Classification of Electric Butterfly Valves
Electric butterfly valves are essential components in fluid control systems, commonly used to regulate gases, liquids, and steam. These valves come in a variety of designs, each catering to specific operational requirements. In this article, we will explore the classification of electric butterfly valves based on structure, sealing material, and sealing method.
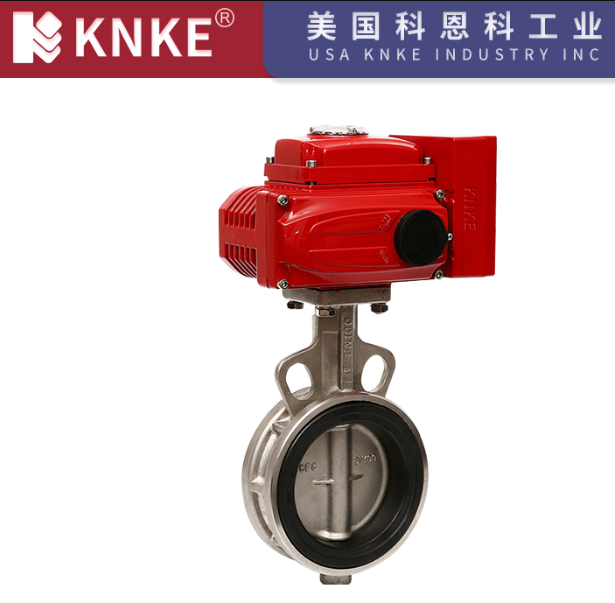
1. Classification by Structure Type
1.1 Center Sealing Electric Butterfly Valve
The center sealing electric butterfly valve features a simple design, where the sealing surface is located at the center of the valve body. This structure works well in low-pressure applications and straightforward fluid control systems. As a result, it provides stable sealing performance, making it ideal for controlling common fluids such as water and air. Therefore, users can rely on this type of valve for low-demand applications.
1.2 Single Eccentric Sealing Electric Butterfly Valve
In the single eccentric sealing valve, an eccentric disc design ensures that the valve plate first contacts the seat before gradually compressing, forming a tight seal. This design reduces friction and wear, extending the valve’s lifespan. Consequently, it is often used in medium-pressure systems, where reliable performance is needed for industrial applications. Furthermore, its design minimizes operational disruptions, making it a preferred choice for many industries.
1.3 Double Eccentric Sealing Electric Butterfly Valve
The double eccentric electric butterfly valve builds upon the single eccentric design by introducing two offset axes. This advancement enhances the precision of the seal, improving overall performance. Therefore, this valve is ideal for higher-pressure applications and is widely used in industries such as chemicals, power generation, and petroleum. Additionally, the double eccentric design ensures smoother operation, reducing maintenance needs.
1.4 Triple Eccentric Sealing Electric Butterfly Valve
The triple eccentric electric butterfly valve incorporates a three-axis eccentric design, which significantly improves sealing reliability, wear resistance, and durability. It excels in high-pressure, high-temperature, and harsh environments. As a result, it is widely used in critical applications such as oil and gas pipelines and liquid transportation systems. Moreover, the triple eccentric design ensures the valve will continue to perform efficiently over time, even in the toughest conditions.
2. Classification by Sealing Surface Material
2.1 Soft Sealing Electric Butterfly Valve
Soft sealing electric butterfly valves feature non-metallic soft materials for the sealing surface. These valves offer excellent sealing performance in low-pressure systems and are suitable for fluids like water and air. Therefore, they are ideal for applications where sealing requirements are moderate. Furthermore, soft sealing valves are cost-effective and provide reliable operation in standard conditions.
Soft Sealing (Non-Metallic Soft Materials)
This valve design is perfect for fluid control systems operating under low pressure. It ensures a tight seal while delivering dependable performance in typical environments.
Soft Sealing (Non-Metallic to Metallic Hard Materials)
Soft sealing valves designed with a combination of non-metallic and metallic materials are used in higher-pressure systems or where the fluid may be corrosive. Consequently, these valves are common in industries like water treatment, power generation, and petrochemicals.
2.2 Metal Hard Sealing Electric Butterfly Valve
Metal hard sealing electric butterfly valves use metal materials for both the valve plate and seat. These valves perform exceptionally well under high-temperature, high-pressure, and corrosive conditions. As a result, they are highly suitable for industries such as petroleum, natural gas, and metallurgy, where durability and reliability are critical. Additionally, the metal hard sealing design provides enhanced resistance to wear and tear, ensuring long-lasting operation.
3. Classification by Sealing Method
3.1 Forced Sealing Electric Butterfly Valve
Forced sealing electric butterfly valves generate sealing force through external energy. This force can either come from compressing the valve plate against the valve seat or applying external torque to the valve shaft. This external application of sealing pressure helps ensure tight and reliable seals. Therefore, forced sealing valves are used in applications that require precise control and strong sealing capabilities.
Elastic Sealing Electric Butterfly Valve
Elastic sealing valves rely on the elasticity of the valve seat or plate to generate sealing force. These valves are ideal for low-pressure systems, where moderate sealing pressure is sufficient. Consequently, they are often employed in systems with standard sealing requirements, ensuring reliable operation in less demanding environments.
External Torque Sealing Electric Butterfly Valve
External torque sealing valves use torque applied to the valve shaft to generate the necessary sealing force. This design is particularly beneficial in applications that require precise control and high sealing performance, such as in chemical, petroleum, and food processing industries. As a result, external torque sealing valves ensure efficient sealing in critical systems.
3.2 Pressure-assisted Sealing Electric Butterfly Valve
Pressure-assisted sealing electric butterfly valves generate sealing force by pressurizing elastic sealing elements. These valves are most effective in medium to high-pressure systems, ensuring stable sealing even under varying pressure conditions. Furthermore, they provide reliable sealing in applications where pressure fluctuations are common, making them suitable for diverse industries.
3.3 Self-sealing Electric Butterfly Valve
Self-sealing electric butterfly valves rely on the pressure of the fluid itself to generate sealing force. As fluid pressure increases, the seal between the valve plate and seat becomes tighter, enhancing the sealing effect. Therefore, these valves are ideal for automated systems and applications where fluid pressure naturally fluctuates. Additionally, self-sealing valves reduce the need for external sealing mechanisms, offering a cost-effective solution.
Electric butterfly valves are available in a wide range of designs, each tailored to meet specific operational needs. By choosing the right valve based on structure, sealing material, and sealing method, users can optimize the performance and lifespan of their fluid control systems. Ultimately, understanding the features of each valve type allows users to make informed decisions, ensuring reliable, efficient, and long-lasting operation across industries.