Turbine Flow Meter: Key Maintenance Tips for Optimal Performance
Turbine flow meters are widely used in industrial applications for measuring liquid and gas flow. To ensure their long-term stability and accuracy, proper daily maintenance is essential. Below are key maintenance tips to keep your turbine flow meter performing at its best.
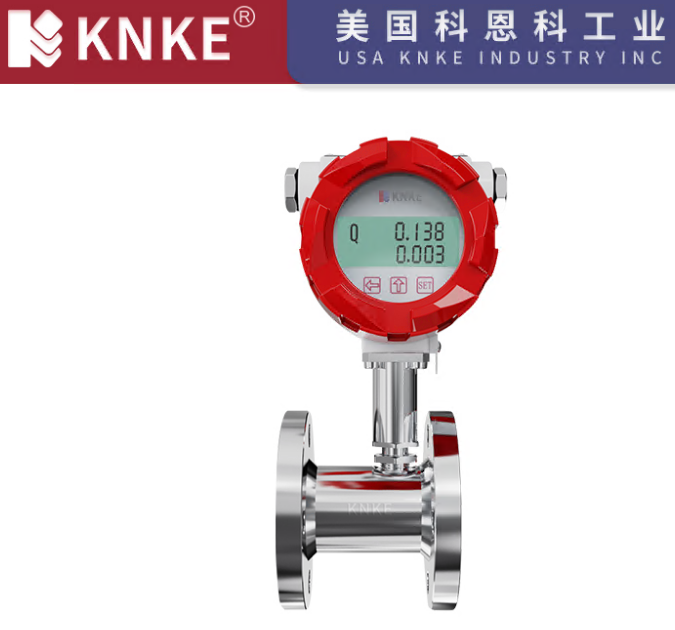
1. Pre-Installation Checks
Before installing a turbine flow meter, ensure that the sensor is used according to the specifications on the certificate of conformity. Pay attention to the following:
- Flow Range: Always use the flow meter within its rated flow range to avoid damaging the sensor.
- Nominal Pressure: Verify that the operating pressure matches the design specifications.
- Flow Direction: Ensure that the flow meter is installed according to the indicated flow direction to prevent errors in measurement.
2. Environmental and Fluid Requirements
The environmental conditions and the properties of the fluid being measured are crucial for accurate readings. Follow these guidelines:
- Fluid Temperature: Ensure that the temperature of the fluid being measured falls within the range specified in the user manual to prevent performance issues.
- Environmental Conditions: The operating environment should meet the flow meter’s specifications to avoid malfunction due to environmental factors.
3. Flow Accumulator Operation
Proper operation of the flow accumulator is key to obtaining accurate flow measurements:
- Power Supply: Ensure that the flow accumulator is connected to a stable power source.
- Zero Flow Check: When the downstream valve is closed, the flow accumulator should display a flow reading of zero, indicating that no flow is occurring.
4. Initial Use of the Turbine Flow Meter
Follow the correct startup procedure when putting the turbine flow meter into operation:
- Bypass Valve Operation: Begin by opening all bypass valves to ensure smooth flow through the system.
- Valve Operation: Gradually open the downstream valve, then the upstream valve to its fully open position. Slowly close the bypass valves to ensure the rotor does not reach high speeds abruptly.
- Without Bypass Valves: If no bypass valve is available, open the upstream valve slowly and then open the downstream valve gradually.
5. Measurement of Liquefied Gases and Gasoline
When measuring fluids like liquefied gases or gasoline, extra precautions are needed:
- Pressure Requirement: Ensure that the pressure in the flow meter is at least 0.1 MPa higher than the vapor pressure of the liquid to prevent vaporization. Vaporization can cause the rotor speed to increase too quickly, leading to excessive wear on the bearings.
6. Routine Inspection and Calibration
To maintain accurate readings, routine inspection and recalibration of the turbine flow meter are essential:
- Inspection Frequency: It is recommended to inspect and calibrate the flow meter every six months to one year, depending on the operating conditions. The frequency may vary based on the severity of work conditions.
- Wear and Tear: If excessive wear is found on the shaft or bearings, replace them promptly and recalibrate the flow meter to ensure continued accurate operation.
FAQ – Frequently Asked Questions
1. How often should I calibrate my turbine flow meter?
It is recommended to calibrate your turbine flow meter every 6 months to a year. The exact frequency depends on the harshness of the working environment and the conditions under which it operates.
2. What should I do if the turbine flow meter displays incorrect readings?
If you notice incorrect readings, check the system for leaks, blockages, or valve malfunctions. Additionally, verify that the meter is installed in the correct flow direction and ensure all operational parameters are within the manufacturer’s specifications.
3. Can I use the turbine flow meter for all types of fluids?
Turbine flow meters are most accurate for clean, low-viscosity liquids and gases. They may not perform well with highly viscous fluids or those containing solid particles, which could cause mechanical damage.
4. What are the signs that the turbine flow meter needs maintenance?
If the flow meter is showing inaccurate readings, operating inconsistently, or if the rotor speed is erratic, these may be signs that maintenance or calibration is needed.
5. What should I do if I encounter high-speed rotor issues?
High rotor speeds can occur if the fluid being measured is close to or above its vapor pressure. In such cases, ensure that the pressure is higher than the fluid’s vapor pressure by at least 0.1 MPa to prevent damage.
By following these maintenance tips and performing routine checks, you can extend the life of your turbine flow meter, ensuring reliable performance for years to come.
Thanks for highlighting the importance of daily maintenance. I’d be curious to know if there are specific indicators to watch for that suggest a turbine flow meter might be drifting out of calibration.