Electric vs. Pneumatic Butterfly Valves: Key Differences & Selection Guide
In the realm of industrial pipeline control, butterfly valves are widely adopted due to their compact structure, low flow resistance, and excellent regulating performance. Among them, electric butterfly valves and pneumatic butterfly valves represent the two dominant types, distinguished by their actuation methods. While both serve to control fluid flow, they exhibit significant differences in technical principles, performance characteristics, and application scenarios. This article will professionally dissect the core distinctions between them, offering a clear reference for your engineering selection.
I. Actuation Principles and Core Construction: Differences in Power Source
The most fundamental difference between electric and pneumatic butterfly valves lies in how they are driven.
1. Electric Butterfly Valves: Power-Driven Smart Control Units
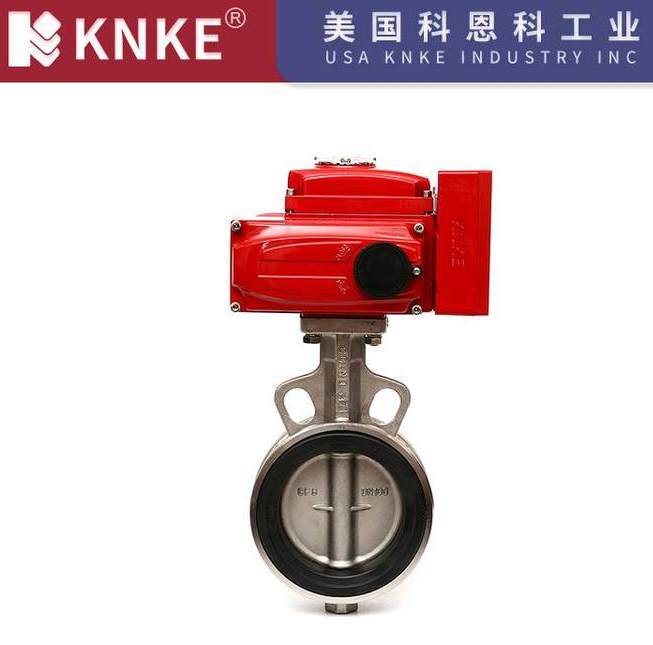
An electric butterfly valve consists of an electric actuator and the butterfly valve body. Its operation relies on a motor driving a gear reduction mechanism, converting electrical energy into the rotational torque for the valve disc. The actuator typically incorporates an internal control module, capable of receiving standard 4-20mA analog signals or PLC (Programmable Logic Controller) commands, thereby enabling precise opening/closing or proportional control of the valve.
Key Advantages:
- No reliance on air source: Suitable for locations with stable power supply.
- Supports remote automated control: Easily integrated into automation systems like DCS (Distributed Control Systems).
- Wide application range: Commonly used for flow regulation in large-diameter pipelines (DN50-DN3000).
Typical Configuration: Three-phase asynchronous motor or servo motor, worm gear reducer, position feedback sensor. They often boast an IP67 protection rating and can operate in temperatures ranging from -20℃ to +80℃ (high-temperature environments require special materials).
2. Pneumatic Butterfly Valves: Air Pressure-Driven Efficient Actuation Solutions
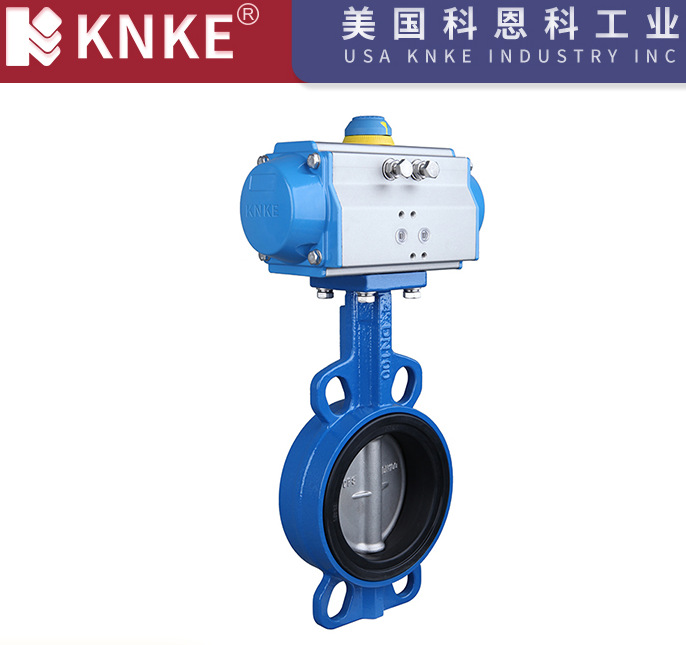
Pneumatic butterfly valves utilize compressed air as their power source. A pneumatic actuator (piston-type or diaphragm-type) drives the valve disc’s rotation. Pneumatic actuators are categorized into double-acting (driven by air in both directions) and single-acting (spring-return type, which automatically reverts to a normally open or closed position upon air supply failure).
