Methods for Preventing Corrosion of Electric Butterfly Valves
Electric butterfly valves are commonly used in industries like water treatment, petrochemical, power generation, and food processing. They are known for their simple structure, ease of operation, and low maintenance costs. However, over time, these valves can suffer from corrosion due to environmental factors and the properties of the media they control. Corrosion can reduce valve lifespan and performance. Therefore, effective corrosion prevention is crucial to maintaining the valve’s functionality.
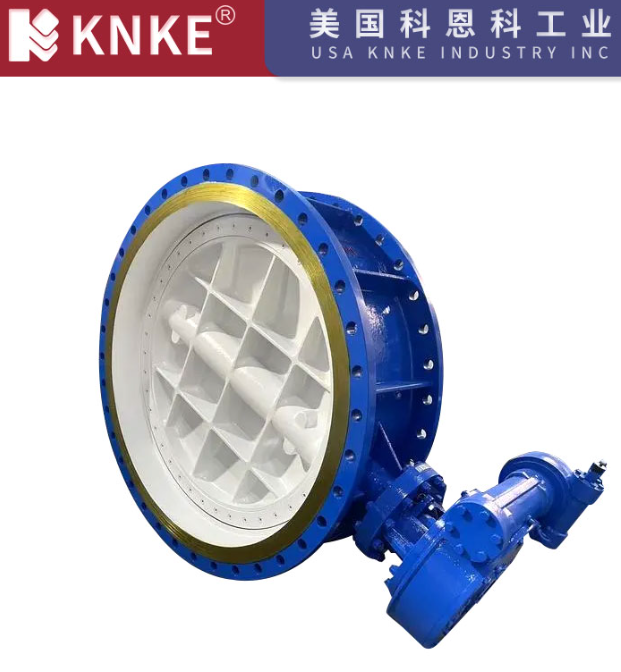
1. Electrochemical Corrosion Prevention
Electrochemical corrosion is a common issue for electric butterfly valves. It occurs when dust or metal particles accumulate on the valve surface. These particles can form a microbattery between the stainless steel and foreign metals. This leads to electrochemical reactions that damage the protective oxide layer, causing corrosion.
Prevention Methods:
- Regular Cleaning: Clean the valve surface frequently to remove dust and foreign particles. This helps prevent electrochemical reactions.
- Apply Anti-corrosion Coatings: Coating the valve surface with anti-corrosion materials strengthens its resistance to electrochemical corrosion.
- Use Corrosion-Resistant Alloys: Choose corrosion-resistant alloys for valve construction to reduce the risk of electrochemical damage.
2. Organic Corrosion Prevention
When organic substances, like juices or liquids, adhere to the valve surface, they can form organic acids in the presence of water and oxygen. Over time, these acids corrode the valve surface.
Prevention Methods:
- Timely Surface Cleaning: Regularly clean the valve surface to prevent organic substances from accumulating.
- Use Acid-Resistant Materials: Select materials that are resistant to organic acids, improving the valve’s corrosion resistance.
- Control Environmental Factors: Manage the water and oxygen levels in the environment to reduce the formation of organic acids.
3. Corrosion from Salts and Chemicals
Salts, acids, and alkalis can cause localized corrosion on the valve surface. This damages the valve and shortens its lifespan.
Prevention Methods:
- Limit Contact with Corrosive Substances: Minimize exposure to salts, acids, and alkalis to prevent corrosion.
- Regular Surface Treatment: Treat the valve surface to maintain its smoothness and reduce corrosion risks.
- Choose Corrosion-Resistant Materials: Use materials that resist damage from salts, acids, and alkalis.
4. Chemical Corrosion Prevention
Polluted air, containing sulfur compounds, carbon oxides, or nitrogen oxides, can cause chemical corrosion. When condensation forms on the valve, these gases react to create corrosive liquids like acetic acid.
Prevention Methods:
- Monitor Air Quality: Regularly check the air quality in the valve’s environment to reduce harmful gas concentrations.
- Apply Protective Coatings: Use high-performance coatings to protect the valve from chemical corrosion.
- Inspect and Maintain Regularly: Conduct routine inspections and maintain the valve to prevent coating damage and corrosion.
5. Routine Maintenance and Corrosion Prevention
Routine maintenance is essential for extending the valve’s life and preventing corrosion.
Prevention Methods:
- Scheduled Maintenance: Perform regular checks and clean the valve to avoid corrosion buildup.
- Use Anti-corrosion Coatings: Apply coatings to prevent external corrosion and improve wear resistance.
- Proper Storage: Store unused valves in dry, clean environments to prevent surface contamination.
Corrosion prevention is vital for the longevity and performance of electric butterfly valves. Selecting the right materials, applying protective coatings, and performing regular maintenance are key to preventing corrosion. By following these methods, you can significantly extend the valve’s lifespan and ensure its reliable operation in harsh conditions.