Electromagnetic Flowmeter Pipe Connection Methods
In industrial production, liquid medium flow measurement is crucial. Electromagnetic flowmeters are common measuring instruments, and their connection methods directly impact measurement accuracy and ease of installation and maintenance. The choice of connection method for an electromagnetic flowmeter depends on pipe diameter, pressure, medium characteristics, and installation requirements under various operating conditions. This necessitates diverse connection solutions. Here’s a technical analysis and explanation of common connection methods and their application scenarios.
I. Flange Connection
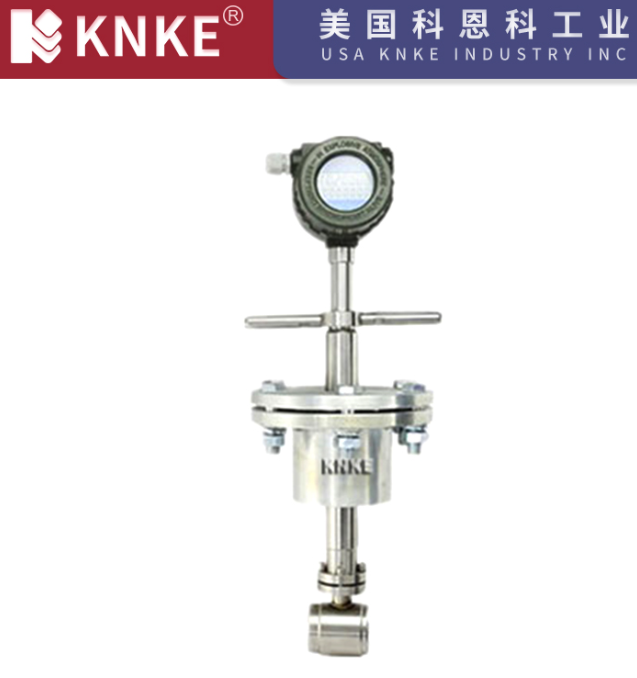
Technical Features and Scope of Application Flange connection is the most widely used method for electromagnetic flowmeters, suitable for pipelines with diameters greater than DN25. This method secures the flowmeter’s flanges to the pipeline flanges with bolts, forming a sealed structure. During installation, always ensure the flange specifications (e.g., nominal diameter, pressure rating) match. Typically, you need four flanges to ensure even stress distribution.
Advantages and Scenarios Flange connections are highly versatile. They adapt well to high-pressure, large-diameter conditions in chemical, petroleum, and water supply/drainage industries. Furthermore, they offer reliable sealing performance and withstand strong vibrations and pressure shocks. However, uniformly tighten bolts to prevent flange misalignment and leakage.
II. Threaded Connection
Technical Features and Scope of Application Threaded connections suit small to medium flow scenarios where pipe diameters are less than DN50. This method allows for quick installation by screwing the flowmeter directly into the pipe, eliminating the need for additional flange components. We commonly find this in medical, food, and pharmaceutical industries, where fluid flow is low, pipelines are compact, and hygiene standards are high.
Advantages and Precautions This method offers convenient installation and flexible disassembly, saving space. However, match thread standards (e.g., NPT or G threads) and use sealing materials (such as PTFE tape) to prevent leakage. Because its pressure capacity is limited (usually ≤1.6 MPa), it is not suitable for high-pressure environments.
III. Wafer Connection
Technical Features and Scope of Application Wafer connections involve clamping the flowmeter between two pipeline flanges using bolts. This method doesn’t require the flowmeter body to have integrated flanges, saving material and space. It suits medium-diameter pipelines from DN50 to DN300.
Advantages and Application Scenarios This method features a compact structure and light weight. During installation, you don’t need to disassemble the pipeline; simply insert and secure the flowmeter. We often use it in heating networks and gas measurement applications where installation efficiency is critical. Nevertheless, ensure the parallelism of the pipeline flanges to prevent uneven clamping force from deforming the instrument.
IV. Sanitary Clamp Connection
Technical Features and Scope of Application Clamp connections (quick-release connections) use a clamp-type sealing structure to quickly secure the flowmeter to the pipeline with a stainless steel clamp. They are ideal for small-diameter, low-pressure (≤1.0 MPa) clean medium applications, such as in the food and beverage and biopharmaceutical industries.
Advantages and Technical Essentials Clamp connections meet hygienic standards, featuring smooth inner pipe walls and no dead corners, which facilitates frequent disassembly and cleaning. During installation, use specialized sanitary clamps and gaskets (e.g., EPDM material) to ensure sealing and corrosion resistance. This makes them the preferred choice for applications with extremely high cleanliness requirements.
V. Insertion-Type Installation
Technical Features and Scope of Application Insertion-type installation allows for work without interrupting fluid flow. It involves opening an installation hole in the pipeline and inserting the sensor probe into the pipeline’s center (usually at the radius), then sealing it with a ball valve or a flange spool piece. This method suits large-diameter pipelines (DN200 and above) where high control accuracy is not required, such as in wastewater treatment and cooling water circulation systems.
Advantages and Limitations This method avoids production downtime and has low installation costs. However, measurement accuracy is significantly affected by flow velocity distribution (accuracy typically ≤1.5%), making it unsuitable for high-precision metering. Crucially, ensure accurate probe insertion depth to minimize measurement deviation.
Core Selection Factors and Matching Recommendations for Operating Conditions
When choosing a connection method, consider these factors comprehensively:
- Pipe Diameter: For DN25 and below, opt for threaded connections. For DN25-DN300, prioritize flange or wafer connections. For DN200 and above, consider insertion-type.
- Medium Characteristics: For clean media, choose clamp connections. For corrosive media, select flange connections with corrosion-resistant materials (e.g., PTFE lining, stainless steel).
- Pressure Rating: For high-pressure conditions (>4.0 MPa), flange connections are mandatory. For low-pressure scenarios, you can choose clamp or threaded connections.
- Maintenance Requirements: For applications needing frequent disassembly and maintenance, choose clamp or insertion-type connections. For long-term stable operation, opt for flange or wafer connections.
- Accuracy Requirements: For high-precision metering (≤0.5%), use flange or wafer connections. For low-precision control, consider insertion-type.
Selecting the proper connection method is crucial for ensuring electromagnetic flowmeter accuracy and operational efficiency. For different operating conditions, always conduct a comprehensive evaluation considering both technical requirements and economic feasibility. This ensures the connection solution perfectly matches your on-site needs, providing reliable support for industrial fluid measurement.