Differences Between Centrifugal Pumps and Submersible Pumps
In the field of fluid transportation, centrifugal pumps and submersible pumps are two widely used types of pumping equipment. Although submersible pumps essentially belong to a special branch of centrifugal pumps, their structural design, application scenarios, and performance characteristics differ significantly from traditional centrifugal pumps. This article deeply analyzes the core differences between the two from dimensions such as technical principles, application scenarios, and maintenance costs, providing a scientific basis for user selection.
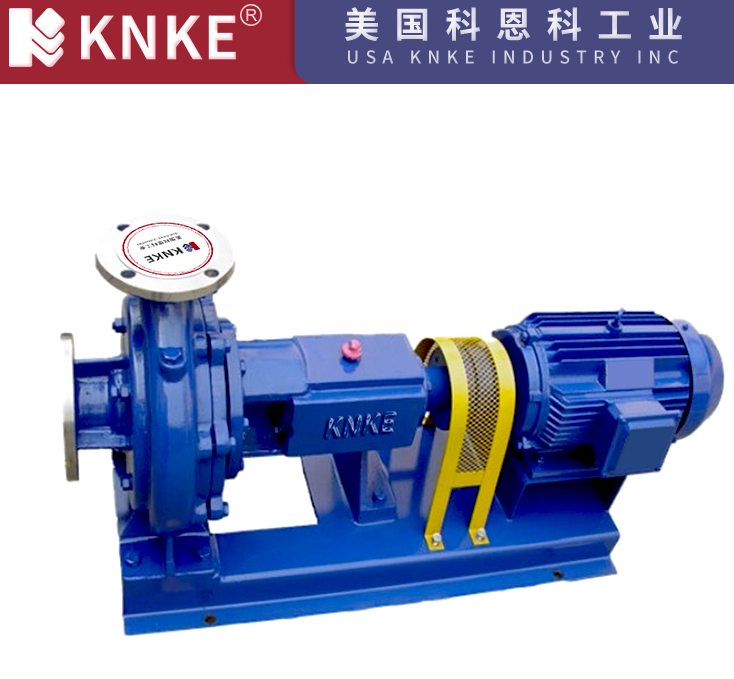
I. Essential Attributes: Subordinate Relationship and Core Positioning
(1) Centrifugal Pumps: Universal Pumps Driven by Centrifugal Force
Centrifugal pumps are a general term for pumps designed based on the principle of centrifugal force. Through high-speed rotation of the impeller, centrifugal force is generated to throw liquid from the center of the impeller to the edge, which is then collected by the volute and transported along the discharge pipe. Their core advantages lie in simple structure and stable flow, making them suitable for transporting various clean or low-impurity liquids in on-land scenarios. They serve as fundamental fluid equipment in industrial, agricultural, and municipal fields.
(2) Submersible Pumps: “Underwater Specialized Version” of Centrifugal Pumps
Submersible pumps represent a deep optimization of centrifugal pumps for underwater environments. They integrate the motor and pump body into a sealed unit that can operate completely submerged in liquid. Their core innovation lies in motor waterproof sealing technology (such as dual mechanical seals and sealed oil chambers), solving the problem that traditional centrifugal pumps cannot operate underwater, thus becoming essential equipment for special working conditions.
II. Core Difference Comparison: A Full-Dimensional Analysis from Structure to Application
(1) Structural Design: Adaptation to On-Land vs. Underwater Environments
Comparison Dimension | Centrifugal Pump | Submersible Pump |
---|---|---|
Motor Position | Independently installed on land, connected to the pump body via a drive shaft, requiring additional protective casing | Integrally sealed with the pump body, directly immersed in liquid; the motor casing serves both waterproof and heat-dissipating functions |
Cooling Method | Relies on air convection or additional cooling devices (e.g., fans, water-cooled jackets), with heat dissipation efficiency affected by ambient temperature | Uses surrounding liquid for direct motor cooling, ensuring uniform and efficient heat dissipation to avoid motor overheating loss |
Sealing System | Only needs to prevent liquid leakage to the outside, with lower sealing requirements (e.g., packing seals, mechanical seals) | Requires a dual-sealing barrier (inner mechanical seal + outer O-ring) to prevent liquid from penetrating the motor chamber, achieving IP68-level sealing |
Impeller Design | Conventional closed/semi-open impellers suitable for clean liquids | Mostly uses wear-resistant open impellers or vortex impellers capable of passing 5-20mm solid particles (e.g., impurities in sewage) |
(2) Installation and Operation: From “Priming Required” to “Plug-and-Play”
- On-Land Operation Logic of Centrifugal Pumps
- Requires fixed installation on a horizontal base, connected to the water source via a suction pipe (with anti-leakage requirements) and to the target location via a discharge pipe.
