Six Major Causes of Valve Seat Damage
Valve seat damage is a critical issue that affects valve performance, seal integrity, and the overall efficiency of fluid control systems. Understanding the causes of valve seat damage can help in selecting the right valves, preventing premature failure, and optimizing system reliability. In this article, we’ll discuss the six major causes of valve seat damage, their effects, and how to prevent them for a more durable and efficient valve system.
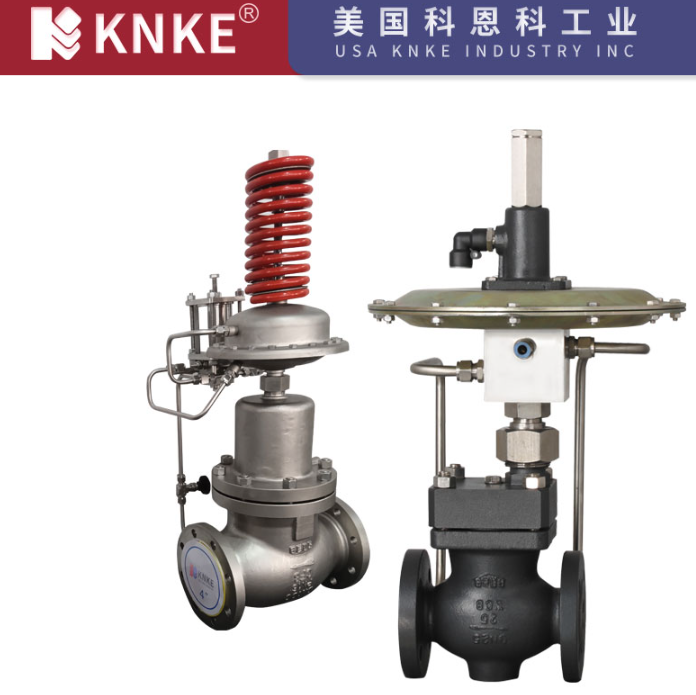
1. Poor Valve Seat Surface Machining Quality
One of the primary reasons for valve seat damage is poor surface machining. Defects like cracks, air pockets, and inclusions often stem from improper welding and heat treatment processes. If the welding process is not performed correctly, the composition of the alloy on the valve seat can be compromised, affecting its hardness and corrosion resistance.
Key Issues:
- Cracks, air pockets, or inclusions in the machining
- Uneven hardness caused by improper material selection or heat treatment
- Decreased corrosion resistance and sealing performance
To prevent valve seat damage from poor machining, it’s essential to choose a qualified supplier who follows precise manufacturing standards and to use materials that are appropriate for your specific working conditions.
2. Incorrect Valve Selection and Poor Operation
Incorrect valve selection or improper operation can lead to significant damage to the valve seat. For example, using a shut-off valve in applications that require a control valve can lead to excessive closing pressure, rapid valve closure, or incomplete sealing, causing erosion and wear on the valve seat.
Common Problems:
- Using the wrong valve type for specific applications
- Incorrect valve installation or failure to perform regular maintenance
- Premature wear from over-pressurization or fast closing
Ensure that the valve you select is suitable for the specific application, considering the media type, pressure, and flow characteristics. Proper installation and ongoing maintenance are also essential for maintaining valve integrity.
3. Chemical Corrosion of the Valve Seat
Chemical corrosion is another major cause of valve seat damage. When the medium in contact with the valve seat has corrosive properties, it can gradually degrade the material of the seat, compromising its sealing ability. Electrochemical corrosion can occur when there is a potential difference between different parts of the valve seat, exacerbating the damage.
Key Factors:
- Exposure to corrosive media, leading to material degradation
- Electrochemical corrosion caused by potential differences between the valve seat and other components
- Increased risk in valves handling highly reactive fluids or gases
To combat chemical corrosion, choose valve seats made from corrosion-resistant materials like stainless steel or alloy-based materials. Regular inspections and maintenance should be performed to detect early signs of corrosion.
4. Erosion from High-Velocity Media
Erosion occurs when the medium flows at high speed and causes particles to strike the valve seat, gradually wearing down the surface. High-velocity fluids, particularly abrasive or turbulent ones, can accelerate this process, leading to premature seat damage. Cavitation and vapor bubble collapse further exacerbate the erosion process by creating localized pressure spikes that damage the valve seat.
Common Erosion Causes:
- High-velocity flow or abrasive particles in the medium
- Cavitation or vaporization of the fluid causing pressure spikes
- Increased erosion when chemical corrosion is also present
For applications involving high-velocity or abrasive media, consider using harder valve seat materials or seats with protective coatings. Proper flow control and cavitation prevention techniques can also help minimize erosion.
5. Mechanical Damage During Valve Operation
Mechanical damage to valve seats typically occurs when there is friction between the sealing surfaces during the valve’s operation. As the valve opens or closes, it can create scratches, dents, or other types of surface damage, especially under high-pressure and high-temperature conditions. The phenomenon of galling (when the surfaces bond together) can cause severe damage to valve seats.
Potential Mechanical Damages:
- Scratches, dents, and gouges caused by friction
- Galling, where materials bond together and tear apart during valve movement
- Surface roughness that exacerbates wear and damage
To reduce mechanical damage, choose valve materials that are more resistant to galling and abrasion. Lubrication or the use of soft-seating materials can also help minimize friction and protect the sealing surfaces.
6. Fatigue Damage from Repeated Cycles
Fatigue damage is a common issue in valves subjected to frequent opening and closing cycles. Over time, the mechanical stresses from these repeated operations can lead to cracks or other structural damage to the valve seat. The constant stress on the valve seat can cause it to degrade, reducing its sealing performance. This is particularly common in high-temperature and high-pressure applications.
Symptoms of Fatigue:
- Cracking or chipping of the valve seat material
- Deformation of the valve seat due to repeated cycles
- Reduced sealing efficiency over time
To prevent fatigue damage, select valves designed for high-cycle applications and use materials that are resistant to fatigue. Regular maintenance and timely replacement of valve seats are crucial for avoiding long-term damage.
Preventing Valve Seat Damage
Valve seat damage can be caused by various factors, including poor machining, incorrect valve selection, chemical corrosion, erosion, mechanical damage, and fatigue. To extend the life of your valves and improve the overall reliability of your fluid control system, it is essential to choose the right materials, ensure proper installation, and perform regular maintenance.
Preventative Measures:
- Select valves that are designed for your specific application.
- Use corrosion-resistant and fatigue-resistant materials.
- Regularly inspect and maintain valves to identify early signs of damage.
- Ensure proper operational procedures to avoid mechanical damage.
By addressing these causes of valve seat damage proactively, you can significantly improve the performance and lifespan of your valves, ensuring a more efficient and reliable fluid control system.