Electric Valve Sealing Methods: A Comprehensive Guide
Electric valves are key components in fluid control. Their sealing performance directly impacts system efficiency, safety, and reliability. Good sealing prevents leaks, cuts energy loss, protects the environment, and extends valve life. This article explores common sealing methods for electric valves, avoiding brand or company specifics.
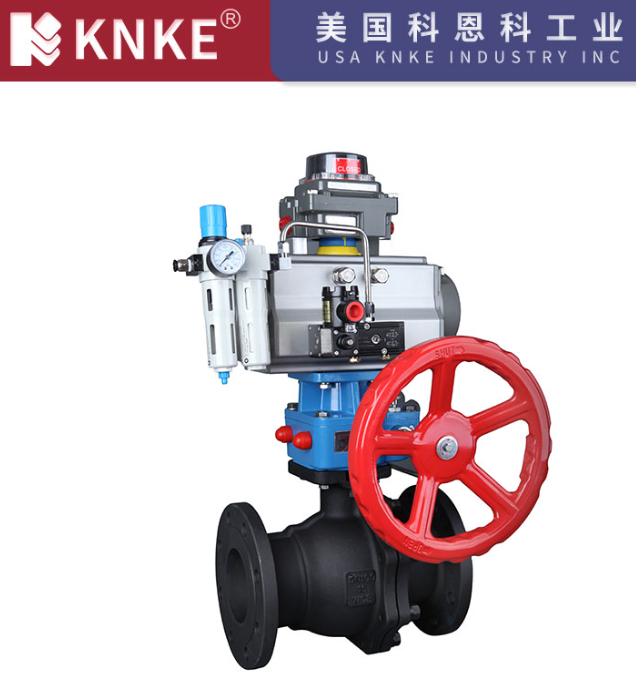
Valves achieve sealing by creating tight contact between the closure element and the seat. This stops fluid passage. Different applications and conditions call for various sealing approaches.
1. Soft Sealing
Soft sealing typically uses non-metallic materials. These materials are elastic and pliable. They fill tiny gaps between sealing surfaces better, leading to superior sealing.
- Elastomeric Material Sealing: Common elastic materials include various rubbers (like NBR, EPDM) and fluororubbers. PTFE (polytetrafluoroethylene) and its modified versions are also used. These materials deform under compression. They conform tightly to sealing surfaces, providing excellent sealing. Soft-seated valves suit high-sealing needs and lower media temperatures and pressures. Examples include water, gases, or weak corrosive media. Benefits include good sealing and easy zero leakage. Drawbacks are poorer resistance to high temperatures, high pressures, and abrasion. Service life can be limited by the material’s properties.
2. Hard Sealing
Hard sealing means direct metal-to-metal contact. It can also be metal-to-ceramic or other hard materials. This contact is between the valve’s closure element and its seat. This method relies on precise machining and surface treatment. These create a highly accurate fit between sealing surfaces.
- Metal-to-Metal Sealing: This method depends on high-precision grinding and fit. This occurs between the valve’s closure element (like a disc, ball, or gate) and its seat. To boost sealing and wear resistance, sealing surfaces are often hard-faced. Alloys like Stellite or tungsten carbide are used, or surfaces are treated with nitriding or carburizing. Hard-seated valves resist high temperatures, high pressures, wear, and corrosion well. This makes them good for harsh conditions. Examples include high-temperature steam, abrasive fluids, or high-pressure gases. Their sealing performance might be slightly less perfect than soft seals. They demand extremely high machining precision and can experience some wear during operation.
- Metal-to-Ceramic Sealing: This combines metal’s toughness with ceramic’s extreme hardness and wear resistance. This composite seal performs exceptionally when facing highly abrasive or corrosive media. Ceramic materials usually go on the sealing surfaces of the valve seat or closure element. They resist media erosion and abrasion.
3. Stem Sealing
Stem sealing commonly prevents media leakage from the valve stem and bonnet connection.
- Gland Packing Sealing: This method involves filling the stuffing box around the valve stem. Rings of soft material like graphite, PTFE, or aramid fibers are used. Tightening gland bolts compresses the packing. This creates a tight seal with the valve stem and the stuffing box’s inner wall. The packing type and structure directly influence sealing and lifespan. This method is simple and easy to maintain. However, it needs regular tightening or replacement of the packing to maintain its seal.
- Bellows Sealing: Bellows sealing is an advanced, zero-leakage method. It’s often used where leakage requirements are very strict. A flexible metal bellows connects the valve stem and the bonnet. This forms a completely enclosed chamber. It eliminates external leakage during stem movement. The bellows’ material and design determine its pressure, temperature, and fatigue resistance.
Choosing the right sealing method for an electric valve requires careful thought. Consider the media’s properties (temperature, pressure, corrosiveness, particle content) and the valve’s operating frequency. Also, think about the required leakage class and maintenance costs. As material science and processing technology advance, electric valve sealing performance and reliability will continue to improve.