Methods to Improve the Accuracy of Gas Turbine Flow Meters
Gas turbine flow meters are widely used in natural gas trade and custody transfer due to their high sensitivity, excellent repeatability, wide turndown ratio, and high accuracy. As the urban gas infrastructure continues to expand and metering requirements become more stringent, gas turbine flow meters are becoming essential tools in gas commercial transactions and transfer metering in cities across China.
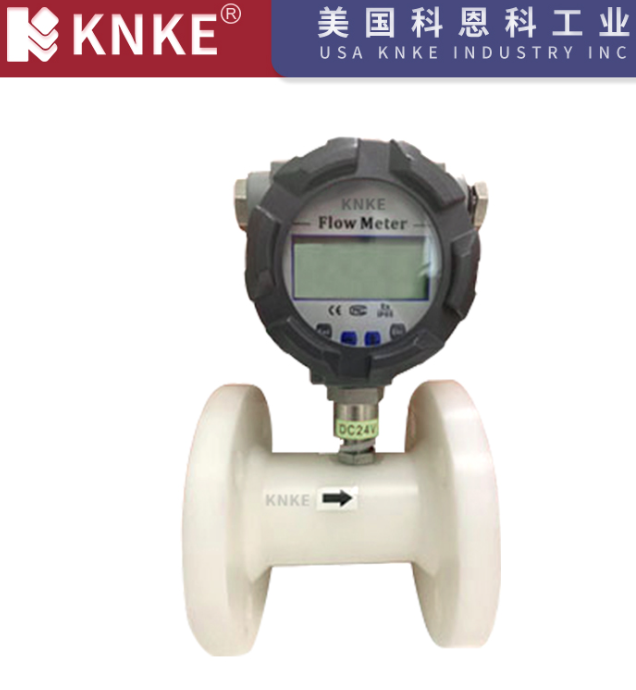
1. Select the Right Model and Installation Location
Because gas turbine flow meters rely on the rotational inertia of the turbine to measure flow, they are not ideal for systems with rapidly fluctuating gas flow rates. In such cases, delayed turbine response may lead to measurement errors. To avoid this, it’s important to accurately estimate the peak and valley values of gas consumption and operating pressure, and then select a flow meter with appropriate specifications.
In addition, the installation location should be carefully chosen. The flow meter should be installed in a section of the pipeline where the gas flow is stable and free from turbulence caused by nearby elbows, valves, or reducers.
2. Install High-Performance Filters and Clean Regularly
Gas turbine flow meters contain moving parts like bearings and rotors that are sensitive to impurities. To ensure reliable operation and minimize wear, a high-efficiency gas filter must be installed upstream of the flow meter.
It is recommended to equip the filter with a differential pressure gauge to monitor blockage. If the pressure difference exceeds the threshold, the filter must be cleaned promptly. In systems without differential pressure monitoring, a monthly cleaning schedule is advisable to maintain optimal flow conditions.
3. Maintain Proper Straight Pipe Lengths
To ensure accurate readings, it is critical to meet the required straight pipe lengths before and after the flow meter. Generally, a minimum of 10 pipe diameters upstream and 5 diameters downstream is required. Inadequate straight lengths or partially open valves upstream can distort the flow profile and reduce measurement accuracy.
When installing, ensure that gaskets do not protrude into the pipe and that the flow meter is properly aligned with the pipeline to avoid installation stress and angular misalignment.
4. Regular Maintenance and Calibration
The rotor and bearings of turbine flow meters are subject to wear over time, especially in high-flow or contaminated environments. Routine maintenance is necessary to check for mechanical wear and replace damaged components.
Additionally, periodic calibration is essential to maintain accuracy. Establishing a regular calibration schedule helps ensure that the meter retains its original accuracy, especially in custody transfer applications.
5. Choose Reliable and Proven Brands
Not all turbine flow meters are created equal. Choosing a reputable manufacturer with reliable technology, quality assurance, and strong after-sales support—such as Huikeda Flow Meters—ensures better performance, durability, and accuracy in the long term.
Frequently Asked Questions (FAQ)
Q1: Why is a filter necessary before a gas turbine flow meter?
A: The filter prevents solid particles and impurities from damaging sensitive internal parts like the rotor and bearings, which are critical to measurement accuracy.
Q2: How often should I calibrate a gas turbine flow meter?
A: Calibration frequency depends on usage and regulatory requirements, but generally, an annual calibration is recommended for custody transfer applications.
Q3: Can gas turbine flow meters be used in systems with pulsating flow?
A: They are not ideal for highly pulsating flows due to rotor inertia. In such cases, alternative flow measurement technologies or damping techniques should be considered.
Q4: What is the typical accuracy of a gas turbine flow meter?
A: Most models offer accuracy classes of ±1.0% or ±1.5%, depending on the application and calibration status.
Q5: What causes turbine flow meter errors?
A: Common causes include incorrect sizing, improper installation, dirty or blocked filters, rotor wear, and insufficient straight pipe runs.