Analysis of Causes and Solutions for Vacuum Damper Valve Air Leaks
Vacuum damper valves play a crucial role in controlling airflow direction and pressure regulation, especially in vacuum systems. These valves are essential for ensuring smooth system operations by opening and closing the air path as required. However, when a vacuum damper valve experiences air leaks, it can negatively impact system performance and reliability. Therefore, understanding the common causes of air leaks and addressing them promptly is vital for engineers to maintain optimal valve function.
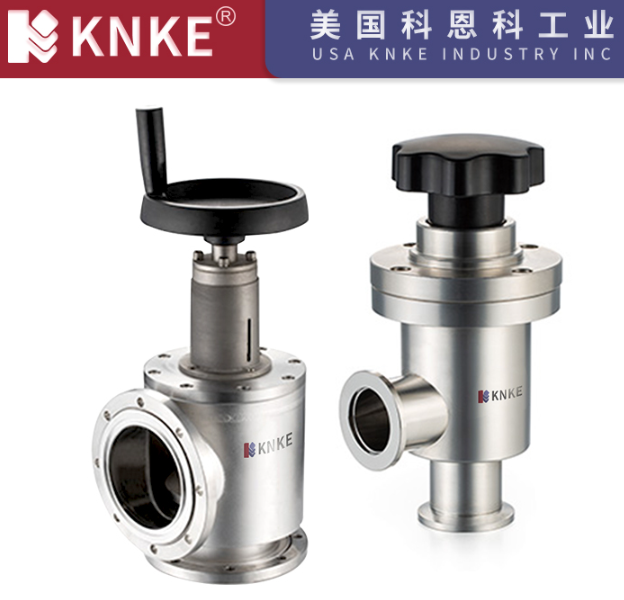
1. Cylinder Wall Damage Leading to Air Leaks
Vacuum damper valves operate by controlling the up-and-down movement of a rod within a cylinder to open or close the airflow. Due to this constant motion, the inner wall of the cylinder and the piston ring experience frequent friction, which over time can cause wear or damage. Once the cylinder wall is compromised, the piston ring can no longer form an effective seal, leading to air leakage.
Solution:
- Regularly inspect the cylinder walls and piston rings for wear and damage.
- Use materials with high wear resistance for the cylinder and piston to improve durability.
- Apply appropriate lubricants to reduce friction between the piston and cylinder.
- Replace piston rings periodically to prevent seal failure due to aging or excessive wear.
2. Manufacturing Tolerances and Seal Failures
The manufacturing process plays a significant role in the valve’s sealing ability. Any discrepancies in the dimensions of critical components, such as the cylinder or exhaust holes, can lead to poor sealing. For example, if the exhaust holes are drilled too deep, they could breach the cylinder wall, causing an internal air leak.
Solution:
- Ensure tight control over the tolerances of critical components during the design and manufacturing phases.
- Use high-precision CNC machines to minimize dimensional errors.
- Implement thorough quality checks on components, particularly on the exhaust holes and sealing surfaces, to prevent breaches or misalignment.
3. Wear Between Cylinder and Shaft Leading to Air Leaks
The interaction between the cylinder and shaft is another common cause of air leaks in vacuum damper valves. Over time, as the valve undergoes repeated operation, the shaft can experience wear, leading to poor sealing between the shaft and the cylinder. This diminished sealing capability results in air leakage.
Solution:
- Perform regular maintenance to inspect and polish the shaft to ensure a smooth surface and proper fit.
- Use wear-resistant materials such as carbide or ceramic coatings for the shaft to extend its lifespan.
- Ensure that the fit between the shaft and cylinder is accurate to reduce wear and improve sealing efficiency.
4. Improper Installation of Exhaust Holes and Other Components
The improper installation of exhaust holes or other sealing components can also cause air leaks. Over-tightening or using excessive force during installation can damage sealing surfaces or misalign components, leading to leaks.
Solution:
- Use torque-controlled tools during installation to ensure proper tightness without over-tightening or under-tightening.
- Perform routine checks to verify that all components, including exhaust holes and seals, are installed correctly and functioning as intended.
- Conduct pressure tests after installation to detect any potential leaks early.
5. Aging of Sealing Materials
With prolonged use, sealing components such as rubber O-rings and gaskets can become brittle, cracked, or deformed. This degradation reduces their ability to form effective seals, resulting in air leaks.
Solution:
- Replace sealing materials regularly, especially after extended use or in high-pressure environments.
- Use advanced sealing materials such as fluorocarbon or polyurethane, which are more resistant to aging and chemical degradation.
- Monitor the condition of seals and gaskets through regular inspections, and replace them before failure occurs.
6. Preventative Maintenance and Best Practices
In addition to addressing the root causes of air leaks through design and manufacturing improvements, regular maintenance is critical to prolonging the life of a vacuum damper valve. Engineers should establish a detailed maintenance plan that includes scheduled inspections, lubrication, and parts replacement. Proper training for operators is also essential to ensure that the valves are used correctly, preventing damage from improper handling.
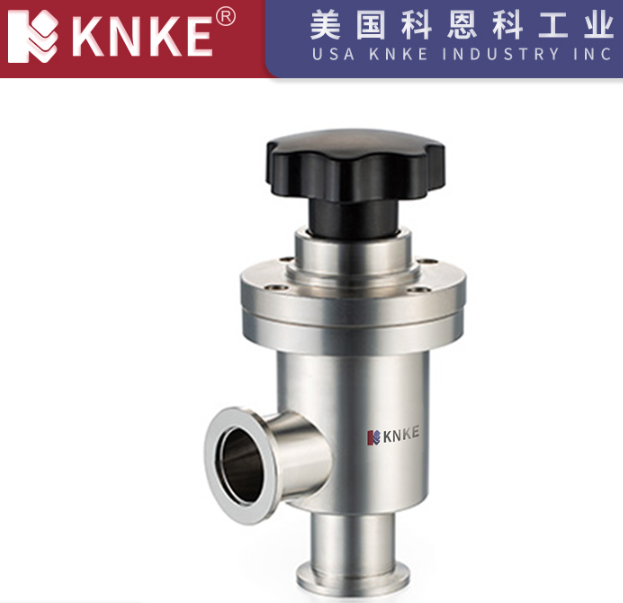
Maintenance Recommendations:
- Develop a comprehensive maintenance schedule based on usage patterns and manufacturer recommendations.
- Conduct thorough inspections at least once per year, particularly after periods of heavy use.
- Perform leak detection tests regularly to identify potential issues before they affect system performance.
Air leaks in vacuum damper valves can severely affect system performance and reliability. By understanding the common causes of these leaks, engineers can implement effective solutions to enhance valve sealing, minimize wear, and extend valve lifespan. Regular maintenance, precise manufacturing, proper installation practices, and the use of high-quality materials are all essential to ensuring that vacuum damper valves continue to operate efficiently. By addressing these factors proactively, engineers can prevent costly downtime and improve the overall performance of the system.