Electromagnetic Flow Meters: Comprehensive Operation Guide & FAQ
Electromagnetic flow meters, utilizing Faraday’s law of electromagnetic induction, measure the volumetric flow rate of conductive liquids. These meters are extensively applied across various sectors, including petrochemical, water treatment, food and beverage production, pharmaceutical, and scientific research, thanks to their high precision and reliability in challenging fluid conditions. This guide systematically details the operation steps to help engineers and researchers optimize the performance and lifespan of electromagnetic flow meters.
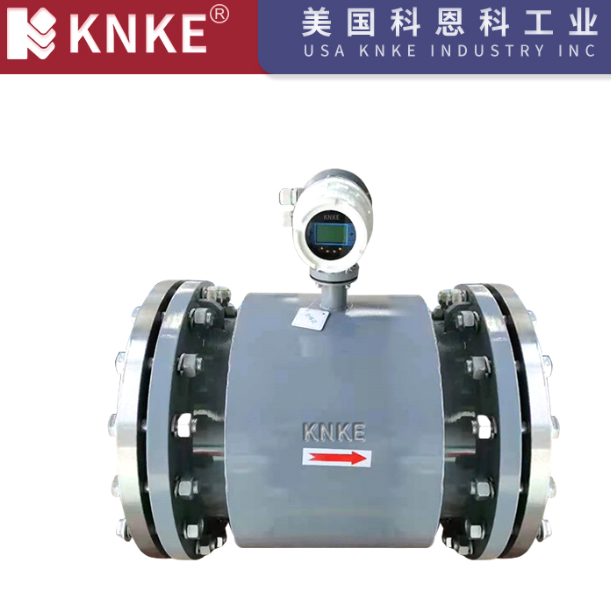
Technical Checks Before System Start-Up
Before initiating operations, comprehensive electrical connections and grounding system inspections should be conducted according to the manufacturer’s manual and national standards, ensuring compliance with electromagnetic compatibility (EMC) and explosion-proof requirements. Additionally, verify the human-machine interface (HMI) display and confirm that preset parameters—such as flow units, measurement range, excitation frequency, and signal output mode—align with actual operating conditions. Accurate parameter settings are essential to preventing measurement deviations and ensuring precise instrument functionality.
Calibration Procedures for Electromagnetic Flow Meters
Calibration is crucial for newly installed or recently serviced electromagnetic flow meters. Standard calibration methods include online real-flow calibration, suitable for actual site conditions, and offline simulated signal calibration using standard sources (such as 4~20mA signals) to validate linear responses, hysteresis, and repeatability. Calibration accuracy should be maintained within ±0.5%, with important measurement scenarios recommended for authoritative third-party calibration.
Real-Time Monitoring and Operational Data Analysis
Integration with Distributed Control Systems (DCS) or Supervisory Control and Data Acquisition (SCADA) systems enables electromagnetic flow meters to collect real-time data, including instantaneous flow rate, cumulative flow, electrode signals, and excitation parameters. Utilizing analytical methods such as moving averages, anomaly detection, and Fast Fourier Transform (FFT) frequency domain analysis effectively identifies zero-point drift, signal distortion, or systematic interference. Address detected abnormalities promptly by inspecting potential issues like electrode fouling, pipe emptiness, or bubble disturbances, supported by sensor diagnostics or simulation tools for verification.
Maintenance and Upkeep Strategies
To ensure sustained operational stability of electromagnetic flow meters, implement the following maintenance strategies:
- Schedule regular electrode and liner cleaning cycles based on fluid characteristics to prevent deposits or corrosion.
- Periodically inspect seals, flanges, and bolt tightness to prevent minor leaks.
- Utilize built-in instrument self-check features or maintenance software to regularly verify parameters and perform firmware updates.
- Provide protective housings, anti-vibration mounts, or signal isolators in harsh environments to prevent physical damage and external disturbances.
Electromagnetic flow meters’ simplicity, adaptability, and lack of pressure loss make them ideal for conductive fluid measurement. Effective installation, regular maintenance, and advanced data analytics are critical for ensuring stable performance. Establishing an ISO-standardized operation and maintenance system significantly extends equipment lifespan, enhances industrial process reliability, and improves measurement accuracy, contributing to intelligent manufacturing and industrial digitalization goals.
FAQs about Electromagnetic Flow Meters
1. What is an electromagnetic flow meter, and how does it work?
An electromagnetic flow meter measures the volumetric flow rate of conductive liquids using Faraday’s law of electromagnetic induction. It calculates flow based on the voltage induced as fluid moves through a magnetic field.
2. What industries commonly use electromagnetic flow meters?
Electromagnetic flow meters are widely used in industries such as petrochemicals, water treatment, food and beverage production, pharmaceuticals, and scientific research.
3. Why is calibration important for electromagnetic flow meters?
Calibration ensures measurement accuracy by verifying the meter’s response to flow conditions. It minimizes errors from installation or component wear, typically within ±0.5% accuracy.
4. How often should an electromagnetic flow meter be calibrated?
Calibration frequency depends on the application and manufacturer guidelines. Typically, annual calibration is recommended, with additional checks after maintenance or significant operational changes.
5. What common issues can affect electromagnetic flow meter accuracy?
Common issues include electrode fouling, air bubbles, empty pipe conditions, improper grounding, signal interference, and incorrect installation or parameter settings.