Installation Requirements for Small Flow Gear Flow Meters
Small flow gear flow meters provide high-precision measurements for volumetric flow. These meters, based on positive displacement, use fluid movement to rotate gears. The rotation, detected through non-contact scanning, ensures accurate flow measurement. To achieve optimal performance and extend the lifespan of the device, it is crucial to install the meter correctly. Below are the key installation requirements for small flow gear flow meters.
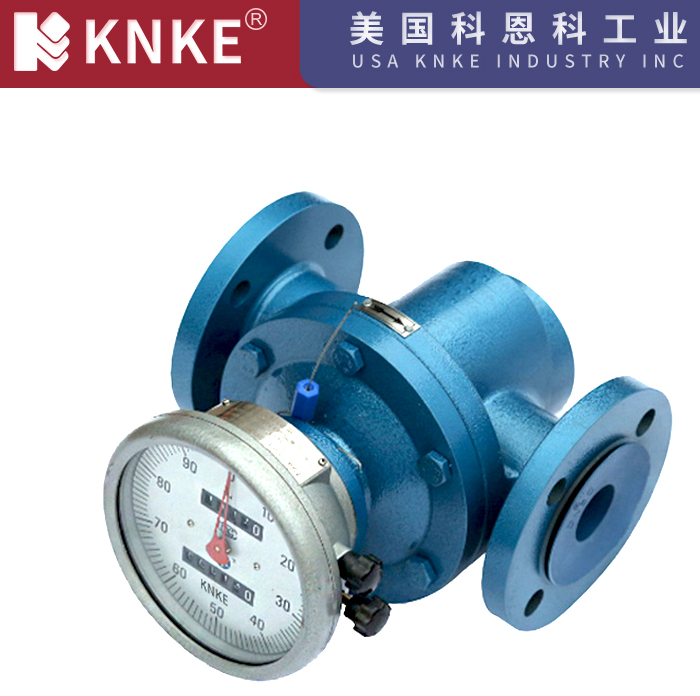
1. Choose the Right Installation Location
- Minimize Vibrations
Vibrations can disrupt the gears and lead to measurement inaccuracies. For this reason, you should place the flow meter in a location with minimal vibrations. - Avoid Magnetic Interference
Since the meter operates based on magnetic induction, installing it away from strong magnetic fields prevents signal interference. - Align with the Flow Direction
Always ensure the meter’s installation direction matches the flow direction indicated on the device.
2. Ensure Proper Pipeline Connections
- Keep Pipelines Clean
A clean pipeline prevents debris from damaging the gears or bearings. To avoid issues, you can install a filter upstream of the flow meter. - Maintain Adequate Inlet Pressure
Insufficient pressure at the inlet may allow air bubbles to form in the medium, which reduces accuracy. - Provide Adequate Straight Pipe Lengths
To stabilize flow, the pipeline should include straight sections. Typically, you need 10 times the pipe diameter upstream and 5 times downstream.
3. Follow the Correct Installation Angle
- Horizontal or Vertical Orientation
You can install the flow meter horizontally or vertically, but the medium must completely fill the meter. For vertical installations, ensure the flow moves upward. - Avoid Inclined Positions
An inclined setup can cause uneven gear operation, which may lead to measurement errors.
4. Set Up Electrical Connections Accurately
- Connect Sensors Properly
Properly connecting the electromagnetic sensor wires prevents incorrect readings or loose connections. - Ensure Effective Grounding
Grounding the flow meter’s housing eliminates static interference and ensures safety. - Use Shielded Cables
Shielded signal cables minimize electromagnetic interference, especially in environments with strong electrical activity.
5. Test and Calibrate for Accuracy
- Perform a Post-Installation Check
Check for loose components and ensure no leaks occur at the pipeline connections after installation. - Run a No-Load Test
Before introducing fluid, confirm the gears rotate freely without obstruction during a no-load test. - Calibrate After Installation
Calibrating the flow meter ensures accurate measurements. Additionally, recalibrate the device if it has been unused for an extended period.
6. Account for Environmental and Operational Factors
- Stay Within Temperature Limits
To prevent damage, the flow meter must operate within its specified temperature range. - Monitor Medium Characteristics
These meters work best with liquid media. Avoid using them for fluids containing large amounts of air bubbles or solid particles. - Schedule Regular Maintenance
Regular cleaning of gears and bearings prevents dirt buildup, ensuring smooth operation and extending the meter’s lifespan.
To achieve precise measurements and maintain long-term operational stability, install small flow gear flow meters correctly. Choosing the right location, ensuring proper connections, and following calibration protocols are vital steps. Additionally, regular maintenance enhances reliability and efficiency, making your system perform at its best.