Corrosion Prevention Methods for Chemical Pumps
In modern industrial systems, pump corrosion remains one of the primary causes of equipment failure, posing significant challenges to production safety, economic efficiency, and sustainable development. Corrosion, mainly induced by environmental media through electrochemical reactions, leads to material degradation and the loss of functional integrity. This process results not only in direct economic losses but also substantially increases safety hazards, environmental risks, and resource wastage.
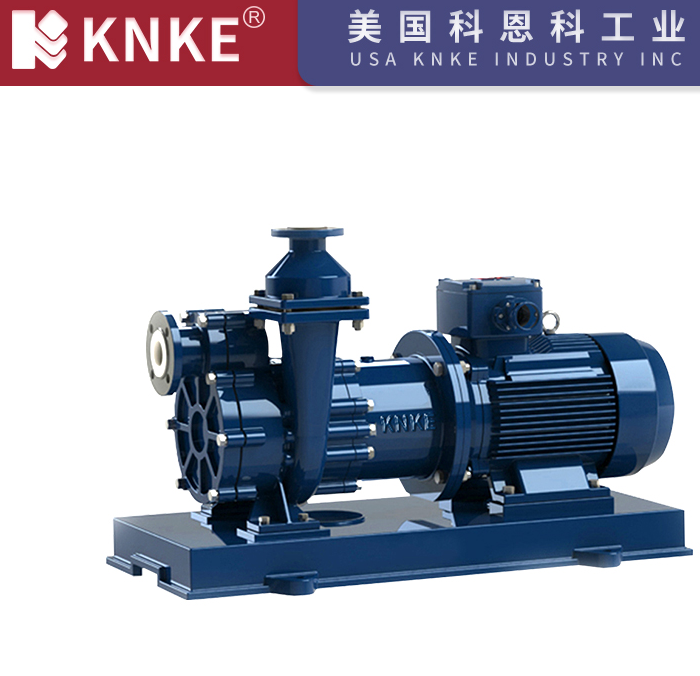
Types of Metal Corrosion
Metal corrosion can generally be categorized into two types: uniform corrosion and localized corrosion. Uniform corrosion occurs evenly across the surface of the material, whereas localized corrosion manifests in specific areas, causing severe damage. Common forms of localized corrosion include pitting, intergranular corrosion, crevice corrosion, hydrogen embrittlement, stress corrosion cracking, erosion-corrosion, and delamination. In extreme service environments such as petrochemical and marine engineering industries, localized corrosion poses a particularly serious threat to equipment integrity.
Importance of Corrosion Prevention in Chemical Pumps
As critical fluid transport equipment in harsh industrial sectors, chemical pumps must exhibit excellent corrosion resistance to ensure system reliability and operational safety. With increasingly demanding process conditions and heightened environmental protection standards, the importance of corrosion prevention technologies for chemical pumps has become even more pronounced. Inadequate protection can lead to frequent equipment failures or, in severe cases, catastrophic chemical accidents.
Current Prevention Strategies
Currently, frequent maintenance and component replacement are common approaches to manage corrosion issues in chemical pumps. However, these methods are costly and fail to address the root causes. A more sustainable solution involves integrating advanced materials science and surface engineering strategies, primarily including:
1. Selection and Application of Corrosion-Resistant Materials
During the design and manufacturing stages of chemical pumps, priority should be given to materials with high corrosion resistance, such as austenitic stainless steels, Hastelloy alloys, and titanium-based alloys. These materials significantly enhance the pump’s ability to withstand various corrosive media (acids, bases, and saline solutions), thereby extending service life.
2. Application of High-Performance Polymer Composite Coatings
The use of high-performance polymer composite coatings for surface protection has gained widespread acceptance in engineering practice. These coatings offer exceptional chemical resistance, high mechanical strength, and excellent adhesion. Compared to traditional pressure vessel welding repairs, polymer coatings provide advantages such as lower maintenance costs, simplified procedures, enhanced safety, and superior repair effectiveness.
3. Structural Optimization Design
Through rational structural design, such as minimizing gaps, blind spots, and flow dead zones, the occurrence of localized corrosion can be effectively suppressed. Additionally, optimizing the internal flow pathways to reduce turbulence, cavitation, and erosion further enhances the corrosion resistance of chemical pumps.
4. Precise Matching of Anti-Corrosion Coatings and Application Techniques
Selecting appropriate anti-corrosion coating systems (such as epoxy, polyurethane, and fluorocarbon coatings) based on specific service environments and strictly controlling the application parameters can substantially strengthen the corrosion barrier properties of the pump.
5. Systematic Maintenance and Corrosion Monitoring
Establishing a systematic corrosion monitoring and maintenance program enables early detection and intervention of corrosion issues. This proactive approach significantly reduces equipment failure rates, extends service life, and improves operational efficiency and safety.
In summary, effective corrosion prevention strategies for chemical pumps require a multidisciplinary approach combining materials engineering, mechanical design, and surface protection technologies. Only through the construction of systematic and scientifically validated protective measures can long-term, efficient operation of equipment be achieved, thus ensuring sustainable industrial development and promoting an environmentally friendly transformation.