Common Faults and Maintenance Methods of Booster Pumps
Booster pumps are essential equipment for household water supply, industrial pipeline pressurization, and other scenarios. During long-term operation, they may encounter various faults. Timely detection and resolution of these issues not only prevent disruptions to water supply but also extend the equipment’s service life. This article summarizes seven common faults of booster pumps and corresponding solutions based on practical maintenance experience, helping users quickly troubleshoot and address problems.
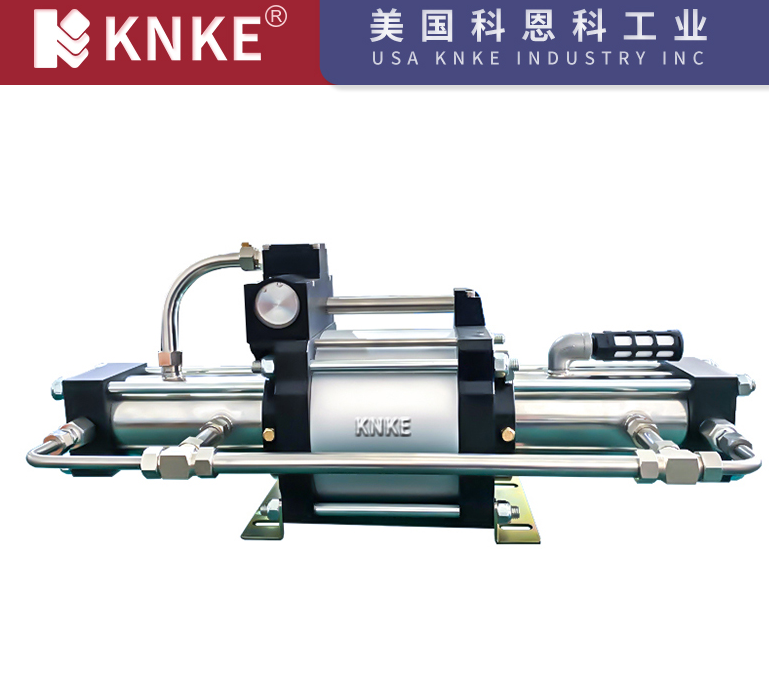
1. Leakage Issues: Locate Leaks and Repair Precisely
Symptoms: Water dripping from interfaces, seepage on the pump body surface, or water stains on the ground.
Causes:
- Aging and cracking of water pipes, wear of interface seals;
- Loose screws during installation, or misalignment between the pump body and pipeline;
- Minor leaks triggering the flow switch, causing frequent pump startups.
Solutions:
- Identify Leak Points: Turn off the power supply, inspect the inlet, outlet, valves, and connecting pipes section by section, and mark specific leakage positions;
- Replace Damaged Parts: Cut off aging pipes and replace them with pipes of the same specification; if the seal ring is deformed, apply waterproof glue and install a new seal ring;
- Reinforce Installation: Realign the pump body, tighten interface screws evenly, and use sealing tape if necessary to enhance tightness.
2. Failure to Start or Continuous Operation: Double Check Power and Pressure Systems
(1) Failure to Start
Possible Causes:
- Loose power plug, blown fuse, or short circuit in the wiring;
- Insufficient pressure in the water supply system (blocked main pipeline, low water tank level);
- Faulty pressure switch unable to detect startup pressure.
Solutions:
- Power Detection: Use a multimeter to check the voltage at the socket, replace the blown fuse, and repair loose wiring connections;
- Pipeline Cleaning: Remove the inlet filter, clear debris such as sand and rust, and check if the water tank level meets the minimum operating requirement of the pump;
- Calibrate Pressure Switch: Refer to the manual to adjust the start-stop threshold of the pressure switch (typically start pressure 0.1-0.2MPa, stop pressure 0.2-0.3MPa); replace the switch if it fails.
(2) Continuous Operation
Core Issues: The pressure switch cannot recognize that the system has reached the rated pressure, or the pipeline continuously releases pressure.
Measures:
- Turn off all water-consuming devices and observe if the pressure gauge drops. If it drops rapidly, inspect and repair hidden pipeline leaks;
- Manually press the pressure switch reset button. If ineffective, disassemble the switch to check for internal spring jams and replace it if necessary.
3. Inadequate Water Suction or Low Pressure: Comprehensive Check from Impeller to Air Blockage
Symptoms: Low water output, intermittent water flow, or no water after startup.
Potential Causes:
- Inlet valve not fully opened, or pipeline blocked by foreign objects;
- Impeller wrapped by debris, deformed blades, or rusted and stuck pump shaft;
- Air trapped in the pump body (especially after initial installation or maintenance), causing air blockage.
Resolution Process:
- Clear Blockages: Turn off the water source, disassemble the inlet pipe and impeller chamber, remove entangled debris like hair and plastic bags, and sand rusted pump shafts;
- Air Exhaustion: Unscrew the pump’s exhaust valve (if available) or the outlet screw until continuous water flow is observed, then tighten;
- Impeller Maintenance: If the impeller is severely worn, purchase a new compatible impeller according to the model, ensuring the rotation direction matches the label during installation.
