How Electric Control Valves Improve Fluid Control, System Safety, and Energy Efficiency in Industrial Automation
In industrial automation, precise control of fluid media is vital. It ensures production efficiency, product quality, and system safety. Electric control valves combine actuators with valve bodies, forming a smart and accurate fluid regulation system. These valves act as the “nerve endings” of pipelines and are key nodes in control networks. Their role spans fluid parameter regulation, stable operation, and efficient energy use.
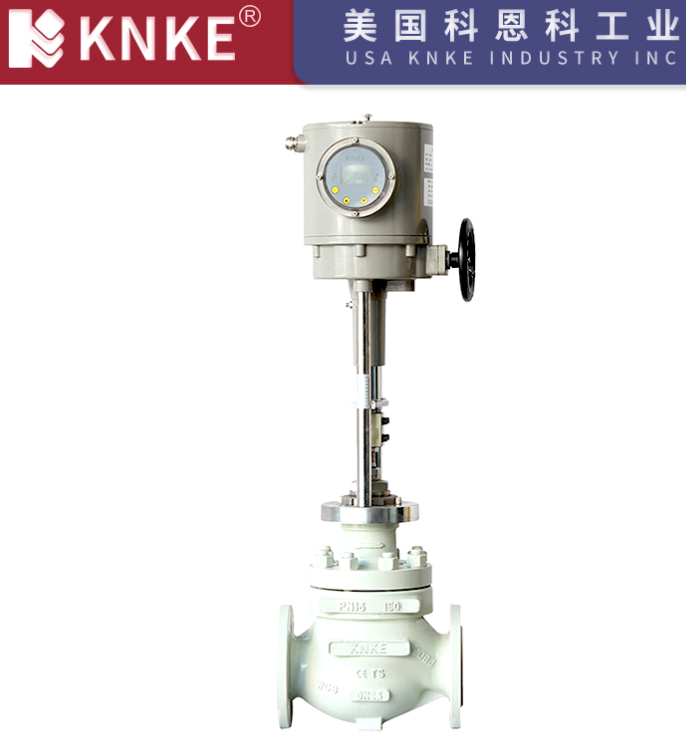
I. Accurate Fluid Control: From Basic Adjustment to Smart Regulation
Electric control valves shine in controlling key fluid parameters. Thanks to their electric actuators, they adjust valve openings linearly from 0% to 100%. This allows precise control of flow, pressure, and temperature.
Flow Control
In flow regulation, the valve adjusts the flow area based on system commands. For example, in a chemical reactor, the valve can control the feed rate within ±1%, ensuring stable reactions.
Pressure Control
Electric valves also stabilize pressure. They monitor real-time signals and adjust automatically. In heating networks, if pressure is too high, the valve closes slightly to prevent damage. In long-distance pipelines, they manage pressure step-by-step, keeping the gradient steady. This “sense–adjust–feedback” loop acts like an intelligent pressure regulator.
Temperature Control
By controlling thermal media like steam or cooling water, electric valves indirectly regulate temperature. In food sterilization, they keep the temperature within ±0.5°C to protect nutrients. In HVAC systems, adjusting chilled water flow keeps room temperature within ±1°C, boosting comfort and saving energy.
