Advantages of Diaphragm Valves: Benefits, Features, and FAQ
Diaphragm valves are widely recognized for their robust design and reliability in various industrial applications. With their simple construction, exceptional sealing capabilities, and corrosion resistance, they have become indispensable in industries such as chemical processing, pharmaceuticals, food production, and nuclear applications. This article outlines the key advantages of diaphragm valves and provides a comprehensive FAQ section to address common queries.
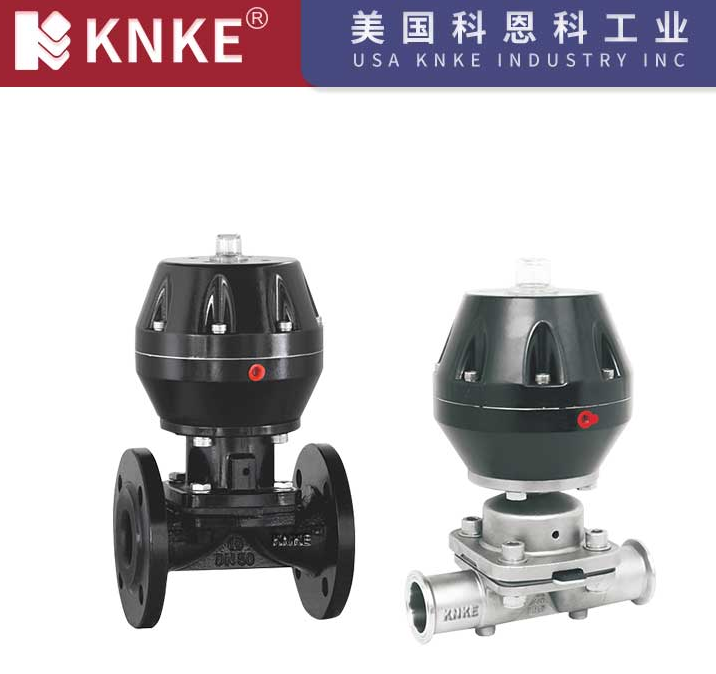
Key Advantages of Diaphragm Valves
1. Simple Structure and Fewer Components
Diaphragm valves are composed of just three main parts: the valve body, diaphragm, and valve cover. Their uncomplicated design reduces production costs and simplifies maintenance, making them a cost-effective and efficient solution for controlling fluid flow.
2. Easy Disassembly and Maintenance
The most commonly damaged part of a diaphragm valve is the diaphragm itself. When replacement is needed, there is no requirement to remove the entire valve from the pipeline. Simply removing the valve cover allows for quick on-site replacement, minimizing downtime and improving operational efficiency.
3. Superior Sealing Performance
Manufactured with soft materials such as rubber or plastic, the diaphragm offers excellent sealing capabilities. This design ensures that there is no leakage at the connection between the valve body and the valve cover, allowing for complete isolation between upstream and downstream sections, which enhances system safety and reliability.
4. No Dead Zones in the Valve Body
The streamlined, smooth internal flow path of diaphragm valves prevents the accumulation of fluids. This design minimizes the risk of residue build-up, mold growth, or product degradation, and ensures that even fluids containing fibers or particles flow without causing blockages.
5. Packing-Free Design
Unlike traditional valves that require packing materials to seal the valve stem, diaphragm valves utilize a packing-free structure. The diaphragm effectively separates the lower valve body from the upper valve cover, eliminating the need for packing and thereby reducing the risk of corrosion while increasing durability.
6. Versatile Applications
Diaphragm valves are not only ideal for completely shutting off flow but also excel in throttling applications. Their versatility makes them suitable for a wide range of processes where precise flow control is critical, from industrial chemical processing to food and pharmaceutical production.
7. Excellent Corrosion Resistance
Thanks to the variety of liner materials available, diaphragm valves exhibit outstanding resistance to corrosive chemicals. This feature makes them particularly effective in handling aggressive media such as acids and alkalis, thereby extending the lifespan of the valve and ensuring consistent performance in harsh environments.
8. Suitable for Various Operating Conditions
Diaphragm valves are especially favored in applications involving hazardous chemicals and radioactive fluids. Their design minimizes the risk of contamination, making them ideal for industries where product purity is paramount. They are widely used in environments that require stringent contamination controls, such as pharmaceutical, food processing, and nuclear industries.
Frequently Asked Questions (FAQ)
Q1: What industries commonly use diaphragm valves?
A: Diaphragm valves are widely used in the chemical, pharmaceutical, food processing, and nuclear industries due to their excellent sealing properties and resistance to corrosive media.
Q2: How does the maintenance of a diaphragm valve compare to traditional valves?
A: Diaphragm valves are easier to maintain since only the diaphragm typically needs to be replaced. This can often be done on-site without removing the entire valve, reducing downtime.
Q3: Can diaphragm valves handle particulate matter?
A: Yes, the streamlined internal design of diaphragm valves prevents the accumulation of particulates, ensuring that fibers or particles do not block the flow.
Q4: What makes diaphragm valves particularly suitable for hazardous fluids?
A: Their packing-free design and superior sealing capabilities ensure that there is no leakage or contamination, making them ideal for handling dangerous chemicals and radioactive fluids.
Q5: Are diaphragm valves cost-effective?
A: Yes, their simple structure, reduced number of parts, and low maintenance requirements contribute to overall cost-effectiveness in various industrial applications.
Diaphragm valves offer significant advantages including simplicity, ease of maintenance, superior sealing performance, and versatility across multiple industrial applications. Their excellent corrosion resistance and ability to handle hazardous fluids make them a preferred choice in critical sectors where safety and product purity are essential. By understanding these benefits and addressing common concerns through our FAQ section, users can make informed decisions when selecting diaphragm valves for their processes.