Control Valves: Essential for Industrial Process Automation & Fluid Control
In modern industrial automation, a crucial piece of equipment acts much like the human heart. It precisely controls fluid flow, ensuring the entire system runs smoothly and efficiently. This is the control valve. From petrochemical plants to power generation, metallurgy, and light industry, control valves are everywhere, playing an indispensable role.
The Core Job of Control Valves
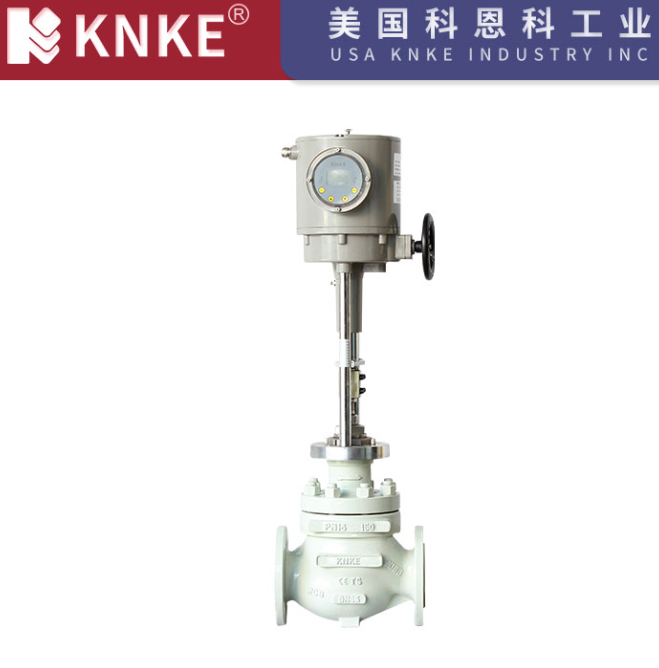
A control valve’s main job is regulation. It changes the flow area between its internal parts and the seat. This alters the fluid’s flow rate, pressure, temperature, or liquid level, keeping these process parameters within a set range.
Control valves primarily:
- Control Flow: This is their most basic and frequent use. By precisely adjusting how much fluid passes through, they meet exact needs for material transport and reaction ratios. For instance, in chemical production, control valves manage reactant feed rates for stable reactions and product quality.
- Regulate Pressure: Stable pressure is vital in many industrial processes. A control valve maintains system or equipment pressure at a preset value by adjusting fluid resistance in the pipeline. In boiler feedwater systems, for example, control valves manage feedwater pressure, preventing damage from extreme pressures.
- Manage Temperature: With temperature sensors and controllers, a control valve precisely regulates heating or cooling media flow. This controls the processed medium’s temperature. In a heat exchanger, a control valve manages steam or cooling water flow to maintain a stable outlet fluid temperature.
- Oversee Liquid Level: In tanks and columns, a control valve automatically adjusts inlet or outlet flow based on sensor signals. This keeps liquid levels within safe or required limits.
- Ensure Safety: Control valves also provide safety protection in specific situations. If the system acts abnormally (e.g., high pressure, uncontrolled temperature), the valve quickly shuts off or regulates the medium. This prevents accidents and protects equipment and personnel.
How Control Valves Operate
Control valves typically work within a closed-loop control system. First, a sensor detects the variable being controlled, such as flow or pressure. Next, it compares this signal to a setpoint. The resulting error signal goes to a controller. The controller calculates an output signal using a pre-programmed algorithm. This signal then drives the valve’s actuator, changing its opening. Ultimately, this action brings the controlled variable closer to the setpoint, achieving dynamic balance and stability.
Types and Uses of Control Valves 🛠️
As industrial technology advances, many types of control valves have emerged to meet different conditions and control needs. Common types include:
- Globe Valves (Single/Double-Seated): These have a simple structure and good sealing but typically handle smaller pressure differences.
- Cage Valves: Known for excellent stability, they suit high-pressure differences and large flow applications.
- Angle Valves: These are best for thick, easily crystallizing, or suspended-solid media.
- Three-Way Valves: They can divert, combine, or mix flows.
- Butterfly Valves, Ball Valves: Sometimes used for throttling, especially for large pipes and low-pressure differences.
Ultimately, control valves are essential components in modern industrial automatic control systems. Their precise and reliable regulation ensures stable, efficient, and safe production. With Industry 4.0 and smart manufacturing, control valves are becoming more intelligent, networked, and precise. They will play an even more critical role in future industrial production.