Common Types of Pumps Used in the Chemical Industry
Pumps are essential components in the chemical industry. They transport fluids, chemicals, slurries, and corrosive substances during different production stages. Choosing the right chemical pump improves safety, boosts efficiency, and extends equipment life. This article introduces the main types of chemical pumps commonly used today, including their working principles and materials.
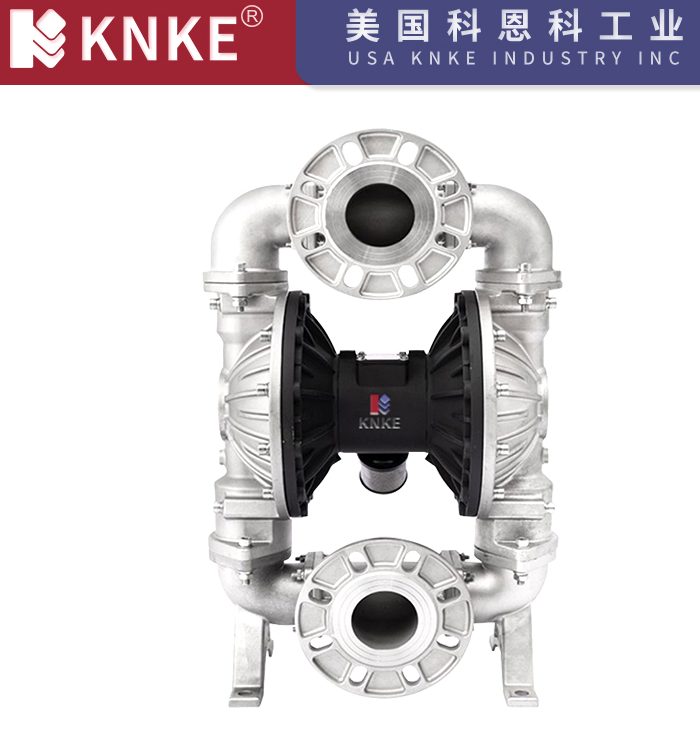
(1) Centrifugal Pumps in the Chemical Industry
Centrifugal pumps dominate chemical processing applications. They rely on a rotating impeller to generate liquid flow through centrifugal force. Because of their simple structure and continuous high-flow performance, many industries prefer them.
Common Types of Centrifugal Pumps:
- Water Pumps
These pumps move water and similar liquids used for cleaning, cooling, and general operations. - Corrosion-Resistant Pumps
These pumps handle acids, alkalis, and ammonia-based solutions. Manufacturers often use stainless steel or fluoroplastic to ensure resistance. Operators must select corrosion-resistant pumps when dealing with aggressive chemicals. - Oil Pumps
Engineers use oil pumps for transferring petroleum products. These pumps feature excellent sealing performance to avoid leakage and reduce fire risk. - Submerged Pumps (Vertical Pumps)
Facilities install these pumps inside storage tanks to transport corrosive or hazardous fluids. Although they serve various purposes, they tend to operate with lower efficiency. - Slurry Pumps (Solids-Handling Pumps)
These pumps handle liquids containing solid particles, such as sludge and slurry. They offer abrasion resistance, easy maintenance, and minimal clogging. Common subtypes include sewage pumps, sand pumps, and mud pumps. - Canned Motor Pumps (Sealless Pumps)
Industries use these pumps to move flammable, toxic, or radioactive materials. Since they operate without mechanical seals, they prevent leakage entirely. However, their efficiency is relatively low compared to standard pumps.
(2) Reciprocating Pumps – Focus on Diaphragm Pumps
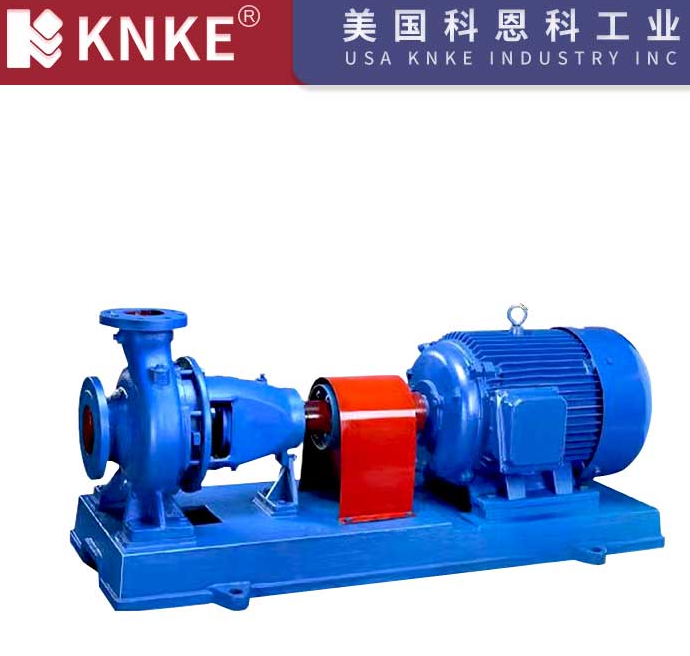
Reciprocating pumps move fluids through a back-and-forth motion. They are ideal for high-pressure or precise-dosing applications in chemical systems.
Common Types of Reciprocating Pumps:
- Diaphragm Pumps
These pumps handle thick liquids and slurries. Since they operate without seals in contact with the fluid, they work well with corrosive and hazardous materials. Additionally, they are self-priming and explosion-proof. - Triplex Plunger Pumps
Chemical plants often use these pumps to deliver high-pressure water or in hydrogenation units. - Steam Reciprocating Pumps
These pumps are usually steam-driven and appear in coking plants. They efficiently transport viscous oils during start-up processes. - Metering Pumps
Operators rely on these pumps for injecting precise chemical doses into pipelines, such as adding corrosion inhibitors or antiscalants.
(3) Classification by Pump Material
Besides function and mechanism, chemical pumps also differ by material composition. Selecting the correct material helps ensure chemical compatibility and reduces wear.
Common Pump Materials:
- Stainless Steel Chemical Pumps
These pumps resist corrosion and support a wide range of chemical applications. - Plastic Chemical Pumps
They provide cost-effective solutions for low to moderate corrosive tasks, especially with weak acids and alkalis. - Fluoroplastic Chemical Pumps
With extreme resistance to strong chemicals and heat, these pumps offer reliable operation in aggressive environments. - Electric Chemical Pumps
These motor-driven pumps support continuous flow in automated systems. - Air-Operated (Pneumatic) Chemical Pumps
Portable and explosion-proof, they handle flammable or dangerous fluids safely in temporary or mobile setups.
Frequently Asked Questions (FAQ)
1. What is the most common pump used in chemical plants?
Centrifugal pumps are the most popular choice due to their high flow capacity, reliability, and simplicity.
2. Which pump is best for corrosive chemicals?
Corrosion-resistant pumps, especially those made from stainless steel or fluoroplastics, work best with corrosive fluids like acids or alkalis.
3. Are diaphragm pumps suitable for chemicals?
Yes. Diaphragm pumps handle corrosive, abrasive, and viscous fluids effectively. They also prevent leaks and reduce contamination risks.