4. Motor Faults: Watch Out for Overload and Heat Dissipation Issues
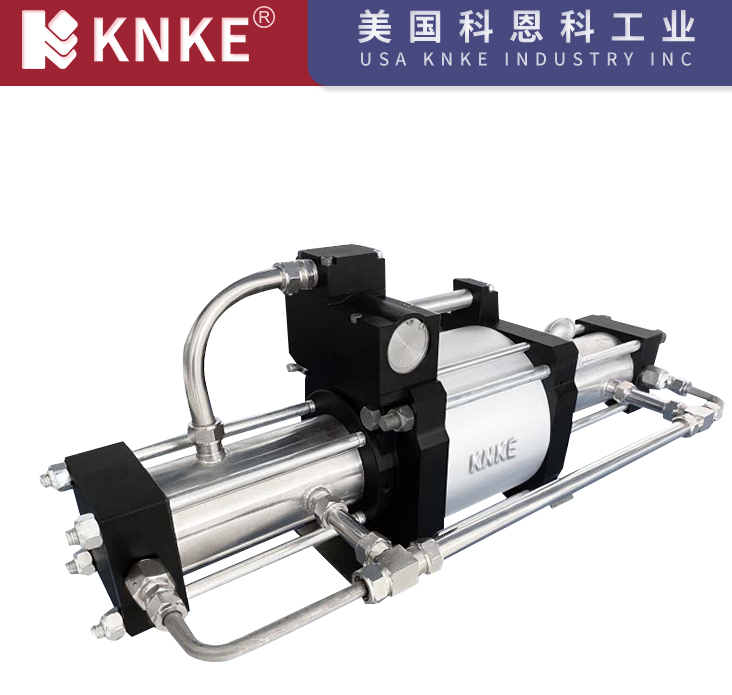
Common Symptoms: Abnormal motor heating, burning smell, or complete stop of rotation.
Main Causes:
- Long-term overload operation (e.g., working beyond the head range) leading to coil overheating and burnout;
- Lack of lubrication or wear of bearings, increasing operational resistance;
- Capacitor failure, unable to provide startup current.
Maintenance Tips:
- Emergency Shutdown: Power off immediately upon detecting abnormalities to avoid safety accidents caused by short circuits;
- Bearing Maintenance: Remove the motor casing, clean old grease, apply high-temperature resistant lubricant, and replace bearings with obvious wobble;
- Coil and Capacitor Replacement: Non-professionals are advised to replace the entire motor assembly. Capacitor faults can be addressed by replacing the capacitor (ensure voltage and capacity match the specifications).
5. Excessive Vibration and Noise: Stability of Installation is Key
Symptoms: Significant pump body shaking during operation, accompanied by metallic knocking or unusual noises.
Root Causes:
- Loose base gaskets, untightened fixing screws, leading to resonance;
- Unbalanced impeller (e.g., damaged blades) or bent pump shaft.
Solutions:
- Stabilize the Base: Install rubber shock-absorbing pads between the pump body and the installation surface, tighten fixing screws diagonally in batches, and ensure horizontal installation;
- Impeller Calibration: Disassemble the impeller to check for notches. Slight wear can be repaired by grinding, while severe deformation requires replacement. If the pump shaft is bent, replace it and conduct a dynamic balance test.
6. Frequent Startups: Ensure Pressure Stability and Sealing
Impact: Increases motor wear and shortens equipment life.
Main Reasons:
- Minor pipeline leaks (e.g., faucet valve seepage) triggering false detection by the flow switch;
- Too small pressure difference setting on the pressure switch (start-stop pressure difference < 0.05MPa), causing frequent system pressure fluctuations.
Strategies:
- Leak Detection and Repair: Turn off all water points, observe if the water meter moves, and replace faucet seals or valves promptly upon detecting leaks;
- Adjust Pressure Settings: Increase the start-stop pressure difference of the pressure switch (recommended 0.1-0.15MPa) to allow the pump to operate within a stable pressure range.
7. Preventive Maintenance: Three Tips to Extend Equipment Life
- Regular Maintenance: Clean the inlet filter every quarter, inspect the aging of seals annually, and replace vulnerable parts such as O-rings and gaskets in a timely manner;
- Standard Operation: Avoid pump dry running (install a water shortage protection device) and control the flow within rated parameters during operation;
- Professional Service: For complex faults (e.g., pressure tank air bag failure, frequency converter malfunction), contact after-sales service instead of disassembling precision components manually.
Troubleshooting booster pumps should follow the principle of “from simple to complex, from external to internal”, starting with external factors such as power supply and pipelines before inspecting internal components. Daily cleaning, lubrication, and pressure calibration can effectively reduce fault occurrences. For complex issues like motor burnout or control circuit faults, seek professional help promptly to avoid greater damage from improper operations. Through scientific maintenance and timely repairs, booster pumps can operate stably for a long time, providing reliable support for household and industrial water supply.