II. Ensuring System Stability: From Prevention to Protection
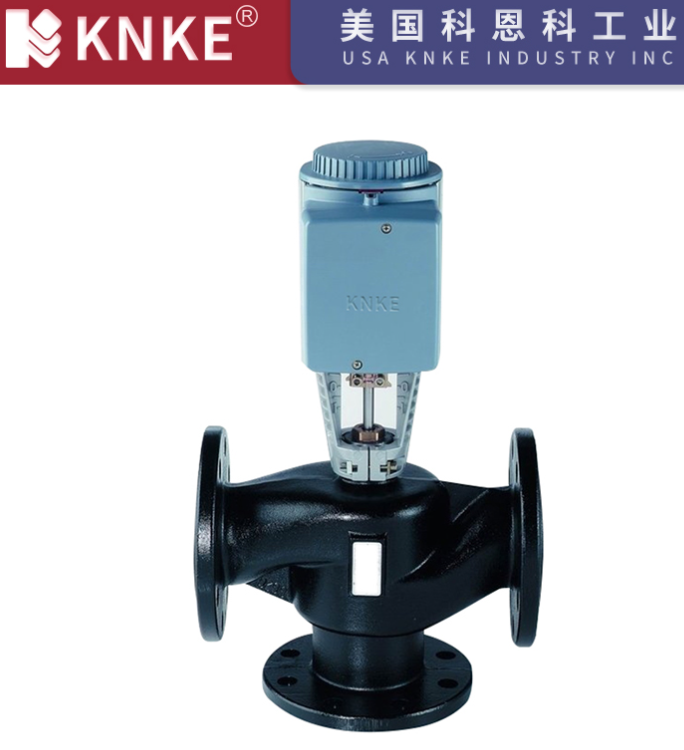
Electric valves serve as “safety guards” in complex industrial setups. Their protective features ensure stable operation even under tough conditions.
Handling High Pressure Differences
Special valve designs—like multi-stage pressure reduction—prevent cavitation. Some models have backup power. If there’s a power failure, the valve resets to a safe position, avoiding uncontrolled flow.
Balancing Flow
In multi-branch systems, valves balance flow across pipelines. In a steel plant, for example, they adjust cooling water based on temperature feedback. This ensures even cooling for blast furnaces and casting machines, avoiding overheating.
Durability in Harsh Environments
Electric valves are built for tough jobs. PTFE linings resist acids and bases in chemical processing. Metal-sealed valves can withstand over 600°C and 25 MPa, making them suitable for nuclear and thermal power systems.
III. Enabling Energy Efficiency: From Demand-Driven Supply to Green Manufacturing
With global carbon goals rising, electric valves are now energy-saving tools.
On-Demand Supply
Paired with sensors and PLCs, valves control media supply based on actual need. In heating, flow adjusts with outdoor temperatures and indoor demand. This avoids “high flow, low temperature difference” waste. Real-world data shows energy savings of 15% to 20%. In compressed air systems, coordinated pressure and flow control cuts compressor energy use by over 10%.
Protecting Equipment
Traditional valves often cause “water hammer,” stressing pumps and motors. Electric valves offer soft-start and soft-close (5–60 seconds), smoothing flow and reducing current surges. For instance, a paper mill reported 30% fewer pump failures and saved $34,722 annually on maintenance after switching to electric valves.
Environmental Benefits
Electric valves help meet emission targets. In wastewater treatment, they adjust chemical dosing based on water quality. This ensures clean output while reducing chemical use. In coal plants, they regulate desulfurization fluids, keeping SO₂ and NOₓ emissions 20% below national limits.
IV. Embracing Industrial Intelligence: From Automation to Digital Transformation
Industry 4.0 and IoT have pushed electric valves into the digital age.
Smart Monitoring
Modern valves include sensors and communication modules. They send real-time data like valve position and torque to the cloud or control center. This enables remote monitoring and predictive maintenance. When a torque spike appears, the system issues an alert. Maintenance teams can respond early, avoiding costly downtime. A petrochemical firm saw unplanned outages fall by 40% with this setup.
AI and Big Data Optimization
AI and machine learning take valve performance even further. Models based on historical data predict the best control strategies. In urban water systems, smart valves adjust pressure ahead of time using weather and usage patterns. This improves supply reliability and reduces leaks. In pharmaceutical production, AI valves control microflows under 0.1 L/min—meeting the industry’s strictest process needs.
Electric control valves are more than just flow devices. They protect safety, boost energy efficiency, and withstand extreme conditions. Most importantly, they connect physical systems with intelligent control. As industries move toward smart, green manufacturing, these valves will be essential to progress. Each precise movement in the pipeline plays a part in the rhythm of modern industrial intelligence.