Application of Angle Control Valves: Benefits, Installation Techniques, and Best Practices
Angle control valves are widely used in chemical, petroleum, metallurgy, and other industrial processes due to their simple flow path and low resistance characteristics. Their efficient design provides excellent control in systems with high pressure drops, high-viscosity fluids, suspended solids, and sticky or fouling-prone media. This article explores the unique features of angle control valves, compares forward and reverse installation methods, and provides best practices and FAQs to help engineers and maintenance professionals select and operate these valves safely and effectively.
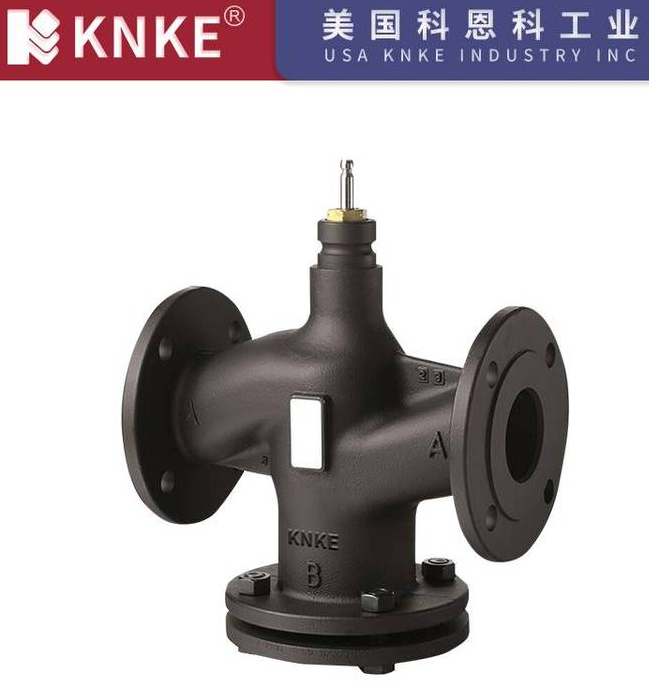
Overview of Angle Control Valve Features
Angle control valves are designed with an angular valve body, while the internal mechanisms remain similar to those of single-seat valves. This design offers several advantages:
- Simple Flow Path and Low Resistance:
The streamlined internal flow path minimizes pressure loss across the valve. This makes it especially useful in high-pressure drop applications where fluid energy efficiency is critical. - Versatile Application Range:
Ideal for handling high-viscosity fluids, media containing suspended solids, and substances prone to fouling, these valves ensure smooth and reliable operation even under demanding conditions. - Easy to Clean and Self-Cleaning:
The uncomplicated internal structure not only simplifies routine maintenance and cleaning but also facilitates self-cleaning, thereby preventing the buildup of deposits that can lead to clogging.
Forward Installation vs. Reverse Installation
Forward Installation: The Standard Approach
In most operating conditions, angle control valves are installed in the conventional forward orientation—typically with bottom inlet and side outlet. This method is preferred because:
- Stable Operation:
Forward installation maintains balanced forces on the valve plug and reduces uneven pressure distribution, protecting the valve from premature wear. - Smooth Fluid Flow:
The valve is optimized for fluid dynamics, ensuring a more stable and consistent flow while reducing turbulence and the potential for vibration. - Maintenance Efficiency:
Conventional installation aligns with standard process designs, simplifying both installation and routine maintenance.
Reverse Installation: Optimized for High Pressure Drops and Challenging Media
Under conditions such as high-pressure differentials, high viscosity, sticky media, and the presence of suspended particles, reverse installation (with the material inlet on the process side and the outlet at the bottom) may be recommended. The benefits of reverse installation include:
- Enhanced Force Balance:
By adjusting the fluid flow direction, reverse installation improves the balance of forces, reducing stress and wear on the valve plug. - Improved Flow of Difficult Fluids:
Reverse flow arrangements promote the smoother movement of high-viscosity or particulate-laden fluids, reducing the risk of fouling and blockages. - Extended Valve Lifespan:
Reducing unbalanced forces and minimizing direct impact on the valve plug helps extend the operational life of the valve.
Key Operational Considerations
While reverse installation offers significant benefits under specific conditions, certain operational precautions are necessary:
- Avoid Prolonged Small-Opening Conditions:
When using reverse installation, it is critical to prevent long-term operation at low openings. Prolonged small openings can cause severe vibrations and lead to damage of the valve plug. - Trial Production Phase Cautions:
During trial production phases, where the process load may be low and conditions are not yet optimized, keeping the valve at a small opening for extended periods should be avoided to prevent undue wear or damage. - Monitoring and Maintenance:
Continuous monitoring of valve performance is advised, particularly in high-stress environments. Adjusting the valve opening according to operational needs and ensuring regular maintenance can mitigate risks of clogging, vibration, or premature wear.
Frequently Asked Questions (FAQ)
Q1: What is an angle control valve?
A: An angle control valve is a type of valve known for its angular design and simplified internal structure, offering a streamlined flow path and minimal resistance. It is particularly beneficial in high-pressure drop and challenging media applications.
Q2: When should I choose forward installation over reverse installation?
A: Forward installation (bottom inlet and side outlet) is best for standard conditions where fluid properties and pressure drops are within typical ranges. Reverse installation is recommended in cases of high pressure drops, high-viscosity fluids, and when dealing with media that are prone to fouling.
Q3: How does reverse installation improve the performance of angle control valves?
A: Reverse installation helps balance unbalanced forces caused by high pressure drops and reduces direct wear on the valve plug. It also facilitates better fluid dynamics in systems with sticky or particulate-laden media, which minimizes the risk of fouling and blockage.
Q4: Why must prolonged small opening conditions be avoided during reverse installation?
A: Operating the valve for extended periods in a small opening state can lead to excessive vibrations, thereby increasing the risk of damaging the valve plug. This precaution is especially important during trial production stages where process parameters may not be fully optimized.
Q5: What maintenance practices help ensure the longevity of angle control valves?
A: Regular monitoring, periodic cleaning, and ensuring optimal opening conditions (avoiding prolonged low-opening operation) are key practices. Additionally, adjustments based on real-time process requirements can help reduce wear and extend the valve’s service life.
Conclusion
Angle control valves are essential components in many industrial processes due to their simple flow design, low resistance, and ability to handle complex media types. Understanding the differences between forward and reverse installations, along with their respective operational guidelines, enables engineers to optimize fluid control, enhance efficiency, and safeguard equipment. By adhering to best practices and continuous monitoring, these valves ensure reliable performance and longevity in challenging operating conditions.