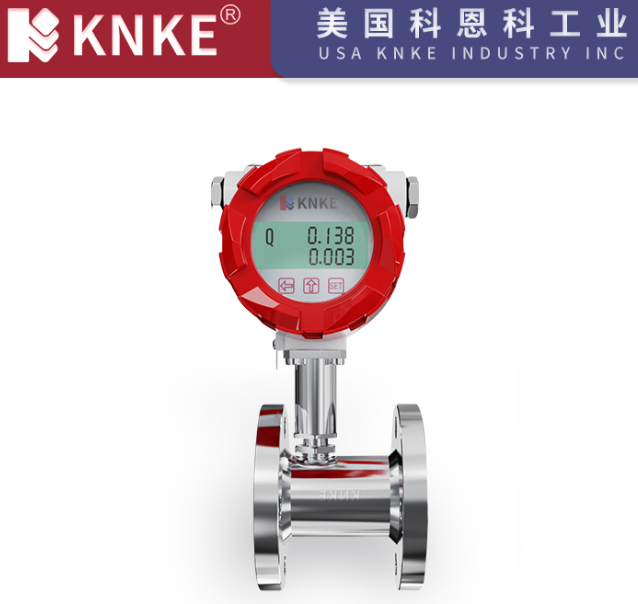
Key Performance Features
High‑Precision Measurement
- ±0.5%FS standard accuracy: By optimizing the rotor design and signal processing, we ensure high accuracy for most chemical and energy applications.
- Up to ±0.2%FS settlement‑grade accuracy: Therefore, this variant is ideal for trade settlements where data sensitivity is critical.
Broad Media Compatibility
- In addition to water and oils, the meter reliably measures natural gas, hydrogen, and steam.
- Furthermore, sensor materials and flow paths undergo special treatment to cover over 90% of industrial scenarios.
Simplified Structure & Low Maintenance
- We employ a modular design, separating the rotor assembly from the detection unit; this approach reduces mechanical wear and shortens service intervals.
- Also, tungsten‑carbide bearings extend service life by more than 30%, and core components can be replaced without pipeline shutdown.
Robust Explosion‑Proof Safety
- The unit features a flameproof housing and intrinsically safe circuitry, meeting ExdⅡCT6 certification.
- Meanwhile, an IP68 rating enables stable operation at depths up to 30 m underwater—ideal for mines and subsea pipelines.
Wide Environmental Adaptability
- The meter maintains stable performance from –40 °C to +200 °C, thus accommodating extreme temperature variations.
- In addition, it withstands pressures up to 25 MPa, making it suitable for LNG storage and high‑temperature steam delivery.
FAQ
Q1: What are the key installation considerations?
A1: First, align the meter’s axis with the pipeline centerline. Next, ensure at least ten pipe diameters of straight run upstream and downstream. Finally, avoid significant horizontal or vertical misalignment.
Q2: How should routine maintenance and calibration be performed?
A2: Regularly clean the rotor flow path and replace seals. Moreover, perform calibration using a standard flow rig every six to twelve months.
Q3: Which media can this flow meter handle?
A3: Beyond clean water and conventional oils, it also measures natural gas, LPG, and steam. Therefore, select the appropriate material version based on the fluid’s properties.
Q4: What recommendations exist for high‑temperature, high‑pressure applications?
A4: For temperatures above +150 °C, install cooling or insulation sections. In addition, use high‑temperature seals and high‑pressure fittings to ensure long‑term reliability.
Q5: How do I choose the correct explosion‑proof certification and IP rating?
A5: Determine the hazardous area classification (e.g., Zone 1/2) and select ExdⅡCT6 or iaⅡCT4 accordingly. Meanwhile, choose IP65, IP67, or IP68 based on moisture and submersion requirements.
It’s interesting to see how explosion-proof turbine flow meters are evolving to meet the needs of high-risk industries. The ±0.5% accuracy is particularly impressive considering the often harsh and variable environments these devices operate in.