Classification of Pneumatic Butterfly Valves
Pneumatic butterfly valves, driven by compressed air, use an actuator to rotate a valve stem 90 degrees. This rotation allows them to open, close, or regulate fluid flow. Consequently, they are widely used across various industries, including petroleum, chemical, power, metallurgy, light industry, food, and pharmaceuticals. Their simple structure, compact size, light weight, easy operation, and good sealing make them a popular choice.
We can classify pneumatic butterfly valves in many ways. Typically, we categorize them based on the following key aspects:
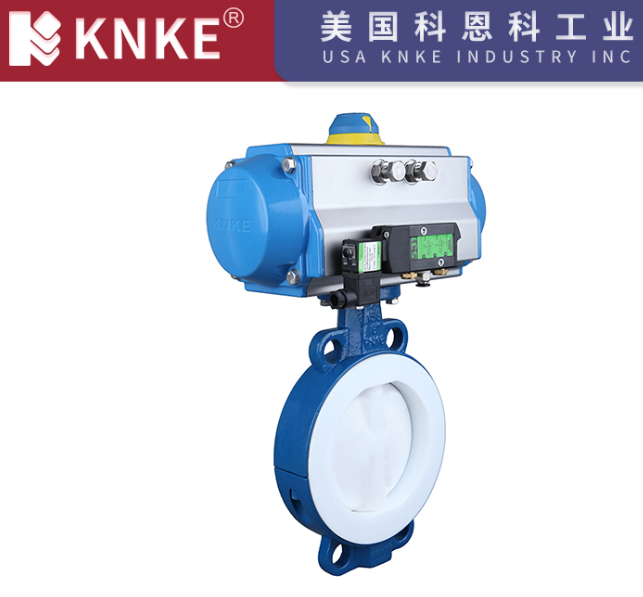
I. Classified by Sealing Type
Soft-Sealed Butterfly Valves use non-metallic materials like rubber, PTFE, or NBR as the sealing element between the valve seat and the disc. Ultimately, these offer excellent sealing performance, making them suitable for corrosive and clean media, and they come at a relatively lower cost. However, they are not resistant to high temperatures or pressures and generally have a shorter lifespan. You’ll find them commonly used in water treatment, food and beverage, and pharmaceutical industries.
Hard-Sealed Butterfly Valves, conversely, employ metallic materials such as stainless steel, alloy steel, or hard alloys for sealing between the valve seat and the disc. Therefore, these valves resist high temperatures, high pressures, and wear, leading to a long lifespan. On the other hand, their sealing performance can be relatively poorer, and they are not suitable for media containing solid particles. Furthermore, they come at a higher cost. They are typically found in high-temperature and high-pressure conditions within petroleum, chemical, power, and metallurgical industries.
II. Classified by Connection Type
Wafer Type Butterfly Valves lack flanges on the valve body; instead, bolts clamp them between pipeline flanges. As a result, they boast a compact structure, are easy to install, and save space. However, removing them requires dismantling the pipeline flanges. You’ll often see them in pipeline systems where space is limited.
Flanged Type Butterfly Valves feature flanges on the valve body, connecting to pipeline flanges with bolts. Consequently, they provide a secure and reliable connection, making them easy to dismantle and maintain. Nevertheless, they are relatively larger in size and weight. These are commonly applied in pipeline systems requiring frequent dismantling and maintenance.
Welded Type Butterfly Valves have their valve body directly welded to the pipeline. This design ensures the best sealing performance, making them suitable for high-temperature, high-pressure, and high-vibration conditions. Installation and removal, however, are difficult, and they are not designed to be removable. Therefore, they are used in petroleum, chemical, and other applications with extremely high sealing requirements.
Lug Type Butterfly Valves (Single-Flange Butterfly Valves) have lugs on the valve body, allowing for single-sided removal, which is convenient for repair or replacement. This means you can repair them without affecting the pipeline; some models can even function as end-of-line valves. Their installation dimensions are slightly larger compared to wafer types.
III. Classified by Structure
Concentric Butterfly Valves (Zero Offset) position the disc’s rotation center to coincide with the center line of the valve body and the valve stem. This results in a simple structure and low cost. Yet, their sealing performance is generally average, and they experience higher wear.
Single-Eccentric Butterfly Valves feature a valve stem centerline offset from the valve body’s centerline by a certain distance. Ultimately, this improves sealing performance and reduces friction during opening.
Double-Eccentric Butterfly Valves have their valve stem’s centerline offset from the valve body’s centerline, and the disc’s sealing surface is also offset from the valve body’s centerline. This significantly improves sealing performance and extends service life, making them widely used in higher pressure and temperature applications.
Triple-Eccentric Butterfly Valves build upon the double-eccentric design by offsetting the geometric center of the conical sealing surface from the valve stem’s centerline. Consequently, they achieve complete zero-leakage sealing, making them suitable for harsh high-temperature, high-pressure, and highly abrasive conditions.
IV. Classified by Control Method
On-Off Pneumatic Butterfly Valves are used solely for fully opening or fully closing the valve. Therefore, they offer a simple structure and are easy to control.
Regulating Pneumatic Butterfly Valves, conversely, can precisely control the opening angle of the disc by receiving analog signals (e.g., 4-20mA), thereby regulating fluid flow. This allows for high precision and enables precise flow control. You will typically find them in automation systems requiring flow control.
V. Classified by Actuator Type
Double-Acting Pneumatic Actuators utilize compressed air for both opening and closing, requiring air supply to both sides. This design provides high torque and fast action.
Single-Acting Pneumatic Actuators (Spring Return Type) use compressed air for opening and spring force for closing (or vice versa). Crucially, this allows them to automatically return to a safe position in case of air source failure. Thus, they are often used in safety interlock systems.
When selecting the appropriate pneumatic butterfly valve, you must consider various factors. These include media properties, working pressure, temperature, flow requirements, installation space, and cost. Understanding the different classification methods of pneumatic butterfly valves helps you choose the most suitable valve product for your specific needs, ultimately ensuring safe and efficient operation of your production processes.