Differences Between Vacuum Valves and Standard Valves
Vacuum valves and standard valves are essential components that control fluid flow, but they differ significantly in design, operation, and application. While both regulate flow, vacuum valves are specifically built for low-pressure environments. Their unique features help them operate effectively under vacuum conditions. Below, we explore the main differences between vacuum valves and standard valves.
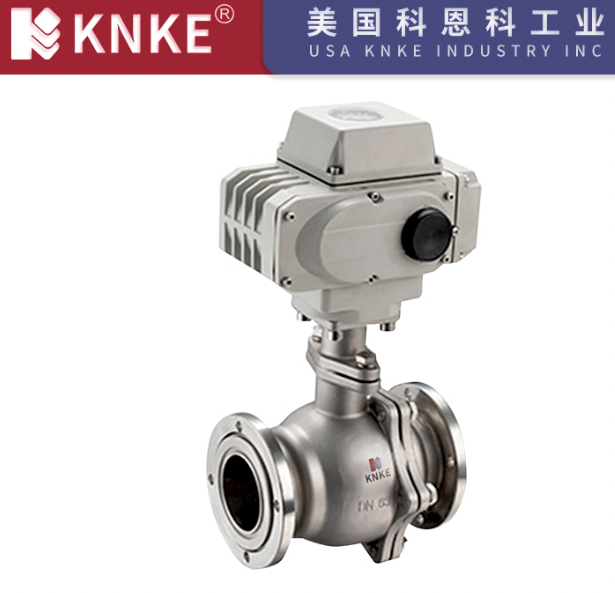
1. Pressure Environment Differences
Standard valves are commonly used in environments with normal or high pressure. They handle various types of fluids without any issue. In contrast, vacuum valves are designed to operate in environments with pressure lower than atmospheric pressure. These valves work in systems that function under a vacuum, where the pressure is much lower than normal. Therefore, vacuum valves must withstand negative pressure without leakage or failure.
2. Seat Pressure Drop Requirements
For vacuum valves, the pressure drop across the valve seat must not exceed 1 kgf/cm² (100 kPa). A significant pressure drop could destabilize the vacuum system and disrupt its operation. In comparison, standard valves do not have such strict requirements. These valves handle higher pressure systems, where minor pressure fluctuations are manageable.
3. Sealing Requirements
Vacuum valves must meet high sealing standards. Even the smallest leak can destabilize a vacuum system. For this reason, vacuum valves use high-quality seals, such as rubber or metal sealing rings, to maintain an airtight seal. Standard valves also need to be sealed properly but do not require the same stringent sealing materials. The materials for sealing in standard valves can vary from rubber to plastic, depending on the application.
4. Valve Type Selection
Vacuum valves are limited in terms of the valve types that can be used. Common types include bellows-sealed globe valves, ball valves, plug valves, and butterfly valves. These types provide reliable sealing in low- and medium-vacuum systems. However, gate valves are not suitable for vacuum systems because they lose their sealing ability in low-pressure conditions. Similarly, plug valves require oil lubrication, which can contaminate the vacuum system, so they are not typically used.
Standard valves, however, offer more flexibility. Gate valves, ball valves, butterfly valves, and plug valves can all be used in systems with normal or high pressure. These valves provide more options for a variety of applications.
5. Temperature Range and Material Selection
Vacuum valves have a narrower temperature range, typically between -70°C and +150°C. Extreme temperatures can damage sealing materials or the valve structure. Therefore, vacuum valves are made from materials like stainless steel, high-zinc brass (such as JI80), and plastics, which offer good temperature and corrosion resistance. In contrast, standard valves are designed for a broader temperature range. They can be made from a wider variety of materials to suit different operating conditions.
6. Valve Actuation and Stem Movement
Vacuum valves typically use a linear stem movement design, especially in bellows-sealed globe valves. This helps maintain an airtight seal in low-pressure environments. Standard valves, on the other hand, may use either linear or rotary stem movement, depending on the valve type (e.g., gate valve, ball valve, or butterfly valve). These valves are designed for high-pressure environments and have sealing mechanisms suitable for such conditions.
7. Lubrication Requirements
Vacuum valves do not use oil lubrication. Oil vapors can contaminate the vacuum system and disrupt its operation. In contrast, standard valves are often lubricated with oils or other lubricants to reduce friction and increase the lifespan of the valve. Since standard valves work in higher-pressure systems, the use of lubrication does not pose the same contamination risk as it does in vacuum systems.
Vacuum valves and standard valves differ in several key areas, including pressure, sealing requirements, and valve type selection. Vacuum valves are designed for low-pressure environments and focus on maintaining an airtight seal, minimal pressure drop, and temperature resistance. Standard valves, on the other hand, can handle a wider range of pressures and materials, offering greater flexibility for various applications. When choosing a valve for a specific system, it’s crucial to consider the operating conditions, pressure, temperature range, and sealing needs to ensure optimal performance.