Causes of Errors in Orifice Flow Meters and How to Address Them
Orifice flow meters are widely used in industries such as petroleum, chemical engineering, metallurgy, power generation, heating, and water supply. These meters are crucial for measuring the flow of gases, steam, liquids, and other media. Given their importance in industrial processes, ensuring accurate flow measurement is critical for controlling production and maintaining safety. However, over time, various factors may cause errors in the measurement readings of orifice flow meters. This article explores the common causes of errors in orifice flow meters and provides corresponding solutions.
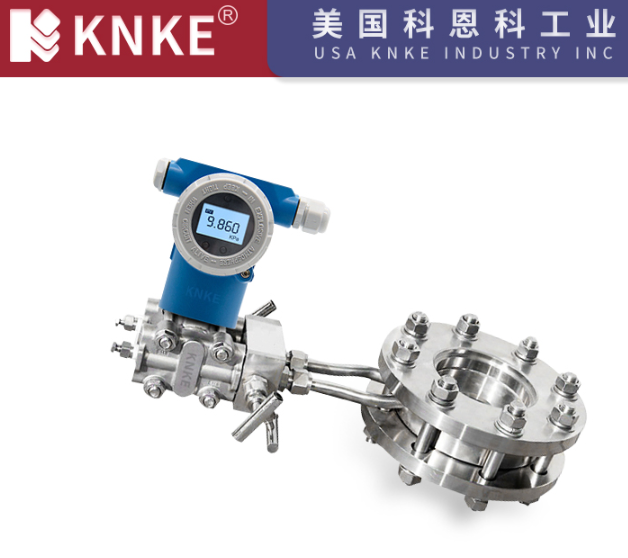
1. Flow Area Changes Leading to Errors
Cause: Accumulation of Dirt on the Orifice Plate
Over time, dirt and impurities may accumulate on the surface of the orifice plate. This can reduce the flow area, causing the pressure differential (ΔP) to increase and ultimately leading to an overestimation of the flow rate.
Solution: Regular Cleaning of the Orifice Plate
To ensure accurate measurement, regularly check the cleanliness of the orifice plate and surrounding areas. If dirt or impurities are found, clean the plate to restore its flow area and ensure unobstructed flow. Follow proper cleaning procedures to avoid damaging the plate.
2. Zero Drift in the Differential Pressure Transmitter
Cause: Zero Drift Over Time
As the differential pressure transmitter is used over time, its zero point may drift, especially if calibration is not regularly performed. A positive drift will cause the pressure differential to increase, which results in an overestimation of the flow rate.
Solution: Periodic Calibration of the Transmitter
To maintain measurement accuracy, regularly calibrate the transmitter to ensure its zero point remains accurate. Calibration intervals should be adjusted based on usage and environmental conditions.
3. Insufficient Upstream and Downstream Straight Pipe Lengths
Cause: Inadequate Straight Pipe Lengths
Orifice flow meters require certain lengths of straight pipe both upstream and downstream to ensure that the gas flow is fully developed. If these lengths are insufficient, the flow may be disturbed, leading to measurement errors. Additionally, the presence of elbows or bends in the pipe can cause the flow meter to overestimate the flow rate.
Solution: Optimize Pipe Design
Ensure the pipe design complies with the recommended straight pipe length requirements for accurate flow measurement. If necessary, modify the pipeline to add sufficient straight sections, or install flow straighteners upstream of the orifice meter to ensure the gas flow is fully developed.
4. Incorrect Orifice Plate Thickness
Cause: Non-Compliant Orifice Plate Thickness
The thickness of the orifice plate directly impacts the resistance the fluid encounters when flowing through the meter. The standard thickness of the orifice plate should fall between the orifice diameter (e) and 0.05 times the pipe diameter (D). If the plate thickness is outside this range, it will increase the resistance to flow, resulting in an overestimation of the flow rate.
Solution: Check and Replace the Orifice Plate
Regularly check the thickness of the orifice plate to ensure it complies with the standard specifications. If the plate thickness exceeds the acceptable range, replace it with one that meets the required specifications to restore accurate flow measurement.
5. Leakage in the Three-Valve Manifold of the Differential Pressure Transmitter
Cause: Leakage in the Low-Pressure Valve
The three-valve manifold in the differential pressure transmitter controls the pressure differential measurement. If the low-pressure valve leaks, the pressure differential will be artificially increased, leading to an inaccurate flow rate measurement.
Solution: Inspect and Repair the Three-Valve Manifold
Inspect the three-valve manifold, particularly the low-pressure valve, to ensure it is properly sealed. If a leak is detected, tighten the valve or replace it if necessary to prevent further leaks and ensure accurate flow measurements.
6. Uneven Liquid Levels in the Isolation Liquid
Cause: Unequal Liquid Heights in the Isolation System
The isolation liquid in the impulse lines separates the high-temperature media from the differential pressure transmitter. If the liquid level in the low-pressure side is higher than the high-pressure side, the pressure differential will increase, causing an overestimation of the flow rate.
Solution: Adjust Isolation Liquid Levels
Regularly check the liquid levels in both the high-pressure and low-pressure sides of the impulse lines. Ensure the levels are consistent. If the liquid levels are not equal, calibrate them accordingly. Additionally, verify that the height of the condensate tank is higher than the steam pipeline. If it is not, raise the height of the condensate tank to ensure proper operation.
Orifice flow meters play an essential role in industrial applications, and any measurement error can lead to unnecessary losses in production. By performing regular maintenance and calibration on the components of the flow meter, such as cleaning the orifice plate, calibrating the transmitter, optimizing pipe design, and ensuring proper plate thickness, errors can be minimized, and the accuracy of measurements can be maintained. Regular maintenance not only ensures the long-term stable operation of the flow meter but also enhances production efficiency and safety.