Features of Low-Temperature Gate Valves: An Engineer’s Perspective
Low-temperature gate valves play a critical role in industries such as petrochemical, LNG processing, and cryogenic gas transport. From an engineering standpoint, understanding their unique characteristics helps ensure reliable performance under extreme conditions. Below, we explore five core features that set low-temperature gate valves apart.
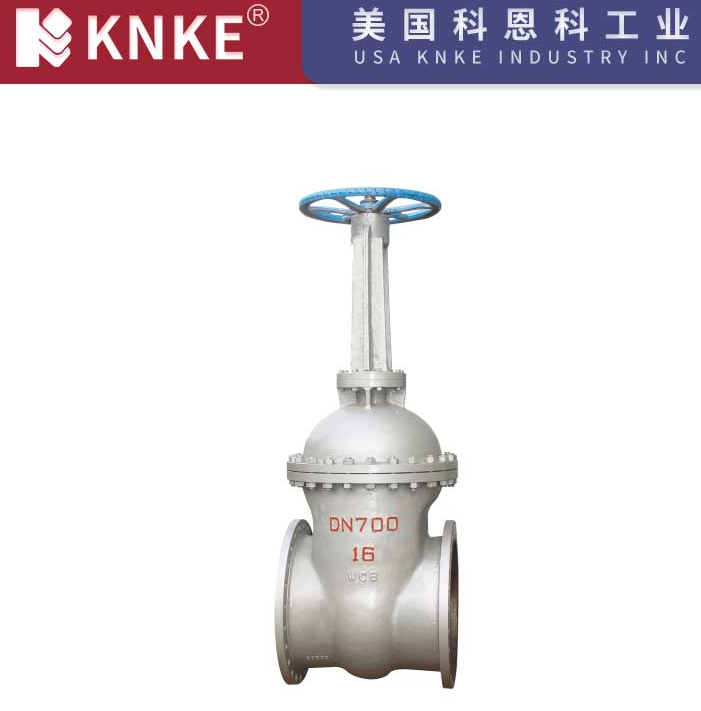
1. Lightweight Construction
By utilizing high-grade ductile iron for the valve body, low-temperature gate valves are approximately 20–30% lighter than traditional designs. This weight reduction simplifies handling, installation, and maintenance, ultimately cutting labor costs and downtime.
2. Flat‑Seat Design
Traditional gate valves often trap debris—such as sediment, scale, or foreign particles—in the recessed seat area, which can lead to leakage and wear. The flat‑seat configuration eliminates this pocket, ensuring that solids cannot accumulate. As a result, fluid flow remains unobstructed, and sealing integrity is maintained even after frequent flushing or cleaning cycles.
3. Full Rubber Encapsulation
The gate and sealing surfaces feature a continuous inner and outer rubber coating, applied through advanced European vulcanization techniques. This full encapsulation bonds the rubber reliably to the metal substrate, providing excellent elasticity and “memory” after repeated cycles. The rubber layer also offers superior corrosion resistance, protecting the valve from aggressive media at low temperatures.
4. Minimal Flow Resistance
Optimized internal contours and smooth sealing surfaces minimize turbulence and pressure drop across the valve. Reduced flow resistance not only improves system efficiency but also decreases erosive wear on the sealing faces. This feature is particularly valuable in cryogenic systems, where even small pressure losses can impact overall energy consumption.
5. Precision‑Cast Body
Employing precision casting technology guarantees tight dimensional tolerances without the need for extensive machining. Accurate geometry directly translates to better sealing performance and consistent operation under high differential pressures and subzero temperatures. Precision casting also streamlines manufacturing and lowers production costs.
FAQ
Q1: What applications are best suited for low-temperature gate valves?
Low-temperature gate valves excel in cryogenic processes, including LNG and LPG transport, industrial gas distribution, and any system requiring reliable shut-off at temperatures down to –196 °C.
Q2: How does the flat-seat design prevent debris buildup?
The flat-seat eliminates recessed cavities where particles can collect. Any solids in the fluid stay suspended or pass through, avoiding seat damage and leakage.
Q3: What materials are used for rubber encapsulation?
High-quality elastomers—often EPDM or specially formulated nitrile rubbers—are vulcanized onto the gate. These materials remain flexible and maintain sealing integrity at ultra-low temperatures.
Q4: How should low-temperature gate valves be maintained?
Regular inspection of the rubber coating and seating surfaces is recommended. Gentle cleaning with compatible solvents helps remove any deposits without harming the encapsulation.
Q5: Can these valves handle high-pressure differences?
Yes, the combination of precision casting and robust materials allows low-temperature gate valves to operate under significant pressure differentials while preserving a tight seal.