Key Points for Using and Maintaining High-Pressure Ball Valves
High-pressure ball valves play a critical role in fluid control systems in industrial pipelines. To ensure long-term stability and performance, users must follow certain guidelines and precautions during operation and maintenance. Below are the key points for using and maintaining high-pressure ball valves:
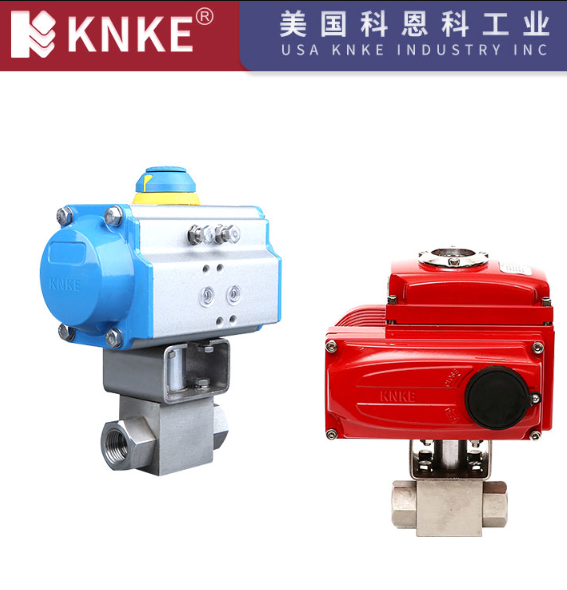
1. Pressurized Fluid Remains Inside the Valve Body in Closed State
Even when a high-pressure ball valve is closed, pressurized fluid may remain inside the valve body. Therefore, always ensure that the internal pressure is safely released before operation or maintenance to avoid leaks or damage.
2. Lubrication Requirements for High-Pressure Ball Valves
High-pressure ball valves typically use grease to ensure a tight seal between the ball and valve seat. The lubricant must be compatible with the valve’s metal components, rubber parts, plastic components, and the working medium. When the working medium is gas, specialized lubricants like T221 grease are recommended.
Grease should be applied to the following areas:
- Valve Stem Sealing and Friction Surfaces: Apply a thin layer of lubricant to reduce wear.
- Seal Groove Surfaces: A thin layer of grease can help improve the sealing performance.
- Rubber Seals: Lubricate rubber seals to extend their lifespan.
3. Disconnect Power or Air Supply Before Maintenance
Before maintaining the high-pressure ball valve, always disconnect the power or air supply. This ensures that the valve cannot accidentally activate during maintenance, ensuring the safety of maintenance personnel.
4. Separate Actuator from Bracket During Maintenance
Before performing maintenance, disconnect the actuator from the bracket to facilitate easier disassembly and inspection of the internal valve components.
5. Bolt Tightening Requirements During Assembly
When assembling the valve, ensure that the flange bolts are tightened symmetrically, gradually, and evenly. This ensures even distribution of force on the valve seat and prevents leakage or improper sealing.
6. Cleaning of Non-Metallic Components
During maintenance and assembly, all non-metallic components should be thoroughly cleaned. After cleaning, remove them immediately from the cleaning solution to avoid prolonged soaking. Once cleaned, allow the components to dry completely and ensure no contaminants, such as fibers or dust, remain before reassembly.
7. Cleaning and Drying Process
Use compatible cleaning agents to clean the high-pressure ball valve components. For valves using gas as a medium, gasoline (GB484-89) can be used to clean metal parts. Non-metallic components should be cleaned with pure water or alcohol. Ensure that no cleaning agents remain on the parts, and allow them to dry before reassembly.
8. Ensure No Contaminants Remain
During assembly, ensure that no metallic debris, oil, dust, or other contaminants are present on the valve components. The presence of foreign matter can lead to poor sealing or valve malfunction. All parts should be clean before assembly.
9. Release Pressure from Pipeline Before Disassembly
Before disassembling or decomposing the valve, always confirm that the upstream and downstream pipelines are depressurized and that the valve is in the open position. This will help prevent valve damage or accidental leakage during disassembly.
10. Cleaning Method and Precautions
For individual components that have been disassembled, use an immersion method for cleaning. For metal components that have not been disassembled, use a clean, fine cloth dampened with a cleaning agent (to prevent fibers from sticking to parts) to wipe the surfaces clean. During cleaning, ensure that all grease, dirt, glue buildup, and dust are removed.
Conclusion
Proper use and maintenance of high-pressure ball valves are essential for ensuring their long-term performance. By following the above key points, you can extend the valve’s lifespan, improve its efficiency, and reduce the likelihood of failure. Regular maintenance checks, precise lubrication, thorough cleaning, and adherence to safety measures are crucial for ensuring the valve’s safe and reliable operation.