Valve Pickling and Passivation Methods
Pickling and passivation are essential processes in valve production. These steps remove impurities and enhance corrosion resistance, extending the valve’s lifespan. This article explains common pickling and passivation methods for austenitic stainless steel valves.
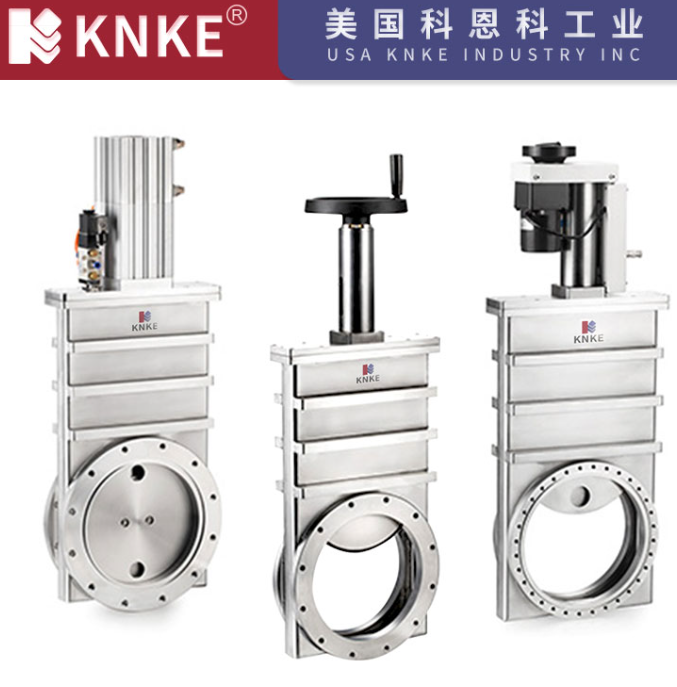
1. Valve Pickling Process
Pickling removes oxides and contaminants from the surface of metals. For austenitic stainless steel valves, a mixture of hydrochloric acid (HCl) and nitric acid (HNO3) is commonly used. The solution typically contains 6%–8% HCl, 20%–30% HNO3, and 6%–7% cyanofluoride acid.
- Procedure: Immerse the valve in the pickling solution for 5–10 minutes. This effectively removes the oxide layer and impurities, creating a smooth surface for passivation.
- Precautions: Because the solution is corrosive, handle it carefully. Wear protective equipment, and ensure the workspace is well-ventilated. Control the concentration and immersion time to prevent excessive corrosion.
2. Valve Passivation Process
Passivation creates a protective layer on the metal surface, improving corrosion resistance. For austenitic stainless steel, passivation typically involves immersing the valve in a nitric acid solution (60%–70%).
- Procedure: Immerse the valve in concentrated nitric acid for 30–40 minutes. The process forms a dense passive film that enhances corrosion resistance. After passivation, clean the valve thoroughly.
- Passivation Enhancement Treatment: Some processes use a mixture of 7%–10% sulfuric acid and 2%–4% ammonium chloride (NAct) for a secondary immersion. After 7–10 minutes, rinse the valve with clean water.
3. Combined Pickling and Passivation Process
Pickling and passivation are often done together. First, pickling removes surface impurities, then passivation forms a protective film. Only after completing both steps does the valve achieve maximum corrosion resistance and optimal performance.
4. Conclusion
Pickling and passivation significantly improve the corrosion resistance and longevity of valves, especially those made of austenitic stainless steel. By using the correct pickling and passivation solutions and controlling immersion time, manufacturers can ensure high-quality valves.
Operators should follow safety guidelines when handling these chemicals. Proper cleaning and post-treatment are also crucial to guarantee the final quality of the valve.
Frequently Asked Questions (FAQs)
Q1: What is the difference between pickling and passivation?
A1: Pickling removes contaminants and oxides from the metal surface, while passivation forms a protective oxide layer to enhance corrosion resistance.
Q2: Why is nitric acid used in the passivation process?
A2: Nitric acid forms a passive oxide film on the metal, which greatly improves its corrosion resistance.
Q3: How long should a valve be immersed in the pickling solution?
A3: Immersion should last 5–10 minutes, which is sufficient to remove contaminants without causing excessive corrosion.
Q4: Can pickling and passivation be done together?
A4: Yes, both processes are often performed in sequence. Pickling cleans the surface, and passivation enhances corrosion resistance.
Q5: Are there safety concerns during pickling and passivation?
A5: Yes, both processes involve corrosive chemicals. Always wear protective gear and ensure proper ventilation in the work area.