- Priming is mandatory before startup: The pump body and suction pipe must be filled with liquid to expel air; otherwise, dry running will cause impeller cavitation (suction lift typically ≤7 meters, restricted by atmospheric pressure).
- Typical scenarios: Factory circulating water systems (requiring long-term stable operation with clean cooling water), farmland irrigation (water distribution to large areas via pipeline networks).
- Underwater Operation Advantages of Submersible Pumps
- No complex installation needed; directly placed in liquid (e.g., deep wells, water tanks, rivers), only requiring connection of a power cable (with anti-electric leakage protection) and discharge pipe.
- Instant operation: Liquid directly fills the pump body without suction lift restrictions, operable at any depth below the liquid surface (theoretical maximum diving depth limited by sealing pressure resistance, usually 5-50 meters).
- Mobility revolution: Compact size (e.g., a portable sewage submersible pump weighs only 30kg), quickly transferable via cables, suitable for temporary emergency response (e.g., urban drainage after heavy rain) and water extraction in remote areas.
(3) Application Scenarios: Expansion from “Conventional Transportation” to “Extreme Working Conditions”
Application Field | More Suitable for Centrifugal Pumps | More Suitable for Submersible Pumps |
---|---|---|
Environmental Conditions | Dry on-land environment, fixed installation (e.g., water supply for rooftop tanks in buildings) | Fully submerged environments (e.g., underground sewage tanks, deep-sea aquaculture water pumping), mobile scenarios (e.g., temporary flood control pumping) |
Transported Media | Clean water, low-viscosity liquids (e.g., water, kerosene), sewage without solid particles | Liquids containing solid particles (e.g., sewage with ≤5% sediment by volume), corrosive liquids (e.g., seawater, acid-base solutions, requiring stainless steel/rubber-coated impellers), high-temperature liquids (≤120℃, requiring special sealing materials) |
Working Condition Requirements | Large flow with low head (e.g., urban tap water pressurization, head ≤50 meters) | High head for long-distance transportation (e.g., deep well pumps can reach 300 meters head), cost-effective drainage (submersible pumps have 30% lower initial cost at the same power) |
(4) Efficiency and Energy Consumption: The Trade-off Between Cooling Advantages and Sealing Losses
- Efficiency Advantage of Submersible Pumps: Direct liquid cooling lowers motor winding temperature by 15%-20%, reducing copper and iron losses. Efficiency increases by 8%-12% under continuous operation (measured data: a 5.5kW submersible pump saves approximately 1,200kWh annually compared to the same-power centrifugal pump).
- Maintenance Advantage of Centrifugal Pumps: The motor is separated from the liquid, eliminating contact with sewage/corrosive media during maintenance. Replacing seals or impellers is more convenient (maintenance time reduced by 50%), suitable for hygienic-sensitive scenarios (e.g., food processing industry).
- Cavitation Risk Comparison: Centrifugal pumps are prone to cavitation (honeycomb pits on impeller surfaces) if the suction pipe leaks or suction lift is too high; submersible pumps have a 90% lower cavitation probability due to stable liquid pressure under immersion.
