Common Solenoid Valve Faults and Solutions
Solenoid valves are essential components used to control the flow of fluids in various industrial automation systems. Due to the complexity of working environments and frequent switching operations, solenoid valves are prone to certain faults. Understanding these faults and their solutions is crucial for extending the lifespan of solenoid valves and ensuring the proper functioning of the equipment. This article will explore common solenoid valve faults and their solutions, helping you diagnose and maintain solenoid valves more effectively.
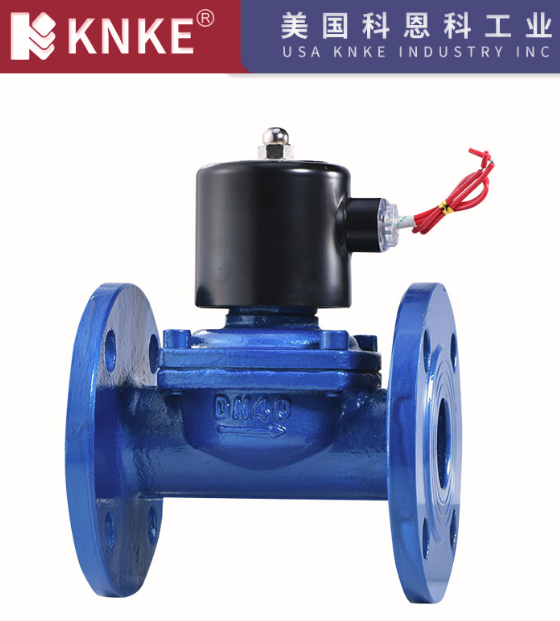
1. Solenoid Valve Does Not Work After Powering On
If the solenoid valve does not respond after being powered on, check the following possible causes:
- Poor Power Wiring
- Solution: Inspect the power wiring for loose connections or breaks. Reconnect the wires and ensure that the connectors are securely attached.
- Power Supply Voltage Outside the Operating Range
- Solution: Verify that the power supply voltage is within the specified operating range (±). If the voltage is outside the range, adjust it to the correct level.
- Coil Detachment
- Solution: Check if the solenoid valve coil has become detached. If so, re-solder the connections.
- Short-Circuited Coil
- Solution: If the coil is short-circuited, replace it with a new one.
- Improper Differential Pressure
- Solution: Check the differential pressure of the valve. If it is not within the correct range, adjust it or replace the solenoid valve with a more suitable model.
- Excessive Fluid Temperature
- Solution: If the fluid temperature is too high, replace the solenoid valve with one rated for higher temperature applications.
- Debris Causing Valve Sticking
- Solution: Clean the solenoid valve. If the seals are damaged, replace them and install a filter to prevent future debris entry.
- Excessive Fluid Viscosity or High Frequency of Use
- Solution: Replace the valve with one suited for high-viscosity fluids or higher-frequency operation.
2. Solenoid Valve Fails to Close
If the solenoid valve fails to close, it may be due to the following reasons:
- Damaged Seals on Main Valve Core or Iron Core
- Solution: Replace the damaged seals.
- Excessive Fluid Temperature or Viscosity
- Solution: Check the temperature and viscosity of the fluid. If either is too high, replace the solenoid valve with one that is compatible.
- Debris in the Valve Core or Iron Core
- Solution: Disassemble and clean the solenoid valve to remove debris.
- Spring Life Expired or Deformed
- Solution: Replace the spring.
- Clogged Throttle or Balance Holes
- Solution: Clean the throttle and balance holes.
- Excessive Operating Frequency or Expired Product Life
- Solution: Replace the solenoid valve with a more suitable product or upgrade to a newer model.
3. Other Common Issues
- Internal Leaks
- Cause: Check for damaged seals or improper spring assembly.
- Solution: Replace the seals or reassemble the spring properly.
- External Leaks
- Cause: Loose connections or damaged seals.
- Solution: Tighten the screws or replace the seals.
- Noise During Power-On
- Cause: Loose fasteners on the valve, voltage fluctuations, or uneven iron core surfaces with impurities.
- Solution: Tighten all loose fasteners, adjust the voltage to within the allowable range, and clean or replace the iron core if necessary.
4. Quick Field Diagnosis of Solenoid Valve Faults
When troubleshooting solenoid valve issues, you can perform the following steps for a quick diagnosis:
- Check for Coil Failure
- Procedure: Send an open or close signal to a two-position valve via the DCS system and listen for valve operation sounds. If no sound is heard, it indicates a problem with the coil.
- Solution: Check the wiring for loose or shorted connections. If the wiring is fine, measure the solenoid coil with a multimeter. If the coil is open, it indicates that the solenoid coil is burned out. This could be due to moisture causing insulation failure, resulting in excessive current and coil burn-out. Prevent water ingress into the solenoid valve to avoid this. Additionally, a hard spring, excessive counterforce, or insufficient coil turns can also cause the coil to burn out.
- If the Coil is Fine, Check the Valve Itself
- Procedure: If the coil is not the issue, inspect the solenoid valve itself. You can manually adjust the valve and check if it opens. If it opens, the coil is likely the problem, and you can replace it. If it doesn’t open, disassemble the valve and check for a stuck valve core or any debris blocking it.
- Solution: Disassemble and clean the solenoid valve. You can use CCL4 solvent for cleaning, or if unavailable, use gasoline or water. After cleaning, dry the valve with compressed air. When disassembling, be sure to record the sequence of parts, as improper reassembly can prevent the valve from functioning properly, even if the cleaning is done correctly.
Solenoid valve faults can arise due to various factors, but by understanding the common issues and solutions, you can quickly diagnose and resolve problems, ensuring the valve operates smoothly. Regular maintenance and cleaning will help extend the life of solenoid valves and reduce the frequency of failures. By performing proper operation and timely upkeep, you can ensure the stability and reliability of your solenoid valves and improve the efficiency of your systems.