Key Characteristics:
- Simple structure: Generally lighter and more compact compared to electric actuators.
- Fast response speed: Opening/closing times are typically less than 5 seconds, making them ideal for rapid shut-off or opening applications.
- Intrinsically safe (explosion-proof): Pneumatic systems do not generate electrical sparks, making them highly suitable for flammable and explosive environments, such as natural gas or combustible gas pipelines.
Typical Configuration: Aluminum alloy or stainless steel cylinder, spring-return mechanism (for single-acting types), solenoid valve, limit switch. They typically operate within a pressure range of 0.4-0.7MPa and require accompanying air treatment units (like filter regulators and lubricators) to ensure clean and stable air supply.
II. Performance Comparison and Work Condition Adaptability: Selection Considerations
In practical applications, electric and pneumatic butterfly valves each have distinct strengths in terms of performance and adaptability to different working conditions.
1. Environmental Adaptability
- Electric Butterfly Valves: Are more sensitive to humidity. In humid environments, actuators with higher moisture protection ratings are necessary. Additionally, the motor generates heat during operation, and frequent adjustments can trigger thermal protection, making them more suitable for normal temperature (<60℃) and dry environments.
- Pneumatic Butterfly Valves: Exhibit better resistance to moisture and dust. With proper air treatment, they can operate over a wider temperature range, from -40℃ to +150℃. Pneumatic actuators do not suffer from motor overheating issues, making them highly suitable for high-frequency cycling applications (e.g., more than 10 cycles per minute). However, their operational stability is heavily reliant on a stable air source (air pressure fluctuation should be less than ±10%).
2. Control Precision and Functionality
- Electric Butterfly Valves: Can achieve 0-100% precise opening adjustment. When paired with a smart control box, they can implement advanced functions such as PID control and fault diagnosis, offering a high degree of automation. This makes them ideal for industries like chemical processing, metallurgy, and wastewater treatment, where remote monitoring and precise control are crucial.
- Pneumatic Butterfly Valves: Standard configurations typically offer on/off control. To achieve proportional control, an additional positioner must be installed, at which point their control accuracy is approximately ±1.5%. Single-acting pneumatic butterfly valves incorporate a fail-safe function; for instance, in gas pipelines, the valve automatically closes upon air supply failure, meeting SIL2 safety certification requirements for high safety.
3. Installation and Maintenance
- Electric Butterfly Valves: Wiring is relatively complex, requiring connections for power, control signals, and grounding. Maintenance usually necessitates a professional electrician. The reduction gears require regular lubrication. Their Mean Time Between Failures (MTBF) is approximately 8,000 hours.
- Pneumatic Butterfly Valves: Feature standardized air connections (G1/4″~G3/8″), making installation more straightforward. The cylinder’s sealing rings are wear parts, but their lifespan typically reaches around 500,000 cycles, and replacement costs are low, allowing on-site personnel to perform maintenance quickly.
III. Typical Application Scenarios: Tailored Choices
Application Area | Electric Butterfly Valve Advantages | Pneumatic Butterfly Valve Advantages |
Industrial Pipeline Control | No air source available, requires precise flow regulation (e.g., petroleum cracking units) | Stable air source available, requires rapid shut-off (e.g., gas boiler inlet valves) |
Safety Requirements | General industrial conditions, remote control | Flammable/explosive media (e.g., LNG pipelines), fail-safe scenarios |
Environmental Conditions | Dry, normal temperature, stable power supply zones | Humid, dusty, high-temperature (requires high-temperature resistant sealing materials) |
Regulation Frequency | Low-frequency regulation (<5 times/hour) | High-frequency cycling (e.g., aeration valves in wastewater treatment plants, >10 times/minute) |
IV. Key Selection Factors and Cost Analysis
When selecting butterfly valves, the following key factors should be prioritized:
1. Core Selection Criteria
- Actuation Condition: First, assess whether a stable and reliable air source is available on-site. If an air source exists and explosion-proof requirements are in place, prioritize pneumatic butterfly valves; otherwise, electric butterfly valves are a more suitable choice.
- Sealing Requirements: Soft seals (e.g., EPDM/NBR materials) are suitable for media like water and air. Hard seals (metal-to-metal) are used for harsh conditions such as high-temperature steam (≤425℃). For both types, it’s crucial to consider the chemical properties and temperature of the medium to select compatible sealing materials.
2. Cost Analysis
While specific cost data isn’t provided here, pneumatic butterfly valves typically have a lower initial valve body cost compared to electric butterfly valves. However, you must also factor in the additional costs for air treatment units and air piping for pneumatic systems. Electric butterfly valves might have a higher upfront investment but could lead to lower long-term maintenance complexity due to the stability of the electrical power supply. For a comprehensive long-term cost of ownership assessment, consider equipment purchase price, installation costs, operational energy consumption, maintenance frequency, and spare parts costs.