III. Selection Decision: Scenario-Oriented Optimal Solutions
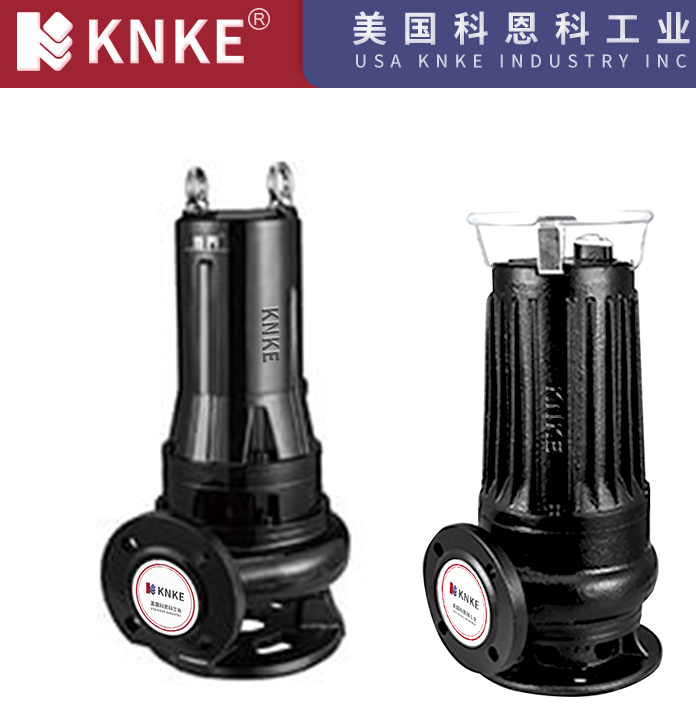
(1) Scenarios Prioritizing Centrifugal Pumps
- Fixed On-Land Working Conditions: Such as factory circulating water systems, secondary water supply for high-rise buildings (requiring long-term stable operation with clean liquids).
- Large Flow with Low Head: When the transportation head is <30 meters and flow rate >200m³/h, centrifugal pumps offer better cost-effectiveness (same parameters, centrifugal pumps are 20%-30% cheaper than submersible pumps).
- Priority on Maintenance Convenience: Frequent impeller/seal 检修 is required, and contact with transported media should be avoided (e.g., toxic liquids in the chemical industry; centrifugal pumps can be equipped with remote seal condition monitoring).
(2) Scenarios Prioritizing Submersible Pumps
- Underwater or Submerged Environments: Deep well water extraction (e.g., 200m deep wells, submersible pumps eliminate the need for pump houses), sewage tank drainage (direct immersion in sewage to avoid suction pipe blockage risks).
- Transportation of Complex Media: Rivers with sediment (≤10% volume ratio), seawater aquaculture water exchange (corrosion-resistant stainless steel submersible pumps required), construction site mud drainage (wear-resistant impeller models needed).
- Emergency and Mobility Needs: Temporary flood control pumping (rapid deployment in waterlogged areas), ship bilge drainage (stable operation during ship 晃动,anti-tilt design).
(3) Key Parameter Comparison Table
Parameter | Centrifugal Pump | Submersible Pump |
---|---|---|
Installation Method | Ground-fixed, requiring pipeline connection | Direct immersion in liquid, no priming needed |
Maximum Head | Usually ≤150 meters (restricted by suction lift) | Up to 500 meters (special deep well submersible pump models) |
Particle Passing Capacity | ≤5mm (closed impeller) | ≤20mm (vortex impeller) |
Initial Cost | Medium (5.5kW approx. 3,000 RMB) | Medium-high (same-power submersible pump approx. 3,500 RMB, including sealing costs) |
Maintenance Cost | Low (annual maintenance fee approx. 500 RMB) | Medium (annual seal replacement cost approx. 800 RMB, including hoisting equipment costs) |
IV. Future Trends: Technological Integration and Scenario Segmentation
With advancements in materials science and sealing technology, the boundaries between the two are dynamically evolving:
- Waterproofing of Centrifugal Pumps: Some high-end centrifugal pumps now adopt submersible-grade sealing (e.g., magnetic coupling drive), enabling short-term immersion in shallow water.
- Efficiency Enhancement of Submersible Pumps: Application of permanent magnet synchronous motors and variable frequency technology has increased submersible pump efficiency to IE5 level, reducing energy consumption by over 15%.
- Deepening Scenario Segmentation: Specialized models continue to emerge, such as low-noise submersible pumps for swimming pools and high-pressure submersible pumps for oil drilling (resistant to over 200bar pressure).
Centrifugal pumps and submersible pumps are not simply in a “substitution relationship” but represent the large-scale application of centrifugal pumps in general scenarios and the precise breakthrough of submersible pumps in special scenarios. When selecting equipment, users should first clarify three core factors: transportation environment (on-land/underwater), media characteristics (clean/complex), and installation conditions (fixed/mobile). Through matching analysis of technical parameters and actual working conditions, the optimal balance between equipment efficiency and cost can be achieved, allowing these two “envoys of centrifugal force” to maximize their value in their respective domains.