Analysis of the Causes and Solutions for Difficult Operation of Large-Diameter Valves
Large-diameter valves are essential in critical industrial applications, such as boiler outlets, steam distribution cylinders, and main steam lines. However, their operation can be extremely challenging due to several factors. These include high pressure, large flow rates, and complex fluid dynamics. Let’s explore the key reasons that make operating large-diameter valves difficult.
1. The Enormous Torque Required to Close the Valve
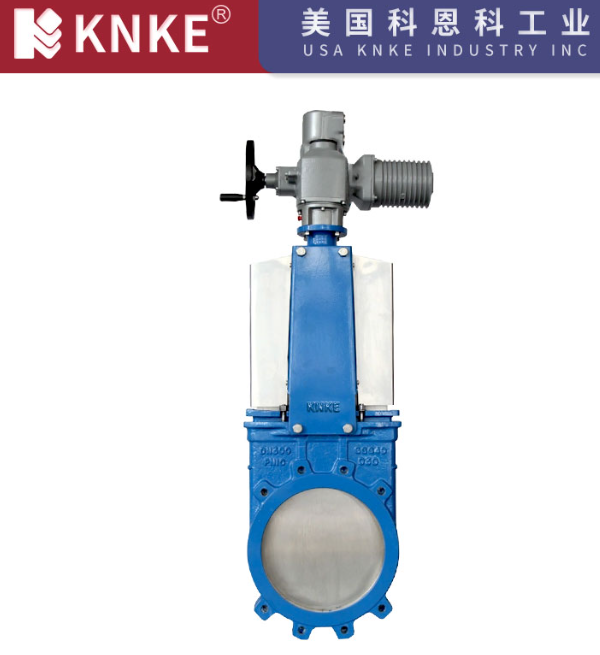
In large-diameter valves, particularly globe valves, operators must overcome substantial forces to close the valve. The force required results from multiple factors:
- Axial Thrust (Fa): This force is a result of the pressure differential between the inlet and outlet sides of the valve. As the valve closes, axial thrust increases. Near closure, this thrust can approach the system’s full pressure, making it increasingly difficult for an operator to close the valve manually. For example, in a DN200 valve operating on a 10 bar steam pipeline, the axial thrust alone can exceed 3140 kg, far beyond the capabilities of a human operator.
- Frictional Forces (Fb and Fc): The friction between the packing and valve stem (Fb), as well as between the valve stem and plug (Fc), increases as the valve closes. Over time, corrosion or wear can intensify this friction, making it even harder to close the valve.
Combined, these forces create a torque that exceeds what manual operation can handle. The larger the valve, the more challenging it becomes to close it.
2. Seal Face Damage and Leakage
Large-diameter valves are often exposed to harsh operating conditions. The following factors contribute to damage and leakage in the valve’s sealing surfaces:
- Erosive Effects of Steam: High steam flow velocity, particularly when it contains water vapor and impurities, leads to erosion of the valve’s sealing surfaces. Over time, this erosion compromises the valve’s ability to seal properly.
- Cavitation and Vaporization: When steam is overheated or when there are fluctuations in pressure, cavitation and vaporization occur. These phenomena cause localized low-pressure areas that damage the sealing surfaces, leading to leaks.
- Chemical Corrosion: Steam from boilers often contains acidic or alkaline substances, especially when water treatment is inadequate. These corrosive substances can attack the valve’s sealing surfaces, reducing their effectiveness and causing leaks.
3. Erosion During Preheating and Flow Fluctuations
Another challenge comes from the preheating of pipelines and the fluctuation of steam flow. These issues contribute to the erosion of valve components.
- Flow Fluctuations: In applications like steam distribution cylinders and boiler outlets, the steam flow often varies due to changes in production demand. This fluctuation in flow velocity can result in cavitation, which accelerates wear on the valve’s sealing surfaces.
- Improper Pipeline Preheating: Large-diameter valves require preheating before full valve opening to avoid thermal shock. If preheating is not done properly, the valve may remain partially open for long periods, leading to increased erosion due to low steam flow. Proper preheating ensures that the valve operates under optimal conditions, reducing wear.
Solutions for Overcoming the Difficulty in Operating Large-Diameter Valves
To improve the operation of large-diameter valves and address the challenges above, several solutions can be applied.
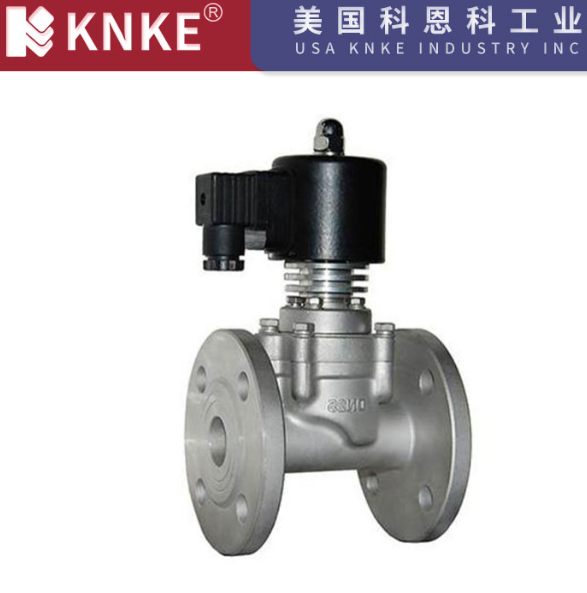
1. Use Bellows-Sealed Valves
To reduce the friction associated with traditional valve designs, bellows-sealed valves are an excellent alternative. The bellows seal prevents the valve stem from contacting the packing directly, which reduces friction and makes the valve easier to operate. This also helps prevent leakage, offering improved performance in high-pressure and high-flow applications.
2. Use of Erosion-Resistant Materials
Choosing high-performance materials for valve components, such as Stellite or other erosion- and corrosion-resistant alloys, is essential. These materials help extend the lifespan of the valve and maintain its sealing integrity. Using materials that are resistant to wear and corrosion reduces maintenance costs and downtime.
3. Dual-Disc Valve Structure
In large-diameter valves, a dual-disc structure can reduce the risk of excessive erosion caused by small valve openings. This design distributes the flow over two discs, preventing localized erosion and improving the valve’s sealing performance. Additionally, dual-disc valves perform better under fluctuating flow conditions, ensuring stable operation even when steam demand changes.
4. Optimize Pipeline Preheating
Properly controlling the preheating process is crucial for preventing valve damage. The steam flow rate and pressure should be managed to ensure gradual heating of the pipeline. This helps avoid thermal shock and excessive wear on the valve’s sealing surfaces. By ensuring the valve is fully preheated before opening, you can reduce the likelihood of erosion.
Operating large-diameter valves can be challenging due to the combination of high axial thrust, frictional forces, and erosive conditions in high-pressure steam systems. By using bellows-sealed valves, selecting erosion-resistant materials, employing dual-disc valve designs, and optimizing pipeline preheating, you can improve valve performance and reduce maintenance. These strategies help ensure the longevity and reliability of large-diameter valves in demanding industrial environments.