Factors Affecting the Measurement Accuracy of Coriolis Mass Flow Meters
Coriolis mass flow meters are widely used in modern industrial production due to their direct measurement of mass flow, fast response, and high accuracy. However, various factors can affect the measurement accuracy in real-world conditions. This article explores the main factors influencing the accuracy of Coriolis mass flow meters, including fluid characteristics, installation conditions, environmental factors, and inherent instrument issues. Suggestions for mitigating these factors are also provided.
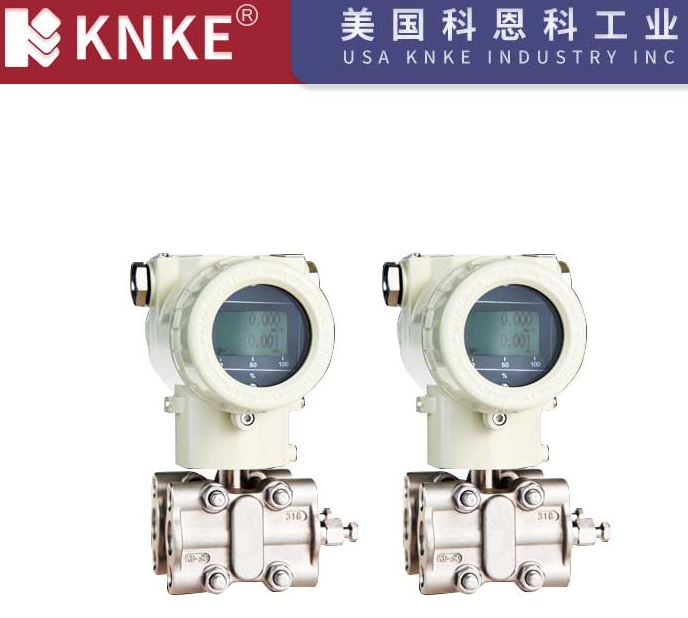
1. Fluid Characteristics
- Density Variation
Although Coriolis mass flow meters theoretically are not affected by fluid density, significant density changes, especially those exceeding the instrument’s design compensation range, can alter the sensor’s response characteristics, leading to measurement inaccuracies. For example, in chemical processes where reaction products cause sudden changes in fluid density, measurement errors may increase. - Viscosity Variation
High-viscosity fluids can alter the vibration modes of the measurement tube, affecting the transfer and detection of Coriolis forces. Additionally, viscosity changes may lead to uneven fluid distribution inside the pipe, further affecting accuracy. This issue is particularly notable when transporting heavy oils or viscous materials. - Presence of Gas or Solids
- Gas: The presence of gas in the fluid can change the mass distribution and elasticity of the measurement tube, altering its vibration mode and causing fluctuations in readings.
- Solids: Solid particles may wear down the inner wall of the measurement tube or accumulate inside, affecting the vibration frequency and amplitude, thus lowering measurement accuracy. Applications such as wastewater treatment or slurry transport often face such issues.
2. Installation Conditions
- Pipeline Vibration
External vibrations from nearby machinery or equipment can interfere with the vibration of the measurement tube, leading to signal deviations. If the frequency of external vibrations is close to the natural vibration frequency of the tube, resonance can occur, significantly affecting measurement accuracy. This is a common concern when installing mass flow meters near large mechanical devices or compressors. - Installation Location
Improper installation locations, such as near pumps or valves that cause fluid turbulence, can lead to unstable flow conditions before the fluid enters the measurement tube, resulting in measurement errors. It is recommended to install the meter in a straight section of the pipe, at least 10 times the pipe diameter upstream and 5 times downstream, while ensuring the tube is aligned horizontally or vertically. - Pipeline Stress
Stress generated during pipeline installation can be transmitted to the mass flow meter, changing the shape and vibration characteristics of the measurement tube, which affects measurement accuracy. This can occur due to thermal expansion or improper fixation of the pipeline. Using proper supports and expansion joints can minimize this effect.
3. Environmental Factors
- Temperature Variation
Changes in environmental temperature can affect the material properties of the measurement tube, such as its elastic modulus and thermal expansion coefficient, leading to changes in vibration frequency and amplitude. Temperature fluctuations can also cause electronic components to drift, affecting accuracy. For installations in extreme temperatures, it is important to use instruments designed for wide temperature ranges and to provide insulation or heat dissipation as needed. - Electromagnetic Interference
Nearby electromagnetic sources, such as motors, transformers, and variable frequency drives, can interfere with the sensor’s signal transmission and processing, leading to inaccurate measurements. To mitigate this, shielded cables, grounding, and filters should be used to suppress electromagnetic interference. - Humidity Impact
High humidity can cause moisture to accumulate on electronic components, leading to reduced insulation and potential short-circuits. In humid environments, such as underground pipelines or coastal areas, it is crucial to use protective enclosures, desiccants, and ensure the integrity of seals to prevent moisture ingress.
4. Instrumental Factors
- Sensor Aging
Over time, the elastic components of the measurement tube in a Coriolis flow meter can undergo fatigue, reducing sensitivity and response characteristics, leading to decreased measurement accuracy. Regular performance verification and calibration are necessary to ensure reliable readings. - Zero Drift
Zero drift occurs when the instrument does not register zero when the fluid is static. This can introduce bias into measurements. Regular zero calibration or online auto-zeroing functions can help eliminate this issue. - Improper Instrument Selection
Selecting a mass flow meter with an inappropriate flow range for the application can significantly affect accuracy. If the flow rate is too close to the meter’s range limits, accuracy will decrease. For example, using a meter with too large a range for small flow rates increases relative error. It is essential to choose an instrument with an appropriate flow range, typically 1.2 to 1.5 times the maximum expected flow rate.
Numerous factors can affect the accuracy of Coriolis mass flow meters, including fluid properties, installation conditions, environmental influences, and inherent instrument issues. To achieve reliable and stable measurements, it is essential to consider these factors during the selection phase and take appropriate measures during installation and maintenance. Regular calibration, proper installation, and the use of shielding or insulation techniques can significantly mitigate these factors, ensuring the high accuracy and efficiency of the measurement process.