Reasons for Using Extended Bonnet in Cryogenic Valves
Cryogenic valves are essential in many industries, particularly those dealing with low-temperature media. These valves, designed for temperatures from -40°C to -196°C, are critical in liquefied natural gas (LNG) and ethylene production. To maintain performance and safety, many cryogenic valves use an extended bonnet. This article will explain why extended bonnets are used and how they help maintain valve integrity.
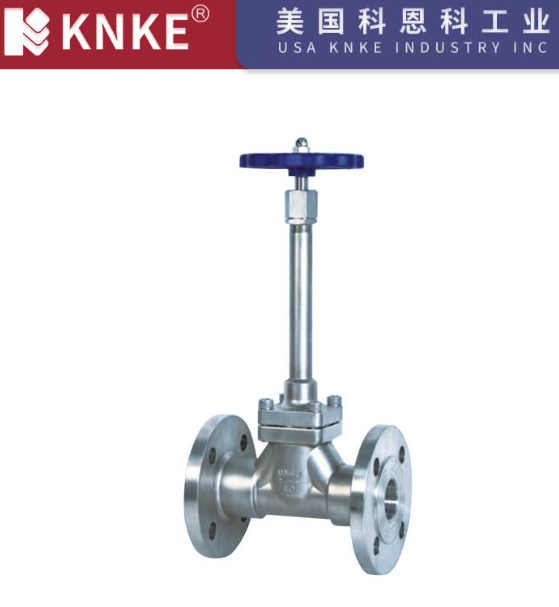
1. Easier Valve Component Replacement
In cryogenic plants, valves are often placed inside insulated “cold boxes” to keep temperatures low. Replacing valve components in these conditions can be difficult. However, the extended bonnet design makes it much easier.
With the extended bonnet, the valve’s main components can be removed and replaced without disassembling the valve body. The bonnet extends through the cold box wall, making it accessible from the outside. This design helps avoid dismantling the entire valve, preventing potential leaks from the cold box. It also ensures that the valve’s seals remain intact. As a result, valve maintenance becomes much more efficient.
2. Protecting the Valve’s Packing Gland
The packing gland in a cryogenic valve is crucial for maintaining a tight seal. This is especially important in cryogenic applications. Any leaks could lead to safety hazards, particularly with volatile media like LNG and liquid oxygen.
The extended bonnet helps protect the packing gland, keeping it insulated and preserving its sealing properties. Without insulation, the packing material could lose its elasticity at low temperatures, leading to leaks. Ice could also form around the packing, which would affect the valve stem’s operation. The extended bonnet ensures the packing gland stays at a temperature above 8°C. This prevents ice formation and ensures smooth operation. As a result, the risk of leakage is significantly reduced.
3. Facilitating Insulation for Cryogenic Energy Efficiency
Cryogenic valves require proper insulation to minimize heat transfer and maintain low temperatures. The extended bonnet provides the necessary space for insulation materials. This prevents heat gain, ensuring the valve keeps the media at the desired low temperature.
Insulating the valve is vital to prevent the vaporization of cryogenic media. For example, LNG, liquid hydrogen, and ethylene must remain at extremely low temperatures. If they warm up, they could rapidly expand, causing safety hazards. The extended bonnet makes it easier to apply insulation, reducing heat loss. This helps keep the valve in optimal operating condition and ensures safety.
4. Designed for Diverse Cryogenic Media
Cryogenic valves control various low-temperature media, including LNG, liquid oxygen, liquid hydrogen, and ethylene. These media expand quickly when exposed to higher temperatures, which can be dangerous. Therefore, cryogenic valves need to be robust and resistant to extreme conditions.
The extended bonnet design helps the valve function effectively in these harsh environments. The added length ensures the valve components remain insulated, minimizing temperature fluctuations. This ensures stable operation, even when handling volatile cryogenic media. Ultimately, the extended bonnet improves the valve’s ability to withstand these conditions and ensures reliable performance.
The extended bonnet design is essential for cryogenic valves used in low-temperature applications. It allows for easier maintenance, protects the valve’s packing gland, provides insulation space, and ensures the valve can handle a variety of cryogenic media. In industries like LNG production and ethylene manufacturing, this design is crucial for safety and reliability.
By using cryogenic valves with extended bonnets, industries can prevent leaks, reduce maintenance costs, and improve overall operational efficiency. The extended bonnet ensures the valve remains effective and safe, even in the most extreme conditions.